Unveiling the Precision World of CNC PEEK Machining for Diffusion Impellers: The Significance of Fine Calibration of CNC System Parameters in Technological Advancements
Introduction to CNC PEEK Machining
The Basics of CNC Machining
CNC machining, short for Computer Numerical Control machining, is a revolutionary manufacturing process that has transformed the way we produce complex parts and components. It involves the use of computer programs to control the movement and operation of machine tools, such as mills, lathes, and routers. This precise control allows for the creation of highly accurate and intricate parts with minimal human error.
PEEK Material and Its Properties
PEEK, or Polyetheretherketone, is a high-performance thermoplastic polymer known for its exceptional mechanical, thermal, and chemical properties. It has excellent strength, stiffness, and resistance to wear, making it an ideal material for applications where reliability and durability are crucial. In the context of CNC machining, PEEK offers unique challenges and opportunities due to its hardness and heat resistance.
Applications of CNC PEEK Machining
CNC PEEK machining finds extensive applications in various industries, including aerospace, medical, automotive, and electronics. One of the key applications is in the production of diffusion impellers. These impellers play a vital role in fluid dynamics systems, where their precise design and manufacturing are essential for optimal performance.
The Significance of Diffusion Impellers
Function and Importance in Fluid Dynamics
Diffusion impellers are responsible for controlling the flow and distribution of fluids in a system. They are designed to convert kinetic energy into pressure energy, thereby increasing the efficiency of fluid transfer. In applications such as pumps, turbines, and compressors, the performance of diffusion impellers directly impacts the overall efficiency and effectiveness of the system.
Design Considerations for Diffusion Impellers
The design of diffusion impellers requires careful consideration of factors such as blade geometry, flow patterns, and material selection. CNC PEEK machining enables the production of impellers with complex geometries and tight tolerances, ensuring optimal fluid flow and minimal energy losses. The use of PEEK material further enhances the impeller's performance by providing excellent resistance to corrosion and wear.
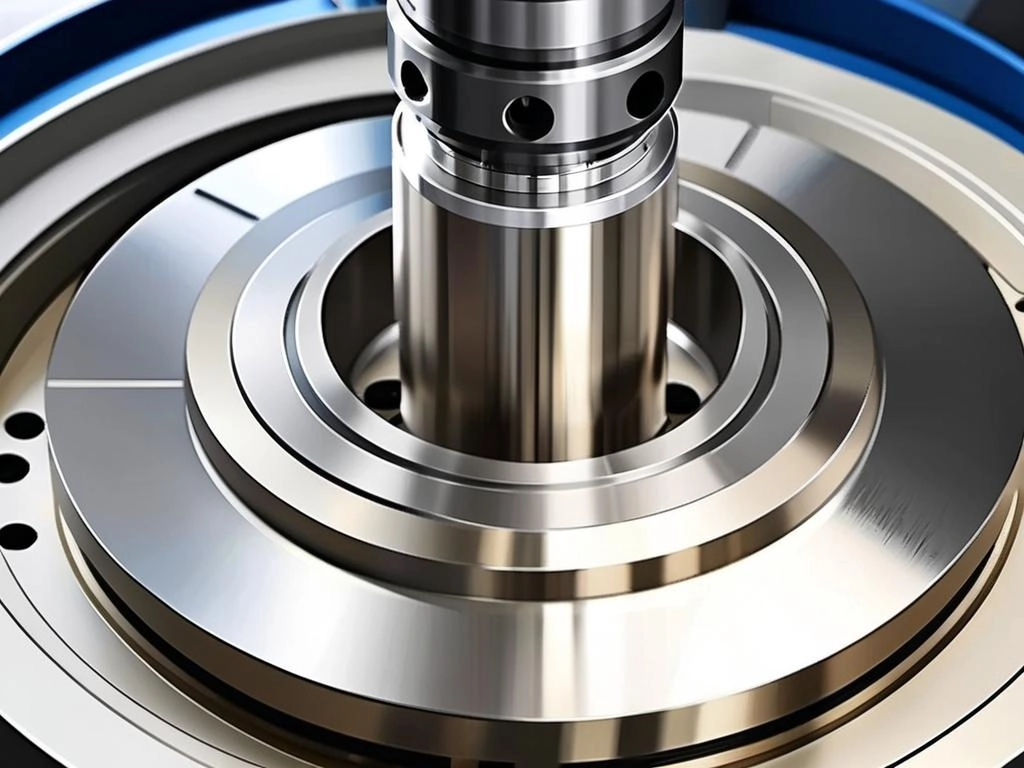
The Role of Fine Calibration of CNC System Parameters
Understanding CNC System Parameters
CNC system parameters are a set of values that determine the behavior and performance of the machining process. These parameters include cutting speed, feed rate, spindle speed, and tool path. Fine calibration of these parameters is essential to achieve the desired level of precision and quality in CNC PEEK machining.
Impact on Machining Precision
Proper calibration of CNC system parameters ensures that the cutting tools move accurately and smoothly, resulting in precise dimensions and surface finishes. In the case of CNC PEEK machining for diffusion impellers, even the slightest deviation in parameters can lead to significant differences in performance. For example, incorrect cutting speeds can cause excessive heat generation, leading to material deformation and reduced dimensional accuracy.
Optimizing Performance through Calibration
By fine-tuning the CNC system parameters, manufacturers can optimize the machining process for PEEK materials. This includes adjusting the cutting speed and feed rate to minimize tool wear and maximize material removal rates. Additionally, precise control of the spindle speed can ensure stable cutting conditions and improve surface quality.
Challenges and Solutions in CNC PEEK Machining
Material Hardness and Machinability
PEEK is a relatively hard material, which can pose challenges during machining. High cutting forces and temperatures can lead to tool wear and reduced tool life. To overcome these challenges, manufacturers can use specialized cutting tools and coolants. Additionally, optimizing the CNC system parameters can help reduce the cutting forces and temperatures, improving machinability.
Heat Management during Machining
The heat generated during CNC PEEK machining can cause thermal expansion and deformation of the material. This can affect the dimensional accuracy of the machined parts. To address this issue, effective heat management strategies such as coolant application and proper tool path planning are essential. These measures help dissipate the heat and maintain a stable machining environment.
Conclusion and Future Perspectives
Summary of Key Points
In conclusion, CNC PEEK machining for diffusion impellers is a complex and precise process that requires a deep understanding of the material properties, machining techniques, and CNC system parameters. The fine calibration of these parameters is crucial for achieving high-quality, accurate, and reliable impellers. By addressing the challenges associated with PEEK machining and optimizing the process, manufacturers can unlock the full potential of this advanced manufacturing technology.
Future Trends and Developments
Looking ahead, we can expect further advancements in CNC PEEK machining technology. This may include the development of more advanced cutting tools and machining strategies, as well as the integration of artificial intelligence and machine learning for real-time parameter optimization. These developments will enable even greater precision and efficiency in the production of diffusion impellers and other complex components.