Which Machine Tool Brands Are The First To Deploy Titanium Alloys With Extremely High Processing Thresholds?
With the development of titanium alloys, the increase in the variety of titanium materials and the reduction in prices, the application of titanium in civil industry has doubled. The CFDA divides medical devices into three levels according to their safety from high to low, and each is subject to the supervision and management of the three levels of government. Implants made of titanium and titanium alloy materials belong to the third category of medical devices and are high-value consumables. .
Unparalleled biocompatibility, titanium alloy has become an "Internet celebrity" in the medical materials industry
Titanium alloys are used in the medical field because of their high strength, low density, non-toxicity, good biocompatibility, and corrosion resistance.
When human facial tissue is severely damaged cnc faq, local tissue repair requires surgical implants. Titanium alloy has good biocompatibility and required strength, making it an ideal material for human facial tissue repair.
It is reported that Lin Zhiying used titanium metal internal fixation for facial surgery and titanium alloy implant surgery for arm surgery.
In addition, because titanium alloy is close to human bones, it has good biocompatibility with human tissues, has no toxic side effects, and has advantages that other materials cannot match. Therefore, it has become an ideal choice for artificial joints, bone trauma, spinal orthopedic internal fixation systems, and dental implants. It is the material of choice for medical products such as body parts, artificial heart valves, interventional cardiovascular stents, and surgical instruments .
But on the other hand, titanium alloys are also recognized as difficult-to-machine materials. Due to its low wear resistance and process performance, machine tools and equipment dedicated to its deep processing are also constantly being upgraded.
What are the difficulties in titanium alloy processing?
The four characteristics of titanium alloys, including low thermal conductivity, severe work hardening, high affinity with cutting tools, and small plastic deformation, are the essential reasons why titanium alloys are difficult to process. Its cutting index is only equivalent to 20% of that of free-cutting steel.
The thermal conductivity of titanium alloy is only about 16% of that of 45# steel. The heat cannot be conducted out in time during processing, resulting in local high temperature on the cutting edge (the tool tip temperature during processing is more than twice that of 45# steel), which can easily cause diffusion wear of the tool.
The work hardening phenomenon of titanium alloy is obvious, and the surface hardening layer is more serious than that of stainless steel, which will bring certain difficulties to subsequent processing, such as increased tool boundary damage.
Strong bonding with titanium-containing carbides.
It is about 1/2 of the elastic modulus of 45 steel, so the elastic recovery is large and the friction is serious. At the same time, the workpiece is also prone to clamping deformation.
Advanced manufacturing solutions for efficient machining of titanium alloys
As domestic high-end application scenarios and potential market space for titanium alloys may gradually expand, global machine tool equipment manufacturers have provided numerous professional solutions.
Mazak i-150>
The i-150 advanced multi-tasking machine delivers maximum versatility, high precision and throughput for small, complex parts. The machine combines the capabilities of a high-performance turning center and a full-service machining center to produce parts in a single unit. Programmable workpiece handling equipment allows milling operations to be performed on the back side. This machine configuration minimizes clamping, machining, handling and non-cutting time. The machine can easily machine solid or cast parts (chuck or bar stock), round parts or fully prismatic parts for high profile parts. Suitable for processing osseointegration plates, bolts, artificial joints and other implanted devices.
Makino Makino a1 series horizontal machining center>
The maximum torque of its A63 spindle is 303N.m, and the A100 high-torque spindle can reach 1202N.m. High-torque spindles can be widely used in U-shaped drills, face milling cutters, corn milling cutters and other large cutting load cutting tools, and are suitable for industrial parts with difficult-to-cut materials. Materials such as stainless steel, ductile iron, and titanium alloys enable efficient material removal. In addition, the spindle runout and bed structure accuracy of the high-precision A1 series machine tools can effectively ensure the coaxiality of boring holes and meet the manufacturing needs of precision industrial parts.
General Technology Shenyang Machine Tool μ1000/5ST-500V five-axis linkage vertical machining center>
It is suitable for multi-faceted processing of complex box parts in key national fields. In addition to ordinary structural steel, the processing materials also include titanium alloys, high-temperature alloys, etc. Boring, drilling, reaming, tapping and rough and fine milling can be completed in one clamping, with high efficiency, high precision and high reliability. A single machine can produce various parts in small batches, or it can be connected to a production line to produce parts in batches according to user needs.
Beijing Jingdiao Jingdiao five-axis high-speed machining center>
Processing material: TC4; workpiece size: φ100×56.75 mm
The five-axis high-speed machining center's reasonable software and hardware configuration, stable machining accuracy, and the excellent tool-using ability of the machine tool itself ensure that the tool wear is small during the machining process of the titanium alloy compressor impeller. At the same time, it is combined with reasonable process measures such as swinging. Rough machining uses wire cutting, effectively utilizing side cutting CNC shop to prevent excessive wear of the tool. Finally, high-quality titanium alloy impellers can be processed efficiently!
2023 Exhibition Highlights>
2023《 ITES Shenzhen Industrial Exhibition 》> Its subsidiary Shenzhen International Metal Cutting Machine Tool Exhibition brings together global high-end intelligent equipment, innovative application technology solutions and cutting-edge industrial concepts, and is committed to machining/precision parts manufacturing, mold and accessories manufacturing, automobile/motorcycle complete sets for automobiles and parts, new Energy technology, 3C and electronic manufacturing, medical equipment, home appliances, kitchen and bathroom, metal products and other industries provide professional solutions for cost reduction and efficiency improvement, green manufacturing, and digital development.
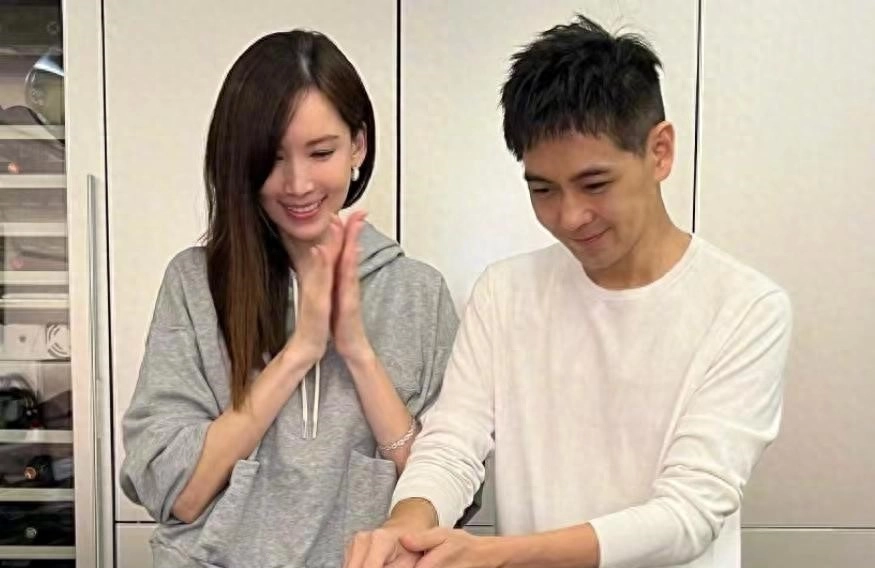