Exploring the Excellence of the best CNC machine center with a Focus on Power supply panels and Finite element simulation optimization
Introduction to the best CNC machine center
The best CNC machine center represents the pinnacle of precision manufacturing technology. It is a sophisticated piece of equipment that combines advanced mechanical, electrical, and software systems to perform a wide range of machining operations with unparalleled accuracy and efficiency. These machine centers are widely used in various industries, including automotive, aerospace, electronics, and medical device manufacturing.
Key Features of the best CNC machine center
One of the primary features of the best CNC machine center is its high precision. It can achieve extremely tight tolerances, ensuring that the machined parts meet the most demanding quality standards. The machine's rigid structure and advanced servo control systems contribute to its excellent accuracy and repeatability. Additionally, the best CNC machine centers often come equipped with state-of-the-art tooling systems that allow for rapid tool changes and a wide variety of machining operations, such as milling, drilling, and tapping.
Applications in Different Industries
In the automotive industry, the best CNC machine center is used to manufacture engine components, transmission parts, and body panels with high precision. In the aerospace sector, it plays a crucial role in producing complex aircraft parts, such as turbine blades and structural components, where safety and reliability are of utmost importance. The electronics industry also relies on CNC machine centers for the production of precision components like circuit boards and microchips.
The Significance of Power supply panels
Power supply panels are an integral part of the best CNC machine center. They are responsible for providing the necessary electrical power to drive the machine's various components, including the motors, spindles, and control systems. A reliable and stable power supply is essential for the proper functioning of the machine and the quality of the machined parts.
Ensuring Stable Power Output
The power supply panels in the best CNC machine center are designed to provide a stable and consistent power output. They are equipped with advanced voltage regulation and filtering circuits to minimize power fluctuations and electrical noise. This ensures that the machine's motors and spindles operate at a constant speed, resulting in smooth and accurate machining operations.
Enhancing Safety and Protection
Power supply panels also incorporate various safety features to protect the machine and its operators. These include overcurrent protection, short-circuit protection, and ground fault protection. In the event of an electrical fault, these safety mechanisms will automatically shut down the power supply to prevent damage to the machine and potential harm to the operators.
Energy Efficiency Considerations
With the increasing focus on energy conservation, the power supply panels of the best CNC machine centers are designed to be energy-efficient. They employ advanced power management techniques, such as variable frequency drives and power factor correction, to reduce energy consumption and operating costs.
The Role of Finite element simulation optimization
Finite element simulation optimization is a powerful tool used in the design and development of the best CNC machine center. It allows engineers to analyze and optimize the machine's structural and thermal performance before physical prototyping, saving time and cost.
Structural Analysis and Optimization
By using finite element simulation, engineers can analyze the stress and deformation of the machine's components under different loading conditions. This helps them identify potential weak points and optimize the design to improve the machine's structural integrity and rigidity. For example, they can adjust the thickness and shape of the machine's frame to reduce vibrations and improve machining accuracy.
Thermal Analysis and Management
Finite element simulation can also be used to analyze the heat generation and dissipation in the machine center. This is particularly important for high-speed machining applications, where excessive heat can lead to thermal deformation and affect the machining accuracy. By optimizing the machine's cooling system and heat dissipation channels, engineers can ensure that the machine operates within a stable temperature range.
Performance Prediction and Improvement
Finite element simulation optimization enables engineers to predict the performance of the CNC machine center under different operating conditions. They can evaluate factors such as cutting forces, spindle speeds, and feed rates to optimize the machining process and improve the overall productivity and quality of the machined parts.
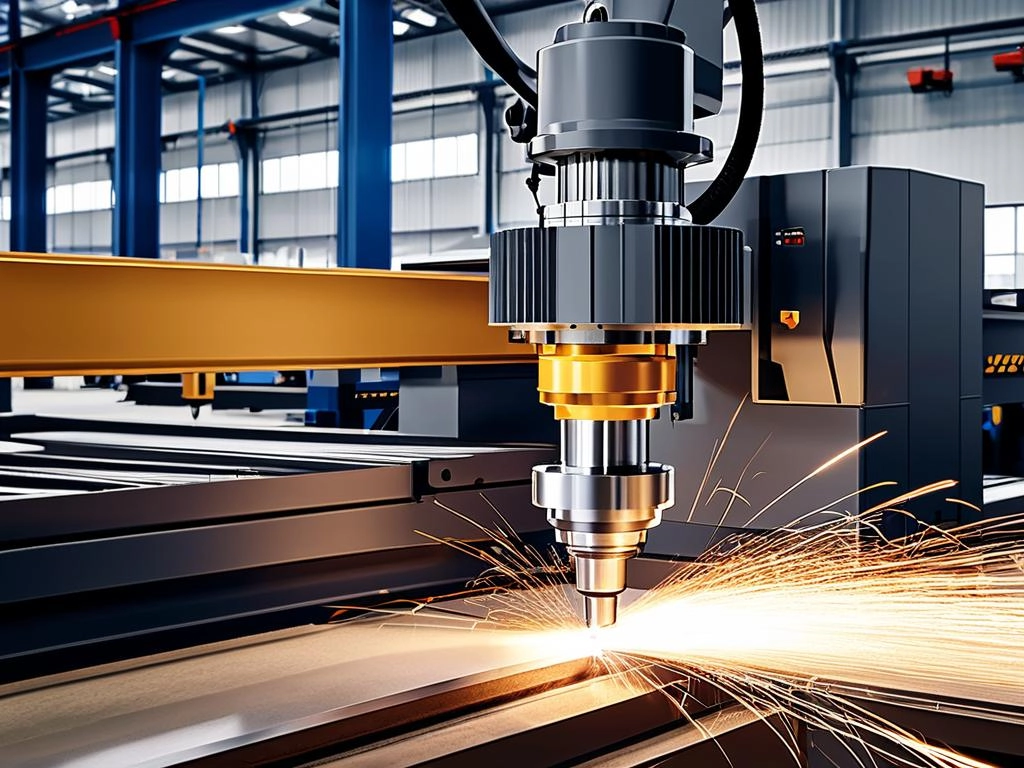
Synergy between the Elements
The best CNC machine center, power supply panels, and finite element simulation optimization work together in synergy to deliver outstanding performance. The reliable power supply from the panels ensures the smooth operation of the machine, while the optimization achieved through finite element simulation enhances its precision and efficiency.
Improved Machining Quality
The combination of a stable power supply and optimized machine design results in improved machining quality. The reduced vibrations and thermal deformation lead to more accurate and consistent part dimensions, better surface finishes, and fewer defects.
Increased Productivity
Finite element simulation optimization allows for faster and more efficient machining processes. By predicting and optimizing the machine's performance, engineers can increase the cutting speeds and feed rates while maintaining high quality, thereby reducing the production time and increasing productivity.
Cost Savings
The use of finite element simulation optimization reduces the need for physical prototyping and trial-and-error testing, saving both time and cost. Additionally, the energy-efficient power supply panels help lower the operating costs of the machine center over its lifetime.
Conclusion and Future Outlook
In conclusion, the best CNC machine center, with its advanced features and capabilities, is a key enabler for high-precision manufacturing. The power supply panels and finite element simulation optimization play crucial roles in ensuring its reliable operation, high performance, and cost-effectiveness. As technology continues to advance, we can expect further improvements in these areas, leading to even more sophisticated and efficient CNC machine centers. Manufacturers will continue to invest in research and development to meet the ever-increasing demands of various industries for higher quality, more complex, and cost-effective machined parts.