An In-depth Exploration of CNC Steel Products, Fuel Pipes, and the Issue of Blade Wear: Understanding Their Significance and Interrelationships
Overview of CNC Steel Products
What are CNC Steel Products?
CNC steel products are manufactured using Computer Numerical Control (CNC) technology. This advanced manufacturing process involves the use of computer programs to control the movement and operation of machinery. In the case of steel products, CNC machines can precisely cut, shape, and form steel materials with a high degree of accuracy and repeatability. CNC steel products find applications in a wide range of industries, including automotive, aerospace, construction, and machinery manufacturing. For example, in the automotive industry, CNC steel parts are used in engine components, chassis, and body structures, where precision and durability are crucial.
Advantages of CNC Steel Products
One of the key advantages of CNC steel products is their high precision. The computer-controlled machining process ensures that each part is manufactured to exact specifications, reducing the margin of error and improving overall quality. This precision also allows for complex geometries and intricate designs that would be difficult or impossible to achieve with traditional manufacturing methods. Additionally, CNC machining is highly efficient, enabling faster production times and increased productivity. It can also be easily automated, reducing labor costs and improving production consistency.
Quality Control in CNC Steel Product Manufacturing
To ensure the quality of CNC steel products, strict quality control measures are implemented throughout the manufacturing process. This includes regular inspection and testing of raw materials, monitoring of machining parameters, and final inspection of finished parts. Advanced inspection techniques such as coordinate measuring machines (CMMs) and non-destructive testing methods are used to detect any defects or deviations from the specified dimensions. By maintaining high-quality standards, manufacturers can produce reliable and durable CNC steel products that meet the demanding requirements of various industries.
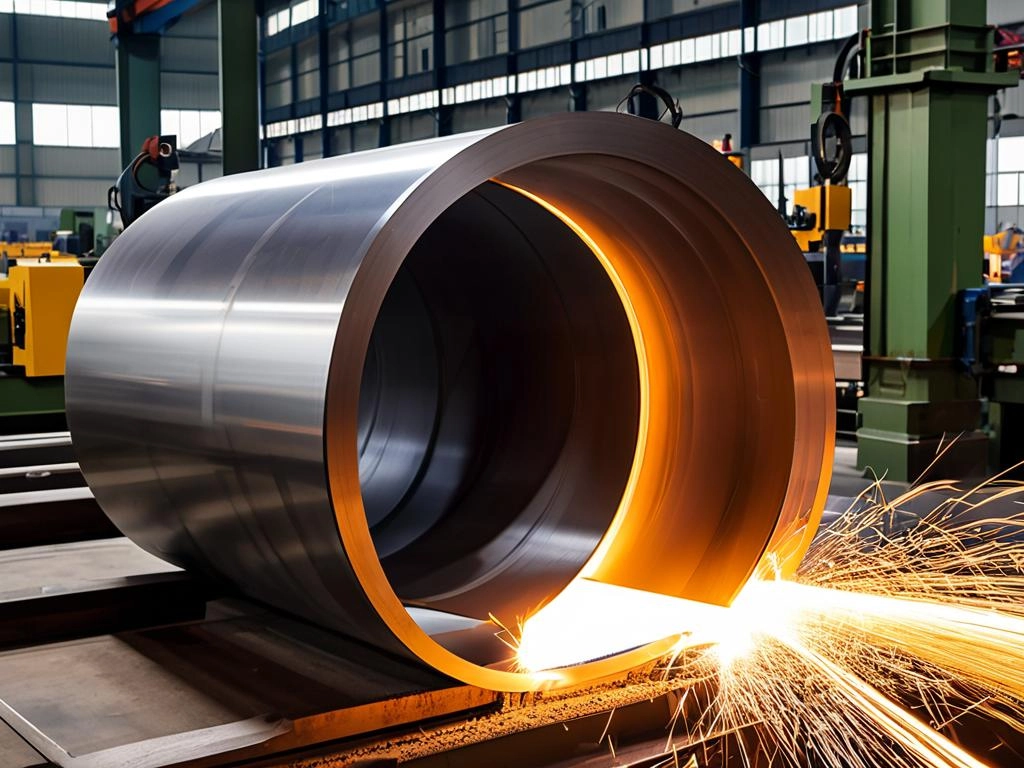
The Importance of Fuel Pipes
Function of Fuel Pipes
Fuel pipes play a vital role in the transportation of fuel from the fuel tank to the engine in various types of vehicles and machinery. They are responsible for delivering a consistent and reliable supply of fuel under different operating conditions. The design and construction of fuel pipes must take into account factors such as pressure, temperature, and chemical compatibility with the fuel being transported. For example, in automotive applications, fuel pipes need to withstand high pressures and temperatures generated during engine operation while remaining resistant to corrosion and degradation caused by the fuel.
