Analysis Of Corrosion Resistance And Processing Technology Of 4J36 Expanded Alloy
Introduction to 4J36 expansion alloy
4J36 expanded alloy, also known as Invar36, is a nickel-iron alloy with a low expansion coefficient and contains about 36% nickel. Mainly used in situations where extremely low thermal expansion coefficient is required. The thermal expansion coefficient of 4J36 alloy is close to zero in the range of -100℃ to 100℃, and it is widely used in high-tech fields such as precision instruments, electronic components, and aerospace. In addition to the control of the thermal expansion coefficient, the corrosion resistance and processing technology of 4J36 expansion alloy also have an important impact on its service life and performance.
Analysis of Corrosion Resistance of 4J36 Expanded Alloy
Since 4J36 expanded alloy contains high nickel and iron elements, its corrosion resistance has become an important indicator to pay attention to in certain environments.
1. Performance in atmospheric corrosive environment
In conventional atmospheric corrosion environments, 4J36 expanded alloy exhibits moderate corrosion resistance. This is mainly due to its nickel content. The presence of nickel element can form a nickel oxide film on the surface, providing a certain antioxidant effect. Compared with other high-nickel alloys such as Monel and Inconel series, the nickel content of 4J36 is slightly lower, resulting in less outstanding atmospheric corrosion resistance.
In the ordinary atmospheric exposure test, after 120 days of exposure test at 25°C and relative humidity of 65%, 4J36 alloy showed slight oxidation spots on the surface, with a corrosion rate of 0.005mm/year. This shows that its corrosion resistance under normal atmospheric conditions is acceptable, but its corrosion resistance needs to be strengthened in humid or heavily polluted environments.
2. Performance in acidic and alkaline environments
The corrosion resistance of 4J36 expanded alloy in acidic environments is relatively limited, especially in sulfuric acid and hydrochloric acid solutions. For example, in a 5% sulfuric acid solution, the corrosion rate of 4J36 is 0.1 mm/year, which is much higher than its corrosion rate in the atmospheric environment.
On the contrary, in alkaline environment, the corrosion resistance of 4J36 expanded alloy is improved. In a 5% sodium hydroxide solution, after a 240-hour immersion test, there were almost no obvious corrosion marks on the surface of the 4J36 alloy. This shows that it has good corrosion resistance in alkaline environments and is suitable for certain specific alkaline working conditions.
3. Marine environmental performance
In marine environments with high chloride content, the corrosion resistance of 4J36 expanded alloy shows obvious deficiencies. Chloride ions in seawater will destroy the nickel oxide protective film on the surface, causing pitting and crevice corrosion of the alloy. After a 100-hour corrosion test of 4J36 expanded alloy in a 3.5% NaCl solution, the corrosion depth reached 0.03mm, indicating that it does not have ideal corrosion resistance in a marine environment.
Analysis of processing technology of 4J36 expanded alloy
The particularities of the physical properties and chemical composition of 4J36 expanded alloy need to be considered during processing. Reasonable processing technology can ensure good dimensional stability and surface quality.
1.Heat treatment process
Heat treatment is a key step in the processing of 4J36 expanded alloy. After the alloy is cold rolled or cold drawn, aging treatment is usually required to eliminate the internal stress generated during the processing and restore the microstructure of the material.
Usually, the annealing temperature of 4J36 expansion alloy is between 830℃ and 880℃. The annealing time is usually controlled between 2 and 4 hours, and the method of slow cooling to room temperature is used. This process can effectively improve the plasticity and toughness of the alloy and ensure the stability of its low thermal expansion coefficient.
Experimental data shows that after annealing at 850°C, the thermal expansion coefficient of 4J36 expanded alloy is 1.5×10⁻⁶/°C in the range of 25°C to 100°C, which is significantly better than that of alloy materials without heat treatment. treat.
2.Cold working process
4J36 expanded alloy has high toughness and ductility, so it is suitable for cold working processes such as cold rolling and cold drawing. Due to the high nickel content, work hardening is prone to occur during cold working, which affects subsequent processing performance and surface quality.
In order to reduce the impact of work hardening, the deformation amount should be controlled not to exceed 50% during cold rolling, and intermediate annealing should be added in the intermediate stage to release the internal stress accumulated during the processing. Usually, the intermediate annealing temperature is controlled at 600°C to 650°C, and the annealing time is 1 to 2 hours.
After cold working, the mechanical strength of 4J36 expanded alloy can be significantly improved. For example, after 50% cold rolling deformation of 4J36 alloy, the tensile strength can be increased from the original 450MPa to more than 700MPa, and the hardness can be increased from 160HV to 220HV.
3.Welding process
4J36 expanded alloy can be joined by a variety of welding processes, including tungsten arc welding (TIG), electron beam welding and laser welding. Due to the high nickel content in its alloy composition, welding cracks are prone to occur during welding, especially when welding large thickness materials.
In order to reduce the occurrence of welding cracks, it is recommended to preheat the material before welding, and the preheating temperature should be controlled between 200°C and 300°C. Slow cooling should be carried out after welding to avoid thermal stress concentration caused by rapid cooling and rapid heating of the material. Post-weld treatment can use aging treatment at around 700°C, which can effectively eliminate residual stress in the welding area and improve the stability of the welded joint.
Experiments show that after preheating and post-welding treatment, the tensile strength of the 4J36 welded joint reaches 450MPa, which is similar to the base material, and the thermal expansion coefficient of the welding zone does not change significantly.
Preheating and subsequent aging treatment should be adopted during the welding process to ensure the mechanical properties and crack resistance of the welded joints. Information on various alloy materials is updated daily, and consultation and exchange are welcome. (ljalloy.com)
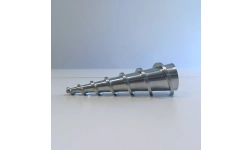