Cold Map: The Most Difficult Core Metal Processing Method Is Launched By Circular Management. Do You Know The Principle?
Have you ever been curious, how do you turn a simple round tube into a square tube? The answer is cold pull technology. The sound of this mysterious process actually plays an important role in the field of metal processing.
Cold maps are not only changes in shape, but also involve improvement of metal strength and hardness, and are widely used in automotive, aviation and other industries. Today, we discuss the principles, history and its application in modern society.
The basic principles and processes of cold pull
The charm of the cold pull process is that it does not require high temperature conditions, and can reshape the metal form by strong squeezing and stretching. At normal temperature, the plasticity of metal is low, but this process can be effectively used through cold pull technology. The basic principle of cold pull is to stretch or compress metal materials through holes or molds to make them deform plastic, thereby changing its shape and size.
During the cold pull process, when the metal material is through the mold, its internal crystal structure has changed a lot. Because it does not involve high temperature, the crystal world of the metal is better arranged, which greatly improves the strength and hardness of the metal. This change not only improves the physical characteristics of materials, but also makes its shape more accurate and reliable. In this way, even a simple shape such as circular tube can be turned into a square tube after the cold pull, showing amazing deformed ability.
The power required during the cold pull process is very huge, and the pressure of the metal itself usually requires several times. This also explains why the Cold Pull -OUT is mainly used for components with high intensity requirements, such as the driver shaft of a car. These components not only require wear resistance, but also need to bear huge impact and pressure, and the cold pull process can only meet these needs.>
It is worth mentioning that cold pull is not suitable for all metal materials. When selecting alloys, it is necessary to consider its plasticity and strength characteristics to ensure that processing can be completed without rupture or excessive deformation. Common metals suitable for cold charts include steel, aluminum and some copper alloys.
History and evolution of cold pull-craftsmanship
Cold painting technology has a long history in China, and its application can be traced back to more than 300 years ago. In the "Kai" of the Ming Dynasty, the detailed records of metal processing mentioned some methods similar to modern cold pull technology. This historical background not only shows the wisdom of ancient Chinese craftsmen, but also shows the gradual development of cold pull technology in development.>
With the emergence of the industrial revolution, the Cold Pull -OUT technology has been widely used. From the end of the 19th century to the beginning of the 20th century, Europe and the United States began to use cold pull technology to create high -precise mechanical parts. Especially in the automotive manufacturing industry, due to its outstanding mechanical performance and cost advantage, cold buckle parts have gradually replaced many traditional processing methods.
After entering the 21st century, with the development of technology, cold pull technology continued. The introduction of new mold materials and processing technologies makes the cold pull process more efficient and accurate. At the same time, the combination of computer -aided design (CAD) and computer CNC (CNC) technology also provides new possibilities for cold pull technology innovation. The advancement of these technologies not only improves production efficiency, but also makes complex shapes possible.
In the process, cold pull technology also faces challenges. With the attention of global environmental protection and sustainable development, how to reduce energy consumption and waste resources when ensuring product quality has become a problem in the industry. Many companies actively explore this goal by optimizing the production process and introducing environmental materials.
The difference between cold and warm, warm and warm
It sounds similar to cold, heat and warmth, but they are very different in terms of application and processing conditions. First, cold pull at room temperature and heat at high temperature. Thermal pulse is suitable for processing those metals with high melting points and poor plasticity, such as tungsten and molybdenum. Under high temperature conditions, the plasticity of these metals has been significantly improved, making stretching and forming easier.>
The warm pulse is between cold and hot pull, which is usually used for alloy tools that are difficult to deform but not suitable for processing at high temperature. The temperature is treated at medium temperature to effectively balance the plasticity and strength of the metal, and it is suitable for those who need fine treatment but not heated to prevent materials.>
Different treatment methods have their own specific application areas. For example, heat absorption is usually used in the aerospace industry, because many aviation materials need high temperature to resist and have high strength. Cold charts are more common in the automotive industry, because the processing parts not only have high strength, but also accurate size, which is suitable for the transmission system components used to bear a large amount of load.
It is worth noting that the problems and challenges of these three methods are also different. Hot needs to control high temperature environments, which may lead to excessive energy consumption, and need to use huge power to treat cold force at room temperature to form metal formation. These challenges have promoted material scientists and engineers, and constantly seek new technologies to optimize these processes.
Use cold pull crafts in modern society
With the development of science and technology, the process of coldness has penetrated into various industries and shows its irreplaceable importance. In the automotive industry, cold pull parts such as transmission, suspension system components, and gears not only require high precision, but also require good fatigue strength and abrasion resistance. Through the cold chart, these parts can reduce weight while ensuring performance, thereby improving vehicle efficiency.>
In the field of aerospace, cold glue also plays a key role. Many aircraft structures and engine components are manufactured during cold pull to ensure that they can still maintain stable performance under extreme conditions. For example, some support rods in the aircraft wing are made of cold pull technology, which is light and strong.
The medical equipment industry has also gradually adopted cold drawing technology. For example, metal components used for brackets and catheter manufacturing can achieve higher accuracy and surface smoothness through cold pull technology, thereby improving the reliability and safety of the product. This is essential for improving the performance of medical equipment.
