An In-depth Exploration of CNC Machine Co Search, Communicators, and Fuzzy Quality Inspection Standards in the Manufacturing Realm
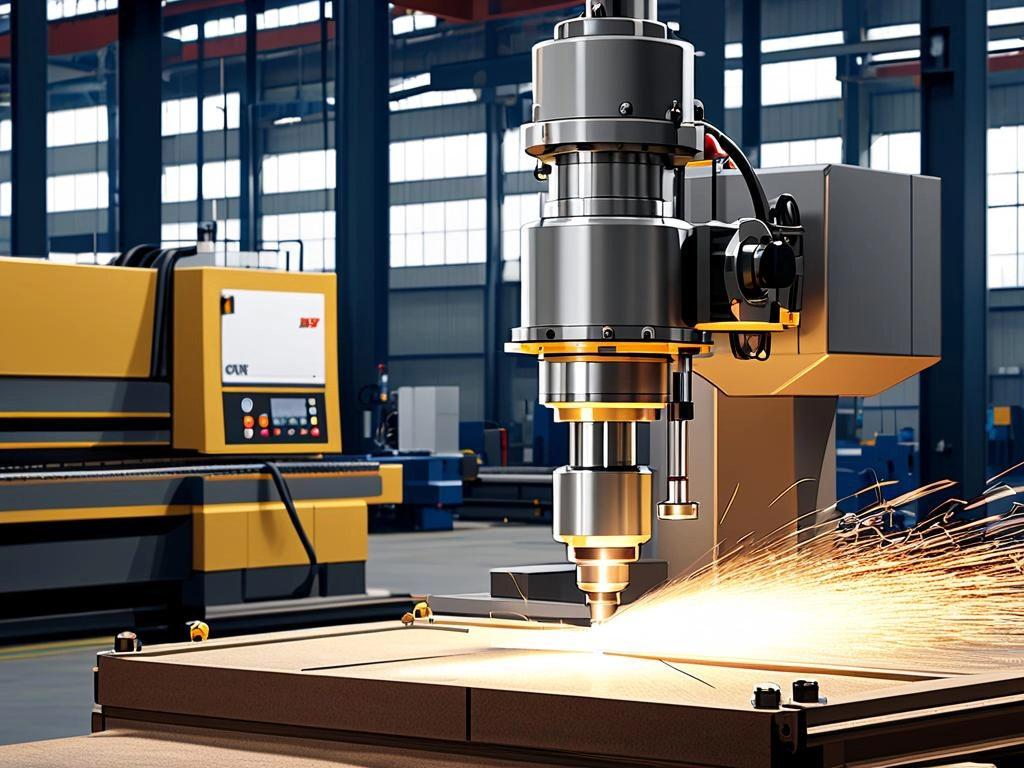
CNC Machine Co Search: The Key to Precision Manufacturing
The Significance of CNC Machine Co Search
CNC machine co search plays a crucial role in the manufacturing industry. It allows companies to find the most suitable CNC machines for their specific production needs. In a highly competitive market, having the right CNC machine can significantly enhance productivity and product quality. For example, a company that specializes in producing complex metal parts may require a CNC machine with high precision and multi-axis capabilities. Through effective co search, they can identify and invest in the appropriate machinery that meets their exact requirements.
How CNC Machine Co Search Works
The process of CNC machine co search involves several steps. Firstly, manufacturers need to clearly define their production goals and requirements. This includes factors such as the type of materials to be processed, the complexity of the parts, and the desired production volume. Based on these criteria, they can then search for CNC machines that offer the necessary features and capabilities. Online platforms and industry directories are often used to conduct such searches. Additionally, manufacturers may also consult with industry experts or visit trade shows to gather more information about available CNC machines.
Benefits of Optimized CNC Machine Co Search
An optimized CNC machine co search can bring numerous benefits to manufacturers. It can lead to increased production efficiency as the right machine can perform tasks more accurately and quickly. This, in turn, reduces production time and costs. Moreover, it can improve product quality by ensuring that the CNC machine is capable of producing parts with the required precision and surface finish. For instance, in the aerospace industry, where safety and reliability are of utmost importance, using a high-quality CNC machine obtained through effective co search can help produce components that meet the strict quality standards.
Communicators in the CNC Machine Environment
The Role of Communicators in CNC Operations
Communicators are essential in the CNC machine environment as they facilitate seamless communication between different components and personnel. In a CNC machine setup, communicators enable the transfer of data and instructions between the machine control unit, operators, and other connected systems. For example, operators can use communicators to send commands to the CNC machine, such as adjusting cutting parameters or starting a production run. At the same time, the machine can send feedback information, such as status updates and error messages, to the operators through the communicators.
