Discover the Excellence of CNC Machining near me for Precise Motor Rotor Manufacturing and the Intricate Assembly Process
Understanding CNC Machining near me
The Significance of Local CNC Machining Services
When it comes to CNC Machining near me, the convenience and benefits are numerous. Local CNC machining services offer quick turnaround times, reduced shipping costs, and the ability to have direct communication with the machining experts. This proximity allows for efficient collaboration, ensuring that your specific requirements for motor rotor production are met with precision and accuracy. For example, if you need to make last-minute adjustments or have urgent orders, having a local CNC machining facility can make all the difference.
Advanced Technologies in Local CNC Machining
Modern CNC machining near me utilizes state-of-the-art technologies. These advanced machines are capable of handling complex geometries and tight tolerances required for motor rotor manufacturing. With features like high-speed spindles and multi-axis capabilities, they can produce intricate rotor designs with exceptional surface finishes. This level of technological sophistication ensures that the motor rotors are of the highest quality, meeting the demanding standards of various industries.
The Intricacies of Motor Rotor Design
Key Design Considerations for Motor Rotors
Motor rotor design is a critical aspect of the overall performance of an electric motor. Factors such as the number of poles, the material used, and the shape of the rotor all play a significant role. For instance, the choice of magnetic materials can affect the motor's efficiency and power output. Additionally, the design must take into account factors like heat dissipation to prevent overheating during operation. A well-designed motor rotor can enhance the motor's performance, reliability, and lifespan.
CNC Machining's Role in Motor Rotor Design
CNC machining plays a crucial role in bringing motor rotor designs to life. It allows for precise shaping and sizing of the rotor components, ensuring that they fit together perfectly. The ability to machine complex shapes with high accuracy means that designers have more freedom to innovate and optimize the rotor design for better performance. CNC machining also enables the production of consistent and repeatable parts, which is essential for mass production of motor rotors.
The Assembly Process of Motor Rotors
Preparing the Components for Assembly
Before the assembly process begins, the individual components of the motor rotor need to be carefully prepared. This includes cleaning, inspecting, and sometimes coating the parts to ensure proper functioning. For example, the magnetic poles may need to be coated with a protective layer to prevent corrosion. The precision machined parts from the CNC machining process are then sorted and organized according to the assembly sequence.
The Step-by-Step Assembly Procedure
The assembly of a motor rotor is a meticulous process. It typically starts with the installation of the shaft, followed by the attachment of the rotor core and the magnetic poles. Special tools and fixtures are used to ensure that the components are aligned correctly. The winding of the coils is another crucial step, as it determines the electrical characteristics of the motor. Finally, the rotor is balanced to minimize vibrations during operation. Each step in the assembly process requires careful attention to detail to ensure the final product meets the required specifications.
Quality Control in the Assembly Process
Quality control is of utmost importance during the motor rotor assembly process. Various inspection and testing procedures are carried out at different stages to detect any defects or deviations from the design specifications. This includes dimensional checks, electrical tests, and performance evaluations. Any faulty components or assemblies are identified and corrected promptly to ensure that only high-quality motor rotors are produced. By maintaining strict quality control standards, manufacturers can guarantee the reliability and performance of their products.
Benefits of Optimized CNC Machining and Assembly
Improved Motor Performance
When CNC machining and the assembly process are optimized, the resulting motor rotors offer improved performance. The precise manufacturing and accurate assembly ensure that the rotor operates smoothly and efficiently. This leads to better power output, reduced energy consumption, and longer motor lifespan. For applications where motor performance is critical, such as in industrial machinery and electric vehicles, the benefits of optimized CNC machining and assembly are even more pronounced.
Cost Savings and Efficiency
Optimized CNC machining and assembly processes can also result in cost savings and increased efficiency. By reducing waste, minimizing errors, and improving production throughput, manufacturers can lower their production costs. Additionally, the use of advanced CNC machining technologies allows for faster production times, enabling manufacturers to meet customer demands more quickly. This combination of cost savings and efficiency makes CNC machining and optimized assembly processes a competitive advantage in the market.
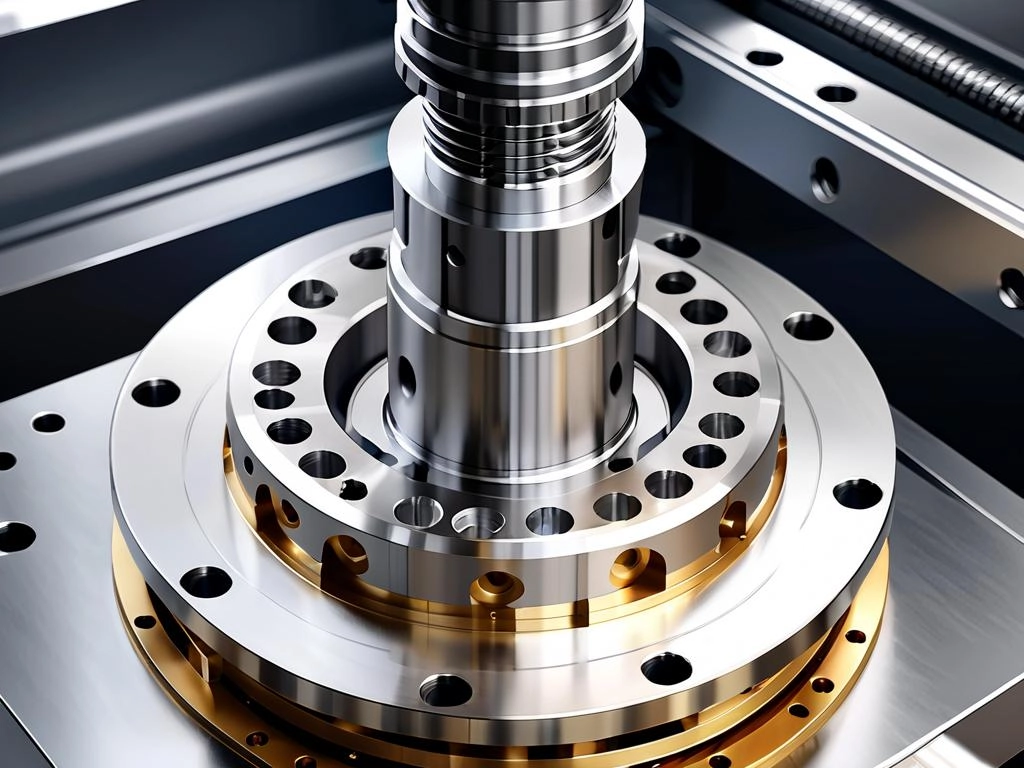
Conclusion and Future Trends
Summary of Key Points
In conclusion, CNC Machining near me offers significant advantages for motor rotor manufacturing and assembly. The combination of advanced technologies, precise machining, and meticulous assembly processes ensures the production of high-quality motor rotors. The benefits include improved motor performance, cost savings, and increased efficiency. As industries continue to demand higher performance and more reliable motors, the importance of CNC machining and optimized assembly processes will only grow.
Future Trends in CNC Machining and Motor Rotor Assembly
Looking ahead, we can expect to see further advancements in CNC machining and motor rotor assembly. This may include the development of even more sophisticated machining technologies, such as additive manufacturing combined with CNC machining. There will also be a greater focus on automation and intelligent manufacturing, where machines can self-adjust and optimize the assembly process based on real-time data. These trends will continue to drive innovation and improve the quality and performance of motor rotors in the future.