An In-depth Inquiry into CNC Miling Shops Regarding Pinion Gear Production and the Impact of Unstable Air Pressure
Introduction to CNC Miling Shops Inquiry
CNC milling shops play a crucial role in modern manufacturing. These facilities are equipped with advanced computer numerical control machines that can precisely shape and fabricate various components with high accuracy. When it comes to the production of pinion gears, CNC milling shops are often the go-to choice for many industries. The inquiry into CNC milling shops regarding pinion gear production involves a comprehensive examination of their capabilities, processes, and quality control measures. This inquiry is essential as pinion gears are vital components in many mechanical systems, and their precision and quality can significantly impact the overall performance of the machinery.
Capabilities of CNC Miling Shops for Pinion Gear Production
CNC milling shops have the ability to produce pinion gears with a high degree of precision. The advanced CNC machines can accurately cut and shape the gear teeth according to the specified design parameters. These shops can handle a wide range of materials, including metals like steel, aluminum, and brass, as well as various alloys. The versatility of CNC milling machines allows for the production of pinion gears in different sizes and configurations to meet the diverse needs of different industries. For example, in the automotive industry, small and precise pinion gears are required for the smooth operation of transmissions, while in heavy machinery, larger and more robust pinion gears are needed.
Quality Control Measures in CNC Miling Shops
Quality control is of utmost importance in CNC milling shops when producing pinion gears. To ensure the highest quality, these shops employ various inspection and testing methods. One common method is the use of coordinate measuring machines (CMMs) to accurately measure the dimensions of the gear teeth and other critical features. This helps to detect any deviations from the design specifications and allows for timely adjustments. Additionally, hardness testing is often performed to ensure that the material used for the pinion gears has the appropriate strength and durability. Visual inspections are also carried out to check for any surface defects or irregularities.
The Significance of Pinion Gears
Pinion gears are essential components in many mechanical systems. They are used to transmit power and motion between different parts of a machine. In gearboxes, for instance, pinion gears work in conjunction with larger gears to achieve the desired speed and torque conversion. The precision and quality of pinion gears directly affect the efficiency and performance of the entire system. If the pinion gears are not accurately machined or have quality issues, it can lead to problems such as increased noise, vibration, and premature wear of the gears and other components.
Applications of Pinion Gears
Pinion gears find applications in a wide range of industries. In the automotive sector, they are used in transmissions, differentials, and steering systems. In the aerospace industry, pinion gears are crucial for the operation of flight control systems and engine components. Industrial machinery, such as conveyors, printing presses, and robotic arms, also rely on pinion gears for their smooth and efficient operation. The demand for high-quality pinion gears is constantly increasing as industries strive for greater precision and reliability in their machinery.
Design Considerations for Pinion Gears
When designing pinion gears, several factors need to be taken into account. The number of teeth, the pitch diameter, the pressure angle, and the tooth profile are all important design parameters. These parameters determine the gear's performance characteristics, such as its load-carrying capacity, efficiency, and smoothness of operation. The choice of material is also crucial, as it affects the gear's strength, durability, and resistance to wear and corrosion. Designers must carefully consider these factors to ensure that the pinion gears meet the specific requirements of the application.
The Impact of Unstable Air Pressure
Unstable air pressure can have a significant impact on the production of pinion gears in CNC milling shops. Air pressure is used in various processes within the shop, such as pneumatic clamping systems and coolant delivery systems. If the air pressure is unstable, it can lead to inconsistent clamping forces, which may result in inaccurate positioning of the workpiece during milling. This can cause errors in the dimensions and shape of the pinion gears. Additionally, unstable air pressure can affect the coolant delivery, leading to improper cooling of the cutting tools and the workpiece. This can result in increased tool wear and reduced surface finish quality of the gears.
Causes of Unstable Air Pressure
There are several factors that can cause unstable air pressure in CNC milling shops. One common cause is problems with the air compressor. If the air compressor is not properly maintained or has malfunctioning components, it may not be able to provide a consistent supply of compressed air. Another factor could be leaks in the air piping system. Leaks can cause a drop in air pressure and lead to instability. Additionally, fluctuations in the electrical power supply can also affect the operation of the air compressor and result in unstable air pressure.
