CNC Prototyping Center Inquiry: Resolving Production Scheduling Conflicts in Connecting Rod Manufacturing
Introduction to CNC Prototyping Center Inquiry
In the realm of modern manufacturing, the CNC prototyping center plays a crucial role. It serves as a hub for innovation and precision, allowing companies to bring their ideas to life with high accuracy and efficiency. When it comes to inquiries related to the CNC prototyping center, it often involves various aspects such as capabilities, processes, and cost. One common area of concern is the production of complex components like the connecting rod.
Understanding the Significance of CNC Prototyping
CNC prototyping offers numerous advantages. It enables manufacturers to quickly create prototypes, reducing the time and cost associated with traditional manufacturing methods. With its computer-controlled precision, it can produce highly accurate and detailed parts, ensuring a perfect fit and functionality. In the case of connecting rods, which are critical components in engines and machinery, CNC prototyping can ensure the highest quality and performance.
The Inquiry Process for CNC Prototyping Centers
When making an inquiry to a CNC prototyping center, it's essential to provide detailed information. This includes specifications of the connecting rod, such as dimensions, material requirements, and any specific design features. Additionally, understanding the center's capabilities, such as the types of CNC machines they have, their experience in handling similar projects, and their quality control measures, is vital.
Challenges of Connecting Rod Production
The production of connecting rods presents several challenges. These components need to withstand high levels of stress and strain, making their design and manufacturing a complex task. The materials used must have excellent strength and durability properties, and the manufacturing process must ensure precise dimensions and smooth surfaces.
Material Selection for Connecting Rods
Choosing the right material for connecting rods is crucial. Common materials include alloy steels, which offer a good balance of strength and toughness. However, the selection also depends on factors such as the application, operating conditions, and cost. For high-performance applications, more exotic materials may be required, but this also increases the production cost.
Precision Machining Requirements
CNC machining is the preferred method for producing connecting rods due to its high precision. The machining process must ensure accurate dimensions, tight tolerances, and smooth surfaces to minimize friction and wear. This requires advanced CNC machines and skilled operators who can program and operate them effectively.
Quality Control in Connecting Rod Production
Quality control is of utmost importance in connecting rod production. Various inspection techniques, such as dimensional measurement, surface roughness analysis, and material testing, are used to ensure that the parts meet the required specifications. Any defects or deviations can lead to performance issues and potential failures.
Production Scheduling Conflicts and Solutions
Production scheduling conflicts are a common issue in manufacturing, especially in CNC prototyping centers. These conflicts can arise due to various reasons, such as high demand, limited machine availability, and unexpected delays in the supply chain.
Causes of Production Scheduling Conflicts
One of the main causes of scheduling conflicts is the lack of proper planning. If orders are not properly scheduled and prioritized, it can lead to overloading of machines and delays in production. Additionally, changes in customer requirements or unexpected machine breakdowns can also disrupt the production schedule.
Impact of Scheduling Conflicts on Connecting Rod Production
Scheduling conflicts can have a significant impact on connecting rod production. Delays can lead to missed delivery deadlines, which can result in customer dissatisfaction and loss of business. Moreover, it can also affect the overall production efficiency and increase costs due to idle time and rush orders.
Strategies to Resolve Production Scheduling Conflicts
To resolve production scheduling conflicts, several strategies can be implemented. First, effective planning and forecasting are essential. By accurately predicting demand and scheduling orders in advance, manufacturers can avoid overloading machines and ensure a smooth production flow. Second, implementing a flexible production system that can quickly adapt to changes in demand and unforeseen circumstances can also help. This may involve having backup machines or cross-training operators.
The Role of Communication in Resolving Scheduling Conflicts
Communication is key in resolving production scheduling conflicts. All stakeholders, including customers, suppliers, and internal teams, need to be kept informed about any changes or delays. This allows for better coordination and cooperation, and can help find solutions to problems more quickly.
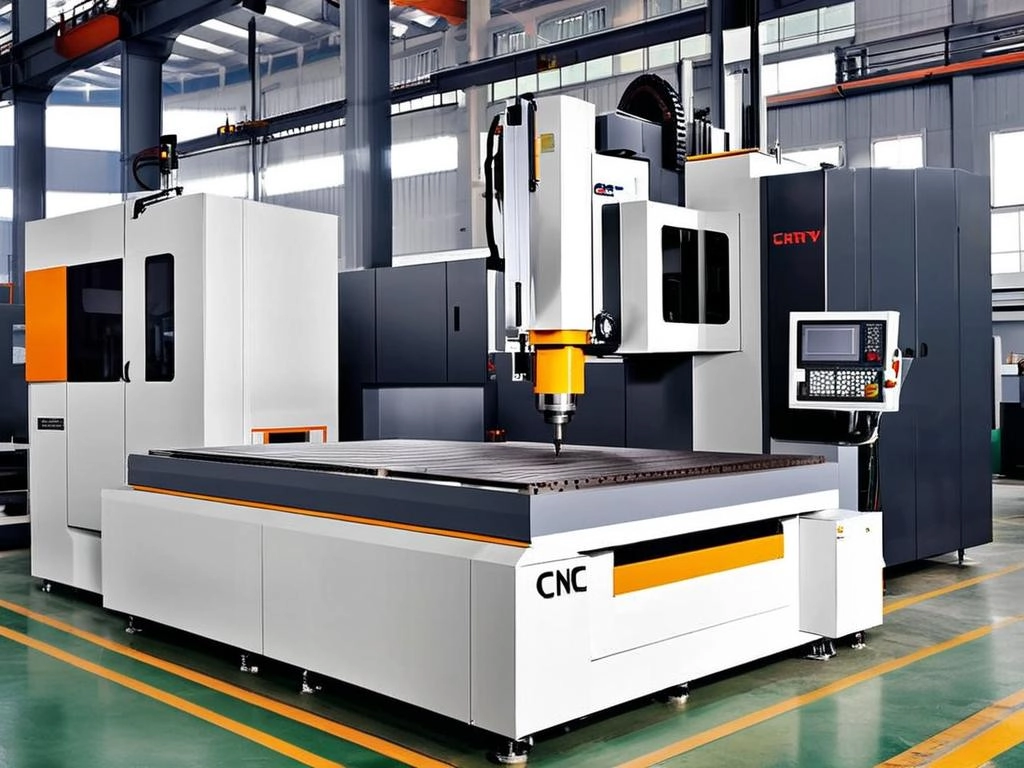
Conclusion
In conclusion, CNC prototyping center inquiries related to connecting rod production involve various aspects, from material selection and precision machining to quality control and production scheduling. By understanding these aspects and implementing appropriate strategies, manufacturers can overcome challenges and ensure the efficient production of high-quality connecting rods. Resolving production scheduling conflicts is crucial for maintaining customer satisfaction and competitiveness in the market. With careful planning, effective communication, and a focus on quality, CNC prototyping centers can meet the demands of the industry and contribute to the success of their clients.