Materials Used in Fuel Pipes
Common materials used for fuel pipes include steel, stainless steel, and various types of polymers. Steel fuel pipes are often preferred for their strength and durability, especially in high-pressure applications. Stainless steel offers additional corrosion resistance, making it suitable for use in harsh environments or with certain types of fuels. Polymer fuel pipes, on the other hand, are lighter in weight and can be more cost-effective in some applications. However, they may have limitations in terms of temperature and pressure resistance.
Safety Considerations for Fuel Pipes
Due to the potentially hazardous nature of fuel, safety is of utmost importance when it comes to fuel pipes. Any leakage or failure in the fuel pipe system can lead to serious accidents and fires. Therefore, fuel pipes must be designed and installed with proper safety features, such as pressure relief valves, leak detection systems, and appropriate sealing mechanisms. Regular inspection and maintenance of fuel pipes are also essential to ensure their continued safety and reliability.
Understanding Blade Wear
Causes of Blade Wear
Blade wear can occur due to a variety of factors. One of the primary causes is friction between the blade and the material being cut or processed. As the blade interacts with the material, the continuous rubbing and abrasion can gradually wear down the blade surface. The type of material being cut, its hardness, and the cutting parameters such as speed and feed rate can all affect the rate of blade wear. For example, cutting hard materials like steel or ceramics will generally cause more rapid blade wear compared to softer materials. Another factor contributing to blade wear is heat generation during the cutting process. Excessive heat can cause the blade material to soften and lose its hardness, leading to accelerated wear.
Effects of Blade Wear
Blade wear can have significant consequences on the performance and quality of the cutting or machining process. As the blade wears, its cutting edge becomes dull, resulting in reduced cutting efficiency and increased cutting forces. This can lead to longer processing times, higher energy consumption, and poorer surface finish on the machined parts. In severe cases, excessive blade wear can cause the blade to break or fail, resulting in costly downtime and potential damage to the machinery.
Preventing and Mitigating Blade Wear
To prevent and mitigate blade wear, several measures can be taken. One approach is to select the appropriate blade material and coating based on the specific application and material being cut. For example, carbide blades are often used for cutting hard materials due to their high hardness and wear resistance. Applying coatings such as titanium nitride (TiN) or diamond-like carbon (DLC) can further enhance the blade's wear resistance. Additionally, optimizing the cutting parameters, such as reducing the cutting speed and feed rate when cutting hard materials, can help reduce the rate of blade wear. Regular blade inspection and replacement when necessary are also important to maintain optimal cutting performance.
Interrelationships between CNC Steel Products, Fuel Pipes, and Blade Wear
CNC Machining of Fuel Pipes
CNC technology is often used in the manufacturing of fuel pipes. The precision and flexibility of CNC machining allow for the production of fuel pipes with complex shapes and tight tolerances. This ensures a proper fit and connection within the fuel system, reducing the risk of leaks. However, during the CNC machining process of fuel pipes, blade wear can be a concern, especially when working with hard steel materials. The use of appropriate cutting tools and optimized machining parameters is crucial to minimize blade wear and ensure the quality of the fuel pipes.
Blade Wear in CNC Steel Product Manufacturing
In the production of CNC steel products, blade wear can affect the dimensional accuracy and surface finish of the parts. As the blades wear, the machined parts may not meet the specified tolerances, leading to quality issues. To address this, manufacturers need to carefully monitor blade wear and replace the blades at the appropriate intervals. This helps maintain the high quality and precision of the CNC steel products.
The Impact of Fuel Pipes on CNC Machinery
The quality and reliability of fuel pipes can have an impact on the performance of CNC machinery. If the fuel pipes are damaged or leaking, it can lead to inconsistent fuel supply to the engine or power source of the CNC machine. This can result in fluctuations in power output, affecting the machining accuracy and efficiency. Therefore, ensuring the proper installation and maintenance of fuel pipes is essential for the smooth operation of CNC machinery.
Conclusion and Summary
In conclusion, CNC steel products, fuel pipes, and blade wear are all important aspects in various industries. CNC steel products offer high precision and quality, fuel pipes are crucial for the safe and efficient transportation of fuel, and blade wear can significantly impact the performance and lifespan of cutting tools. Understanding the interrelationships between these elements is essential for optimizing manufacturing processes, ensuring product quality, and maintaining the safety and reliability of machinery. By implementing appropriate measures to address blade wear, selecting the right materials for fuel pipes, and leveraging the capabilities of CNC technology, manufacturers can achieve better results and enhance their competitiveness in the market.