With the development of emerging materials, cold drawing technology is constantly expanding its application scope. The combination of composite materials and new alloys makes cold water not limited to traditional metal processing, but also expands to more fields. This trend shows that future cold drawing technology will be used with more new materials to bring us more innovative products.
Cold pull technology and sustainable development
In the context of advocating global sustainable development, cold pull technology itself has been exploring how to reduce waste of resources and energy consumption. Because it does not require high temperature heating, cold pull is more environmentally friendly. But this does not mean that we can stop innovation.>
Modern enterprises achieve more effective energy use by optimizing the production process. For example, by improving mold design and using more advanced materials, the energy required for the operation of the machine can be reduced, while prolonging the life of the mold and reducing maintenance costs. This not only improves production efficiency, but also reduces waste caused by mold wear.
More and more companies have begun to pay attention to the concept of circular economy. Under this framework, through recycling and reuse of abandoned metal materials, it can not only reduce the demand for raw materials, but also reduce production costs. This method reduces the problem of resource shortage to a certain extent and also reduces the environmental impact in the production process.
Another development direction worthy of attention is the application of digital technology in cold pull technology. By introducing the Internet of Things (IoT) technology, manufacturers can monitor each link in the production process in real time in order to discover and solve problems in time. This can not only improve the quality of production, but also effectively reduce the waste of resources caused by operating errors.
In the long run, as environmental protection regulations are becoming more and more stringent, how to further improve the performance of cold -pull technology in environmental protection will become an important issue facing the industry. Through technological innovation and management optimization, I believe that in the future, we can see more green manufacturing models appear in cold pull technology.
The impact of cold painting crafts on employment structure and technical requirements
With the widespread application of cold drawing technology in various industries, it also has a profound impact on employment structure and technical requirements. First of all, because the process of cold pull has high requirements for equipment and operation technology, higher requirements have been put on the skills level of operators. Skilled skills such as the mold design CNC parts, equipment maintenance and quality control have become the basic conditions for employees.
With the development of automation and digital technology, the Cold Pull production line has introduced more and more new generations of equipment. This requires employees not only to have traditional skills, but also to master related software operation functions to control modern equipment for production. Therefore, skill training has become an important area for the company's attention and improves employee skills through continuing education to cope with changing market needs.
The development of cold pull technology may also affect the employment market of the traditional metal processing industry. Because of its high efficiency and low energy consumption characteristics, many companies may tend to use cold pulls instead of other processes. This change may lead to some inefficient and high energy consumption, and create new opportunities for high -value positions.
With the increase in the demand for environmental protection in society, CNC Services, those who can master green manufacturing technology will have an advantage in the market. Therefore, people engaged in the metal processing industry need to constantly update their knowledge reserves to adapt to new challenges brought about by changes in environmental protection regulations. At the same time, this also provides a new direction for education institutions. By cultivating a new generation of engineers with awareness of environmental protection, it helps the industry's sustainable development.
As a unique and powerful metal processing method, the cold drawing process not only plays an important role in the industrial field, but also continues to meet the development needs of modern society. From the long -term establishment method to combining the concept of modern technology and environmental protection, cold pull is writing a wonderful development process.
With the continuous development of technology, we have reasons to believe that the cold pulse process will continue to lead the development direction of the metal processing industry, thereby bringing us more innovation and possibilities. In daily life, we may be able to consider how to learn from the principles reflected in these advanced processes to better realize the balance between resource utilization efficiency and environmental protection.
`` `` `` ``
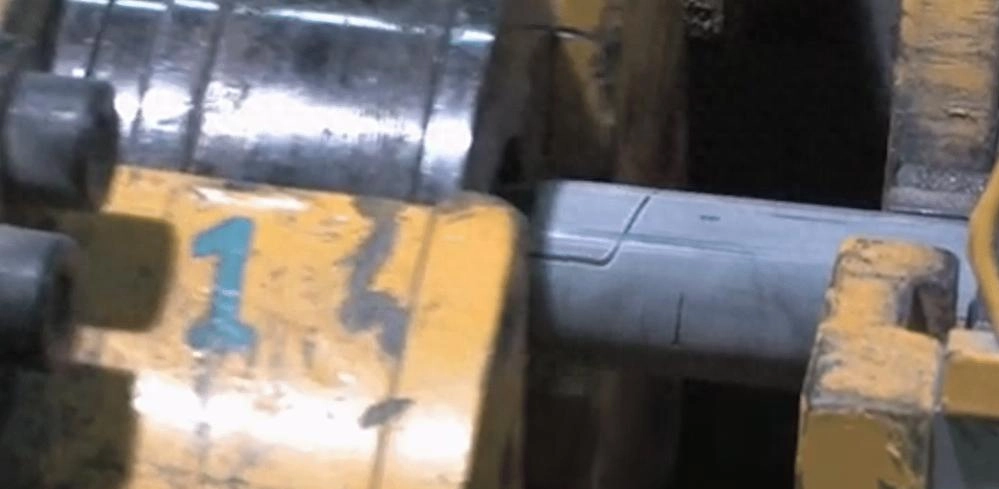