An In-depth Exploration of CNC PEEK, Vibrating Discs, and the Return of Workpieces to School: Understanding Their Significance and Applications in Modern Manufacturing
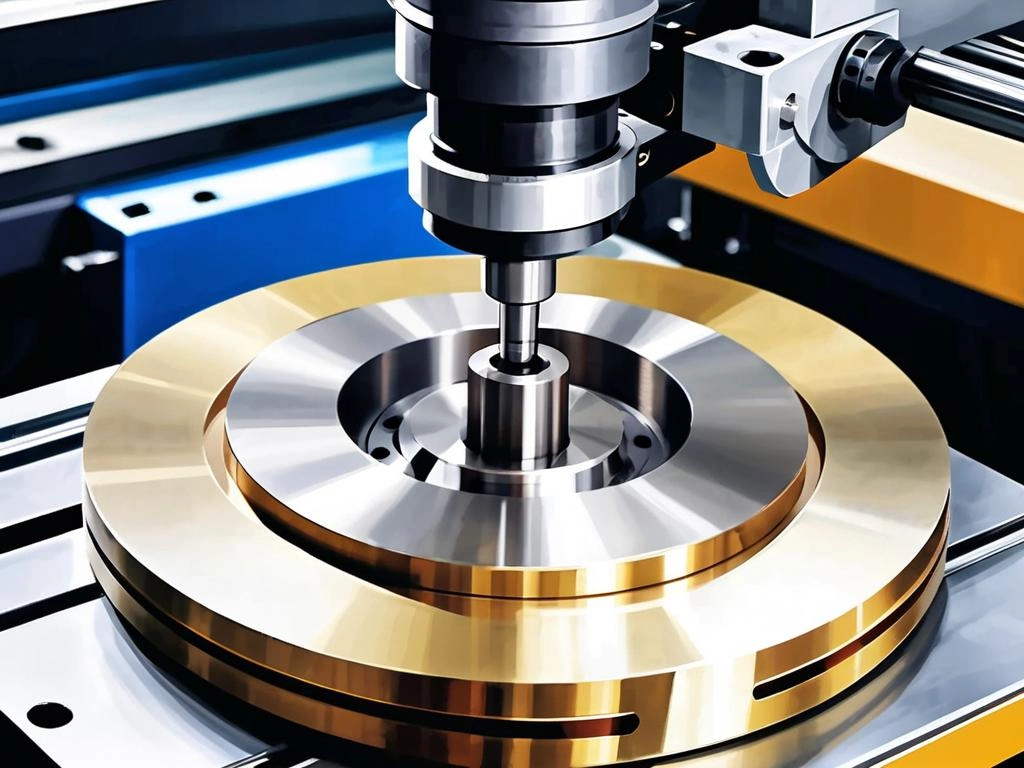
Introduction to CNC PEEK
CNC PEEK, which stands for Computer Numerical Control Polyether Ether Ketone, represents a remarkable advancement in the field of manufacturing. PEEK is a high-performance thermoplastic known for its exceptional mechanical properties, chemical resistance, and thermal stability. When combined with CNC technology, the precision and accuracy of machining PEEK components reach new heights.
Properties of PEEK Material
PEEK has a unique set of properties that make it highly desirable in various industries. It exhibits excellent strength-to-weight ratio, allowing for the production of lightweight yet durable parts. Its resistance to chemicals, including acids, bases, and solvents, makes it suitable for applications in harsh chemical environments. Moreover, PEEK can withstand high temperatures without significant degradation, maintaining its mechanical integrity even at elevated temperatures.
CNC Machining Process for PEEK
The CNC machining process for PEEK involves the use of computer-controlled machines to precisely cut, shape, and drill PEEK materials. This process ensures high accuracy and repeatability, resulting in consistent quality of the machined parts. Specialized cutting tools and machining parameters are often required to optimize the machining process and achieve the desired surface finish and dimensional accuracy.
Applications of CNC PEEK
CNC PEEK finds extensive applications in industries such as aerospace, medical, automotive, and electronics. In the aerospace industry, PEEK components are used in aircraft engines, interior parts, and structural components due to their lightweight and high-strength properties. In the medical field, PEEK is used for implants and surgical instruments due to its biocompatibility and resistance to sterilization processes. In the automotive industry, PEEK parts are used in engine components, transmission systems, and interior trims.
The Role of Vibrating Discs
Vibrating discs play a crucial role in the manufacturing process, particularly in the handling and sorting of small parts and components. These discs use vibrations to move and orient parts in a specific direction, facilitating their assembly or further processing.
Working Principle of Vibrating Discs
The working principle of vibrating discs is based on the generation of vibrations through an electromechanical system. The vibrations cause the parts placed on the disc to move in a circular or linear motion, depending on the design of the disc. The shape and surface features of the disc are carefully designed to guide the parts into the desired orientation.
Benefits of Using Vibrating Discs
One of the main benefits of using vibrating discs is their ability to automate the handling and sorting of parts, increasing production efficiency and reducing labor costs. They can handle a large number of parts in a short period, ensuring a continuous supply of parts for downstream processes. Additionally, vibrating discs can improve the quality of the assembly process by ensuring that the parts are properly oriented and positioned.
Applications of Vibrating Discs
Vibrating discs are widely used in industries such as electronics, automotive, and consumer goods manufacturing. In the electronics industry, they are used for the assembly of small electronic components such as resistors, capacitors, and integrated circuits. In the automotive industry, vibrating discs are used for the sorting and assembly of small parts like screws, nuts, and washers.
The Significance of Returning Workpieces to School
The concept of "returning workpieces to school" may seem unusual at first, but it has important implications in the context of education and training. In educational institutions, especially those offering technical and vocational programs, returning workpieces can serve as valuable teaching tools.
Educational Value of Returned Workpieces
Returned workpieces provide students with real-world examples of manufacturing processes and quality control. By examining the workpieces, students can learn about the various machining techniques used, the importance of dimensional accuracy, and the effects of different materials on the final product. This hands-on learning experience can enhance their understanding of manufacturing concepts and improve their practical skills.
Quality Improvement through Returned Workpieces
For manufacturers, returning workpieces to school can also contribute to quality improvement. By analyzing the returned workpieces, manufacturers can identify areas for improvement in their production processes, such as tool wear, machining errors, or material defects. This feedback can be used to optimize the manufacturing process and reduce the occurrence of defects in future production runs.
Collaboration between Industry and Education
The practice of returning workpieces to school promotes collaboration between industry and education. Manufacturers can work with educational institutions to develop curriculum and training programs that are aligned with the needs of the industry. This collaboration can ensure that students are equipped with the relevant skills and knowledge required by the manufacturing sector, bridging the gap between academia and industry.
In conclusion, CNC PEEK, vibrating discs, and the return of workpieces to school are all important aspects of modern manufacturing. CNC PEEK offers high-performance materials and precise machining capabilities, vibrating discs improve the efficiency of part handling and sorting, and the return of workpieces to school enhances education and promotes quality improvement. Understanding and leveraging these elements can lead to significant advancements in manufacturing processes and the development of high-quality products.