Impeller Finishing Innovatively Solves Problems
Ma Changhao, a CNC operator in the rotor workshop of Shengu Group - using innovation to solve the problem of impeller finishing
[Unique skill highlights]
Ma Changhao: Engaged in impeller finishing for more than 20 years. He invented more than 100 new methods such as the "eight-point average centering method" and the combination of forward and reverse cutting. It also proposed innovative solutions such as thin-walled sleeve processing methods and tooling research, and impeller forging size optimization, and participated in more than 400 innovative projects. His products are used in many large air compressor equipment.
Make a circle around the original impeller, observe the appearance carefully to confirm that there are no defects, then hoist it to the machine tool, measure the size, mark, align, select turning tools and programs, and arrange the process flow requirements according to the drawings... 7:20 in the morning, In the rotor workshop of Shengu Group Co., Ltd., Ma Changhao (see picture, provided by the interviewee) is busy around an original impeller.
In front of him is an impeller with a diameter of 1.75 meters, which is 0.25 meters beyond the maximum processing diameter of the machine tool. It was the largest impeller he had ever machined. The difficulty lies in installing and securing it. "This kind of impeller has a large diameter and can only block the tooling shaft. The tooling shaft is very thin and can easily affect the accuracy due to vibration." In order to solve this problem, Ma Changhao made four arc clamping blocks in advance and made a An extension rod. Used for reinforcement. When turning, he concentrated on controlling the speed of the machine tool and observed and adjusted the position of the turning tool at any time.
Under his operation, the lathe started, and the turning tool came into contact with the surface of the impeller, cutting off rolls of iron filings and emitting wisps of light smoke. After a few turns, the arc of the impeller becomes more and more perfect.
Ma Changhao is a CNC operator in the rotor workshop of Shenggu Group. His job was impeller finishing. This work is extremely demanding, and the working error must be controlled within 0.02 mm; if you are not careful, the impeller worth hundreds of thousands to millions of yuan may be scrapped.
Ma Changhao, 46 years old, has been engaged in impeller finishing work for more than 20 years, while constantly consolidating the theoretical foundation. He studied all the way from high school to a bachelor's degree. Not only is he familiar with craftsmanship, but he is also often innovative. His products are used in many large air compressor equipment.
In 2019, the rotor workshop piloted a digital and intelligent production line. The workstation computers and mobile phones in front of each CNC lathe are like resource libraries. Click the screen to view high-definition electronic drawings. Ma Changhao faced the screen and clicked "Start", and the production status changed from "Shipping" to "Processing"; after the turning was completed, he clicked "Finish" again, and the workpiece automatically entered the next process.
In order to skillfully operate this intelligent system, Ma Changhao specially studied online courses such as 5S on-site management and practical experience, office software training, etc. At the beginning of 2022, he proposed innovative solutions such as thin-walled sleeves, processing methods and tooling research, and impeller forging size optimization.
"To deal with various problems on the intelligent production line, we cannot do without the intelligence of the operators." Ma Changhao has been working on machine tools for more than 20 years and has a unique understanding of intelligent production lines. "It still requires physical labor to get to the most delicate spots." That's it. The angle of the impeller, the design of the cutouts, and the hardness of the material all require people to feel it. Stroking the processed workpiece, Ma Changhao said that perfectly processing a workpiece is like carving a work of art, which requires patience and meticulousness.
Dare to innovate and be good at innovation is one of the concepts that Ma Changhao has always adhered to. When the Kamiya Group was manufacturing 100,000 air separation compressors, the outer circle of the impeller was tilted and could not be clamped on the machine tool. Ma Changhao independently designed a set of exquisite arc clamping blocks and angle clamping pads based on the angle of the impeller. Tool successfully solved the problem. With a set of small tooling, the processing cost of each impeller was saved by more than 40,000 yuan.
Eliminating the imbalance of traditional impellers requires manual grinding, which is prone to dust generation, high labor intensity, low efficiency, and poor quality. Ma Changhao discovered a way to eliminate the imbalance in turning. He first found the deviation of the impeller, and then programmed, simulated, trial-cut, and cut the impeller according to the imbalance amount. Finally, judge whether the grams of iron filings removed are consistent with the unbalanced amount. , "A thread, a ruler, a pen, and a knife solved the big problem of impeller balance!"
Proposed the "eight-point average centering method", explored the processing method of combining forward and reverse cutting, solved the problems of bumps and scratches in impeller processing, and solved the problem of pre-milling of overweight products... In the past 20 years, Ma Changhao invented He has developed more than 100 new methods and participated in more than 400 innovation projects; saving the group tens of millions of yuan in production costs and creating benefits of more than 6 million yuan every year.
When performing urgent, dangerous and heavy tasks, Ma Changhao often comes to the workshop from home before dawn; he likes seemingly ordinary and boring work; he often teaches his new skills to his apprentices without reservation. and fellow workers. Under his leadership, the overall processing efficiency of the impeller processing group has been significantly improved in recent years. "There is no secret. Just stick to your job and do your job conscientiously." Ma Changhao said.
(Reporter Xinyang Liu Jiahua)
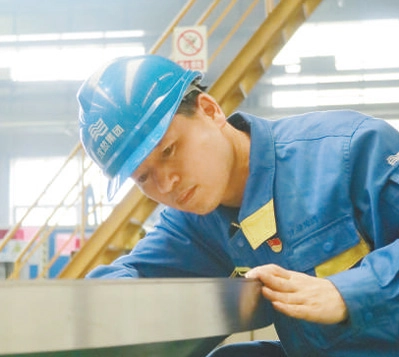