Types of Communicators Used in CNC Machines
There are various types of communicators used in CNC machines. One common type is the human-machine interface (HMI), which provides a graphical user interface for operators to interact with the machine. The HMI allows operators to input commands, monitor the machine's performance, and make adjustments as needed. Another type is the network communicator, which enables the CNC machine to be connected to a local area network or the Internet. This allows for remote monitoring and control of the machine, as well as data sharing with other systems.
Importance of Effective Communication in CNC Machine Operations
Effective communication is vital in CNC machine operations. It ensures that the machine operates according to the intended instructions and that any issues or errors are promptly addressed. For example, if there is a communication breakdown between the operator and the CNC machine, it may lead to incorrect machining operations, resulting in defective parts. Therefore, it is essential to have reliable communicators and proper communication protocols in place to ensure smooth and efficient CNC machine operations.
Fuzzy Quality Inspection Standards: Ensuring Product Consistency
Understanding Fuzzy Quality Inspection Standards
Fuzzy quality inspection standards are a set of guidelines that take into account the inherent uncertainty and variability in manufacturing processes. Unlike traditional quality inspection standards that rely on precise numerical values, fuzzy standards allow for a more flexible and realistic assessment of product quality. For example, in some manufacturing processes, it may be difficult to define a specific tolerance limit for a certain dimension due to factors such as material variations and machining inaccuracies. Fuzzy quality inspection standards can handle such uncertainties by using linguistic variables and fuzzy logic.
Application of Fuzzy Quality Inspection Standards in CNC Machining
In CNC machining, fuzzy quality inspection standards can be applied to various aspects of the production process. For instance, they can be used to evaluate the surface finish of machined parts. Instead of specifying a single numerical value for the acceptable surface roughness, fuzzy standards can define a range of values with different degrees of membership. This allows for a more accurate assessment of the surface quality, taking into account the natural variations that occur during machining. Similarly, fuzzy standards can be used to evaluate the dimensional accuracy of parts, considering factors such as tool wear and thermal expansion.
Advantages of Fuzzy Quality Inspection Standards
The use of fuzzy quality inspection standards offers several advantages. Firstly, it provides a more realistic and practical approach to quality assessment, especially in complex manufacturing processes where precise numerical values may not be applicable. Secondly, it can help reduce the number of false rejects or false accepts, as it takes into account the inherent variability in the production process. This can lead to cost savings by minimizing unnecessary rework or scrap. Finally, fuzzy quality inspection standards can improve customer satisfaction by ensuring that products meet the expected quality levels more consistently.
Integration and Synergy
Integrating CNC Machine Co Search, Communicators, and Fuzzy Quality Inspection Standards
The integration of CNC machine co search, communicators, and fuzzy quality inspection standards can lead to significant improvements in the overall manufacturing process. By finding the most suitable CNC machine through effective co search, manufacturers can ensure that the machine has the necessary capabilities to meet the quality requirements defined by the fuzzy inspection standards. Communicators play a crucial role in this integration by enabling the seamless transfer of data and instructions between the machine, operators, and quality inspection systems. For example, the machine can send real-time data about the machining process to the quality inspection system, which can then use fuzzy logic to evaluate the quality of the parts being produced.
The Synergistic Effects of the Three Elements
The synergy between CNC machine co search, communicators, and fuzzy quality inspection standards can result in enhanced productivity, improved product quality, and reduced costs. When these elements work together effectively, manufacturers can optimize the production process, minimize errors and defects, and achieve higher levels of customer satisfaction. For instance, by using communicators to monitor and control the CNC machine in real-time based on the fuzzy quality inspection results, operators can make timely adjustments to ensure that the parts being produced meet the required quality standards. This can lead to a reduction in scrap and rework, thereby increasing production efficiency and reducing costs.
Conclusion and Future Outlook
Summary of Key Findings
In conclusion, CNC machine co search, communicators, and fuzzy quality inspection standards are all critical elements in modern manufacturing. CNC machine co search helps manufacturers find the right machines for their production needs, communicators enable effective communication and control in the CNC machine environment, and fuzzy quality inspection standards provide a more realistic and flexible approach to quality assessment. The integration and synergy of these elements can lead to significant improvements in productivity, product quality, and cost-effectiveness.
Future Trends and Developments
Looking ahead, we can expect to see further advancements in these areas. For example, the use of artificial intelligence and machine learning algorithms may enhance the effectiveness of CNC machine co search by providing more accurate recommendations based on historical data and production requirements. Communicators may become more sophisticated, enabling seamless integration with other smart manufacturing systems and the Internet of Things. Fuzzy quality inspection standards may also evolve to incorporate more advanced mathematical models and techniques, further improving the accuracy and reliability of quality assessment. Overall, the future of manufacturing looks promising with the continued development and integration of these key technologies.