Solutions to Address Unstable Air Pressure
To address the issue of unstable air pressure, CNC milling shops can take several measures. Regular maintenance of the air compressor is essential to ensure its proper functioning. This includes checking and replacing filters, lubricating moving parts, and inspecting for any signs of wear or damage. The air piping system should also be regularly inspected for leaks and repaired promptly. Installing pressure regulators and air storage tanks can help to stabilize the air pressure and provide a more consistent supply of compressed air. Additionally, having a backup power source or a voltage stabilizer can help to mitigate the effects of power fluctuations on the air compressor.
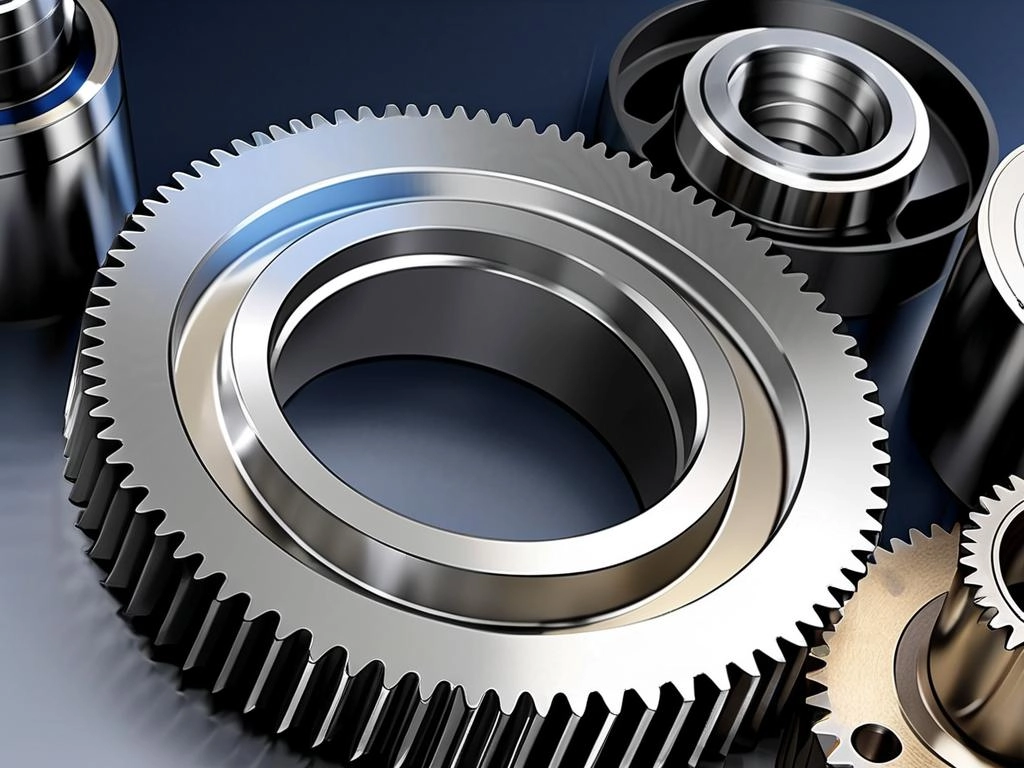
Conclusion and Recommendations
In conclusion, the inquiry into CNC milling shops regarding pinion gear production and the impact of unstable air pressure reveals the importance of precision, quality control, and stable operating conditions in manufacturing high-quality pinion gears. CNC milling shops need to continuously invest in advanced technology and training to improve their capabilities and ensure the production of reliable pinion gears. To address the issue of unstable air pressure, proactive maintenance and the implementation of appropriate solutions are crucial. Industries that rely on pinion gears should also work closely with CNC milling shops to ensure that the gears meet their specific requirements. Recommendations include regular communication between the shops and their customers, continuous improvement of manufacturing processes, and the adoption of best practices in quality control and air pressure management.