The Significance and Implementation of "Semiconductor CNC Turning", "Resistor chip" and the Construction of Processing Process Data Acquisition and Analysis System
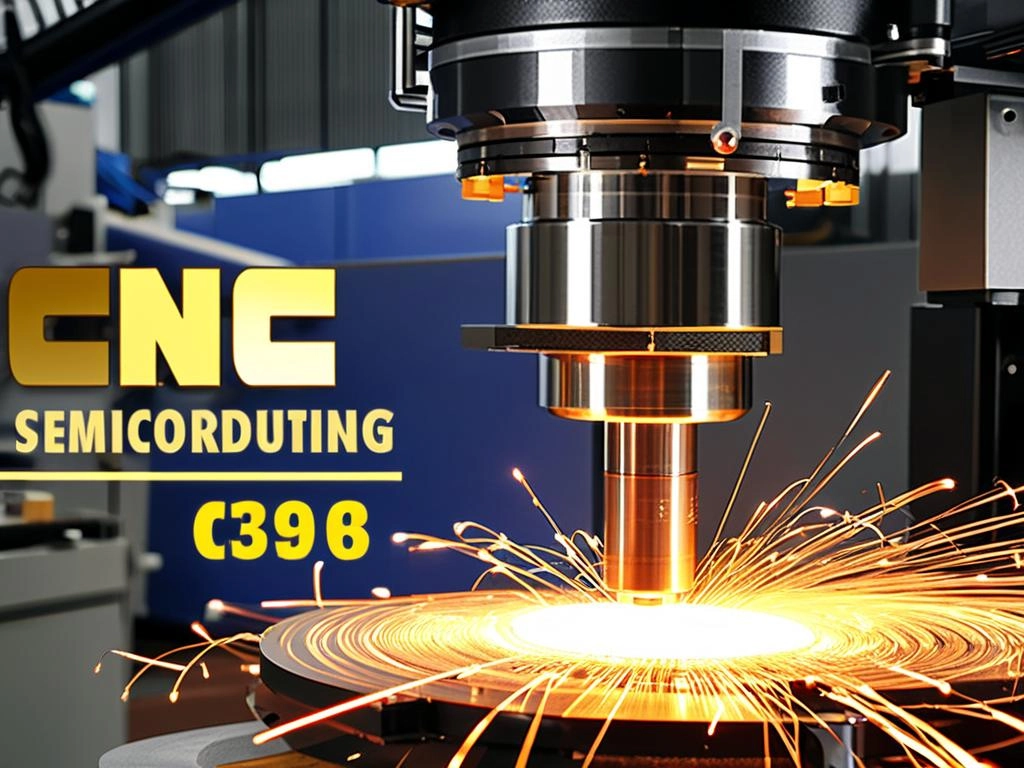
Introduction to Semiconductor CNC Turning
What is Semiconductor CNC Turning?
Semiconductor CNC Turning is a highly precise manufacturing process that plays a crucial role in the semiconductor industry. It involves the use of computer numerical control (CNC) technology to turn semiconductor materials into specific shapes and sizes with high accuracy. This process is essential for producing various semiconductor components, such as wafers and chips, which are the building blocks of modern electronics.
Advantages of Semiconductor CNC Turning
One of the main advantages of Semiconductor CNC Turning is its ability to achieve extremely high precision. The CNC machines can control the cutting tools with great accuracy, ensuring that the semiconductor materials are shaped precisely according to the design specifications. This precision is vital for the proper functioning of semiconductor devices, as even the slightest deviation can lead to performance issues. Additionally, CNC turning allows for high repeatability, meaning that the same high-quality parts can be produced consistently, which is crucial for mass production in the semiconductor industry.
Applications of Semiconductor CNC Turning
Semiconductor CNC Turning has a wide range of applications. It is used in the manufacturing of integrated circuits, where precise shaping of semiconductor wafers is required. It is also used in the production of optoelectronic devices, such as light-emitting diodes (LEDs) and photodetectors. The ability to accurately turn semiconductor materials enables the creation of complex structures that are necessary for the efficient operation of these devices.
Resistor chip: An Essential Component
Function of Resistor chip
Resistor chips are fundamental components in electronic circuits. Their primary function is to resist the flow of electric current, thereby controlling the amount of current that passes through a particular part of the circuit. By adjusting the resistance value, resistor chips can regulate voltage levels, limit current flow to protect other components from damage, and perform various signal conditioning tasks. For example, in a power supply circuit, resistor chips are used to divide voltages and ensure that the appropriate voltage is supplied to different parts of the circuit.
Types of Resistor chips
There are several types of resistor chips available, each with its own characteristics and applications. Some common types include carbon film resistors, metal film resistors, and thick film resistors. Carbon film resistors are widely used due to their low cost and good stability. Metal film resistors offer higher precision and lower temperature coefficients, making them suitable for applications where accuracy is crucial. Thick film resistors are often used in high-power applications as they can handle larger currents.
Manufacturing Process of Resistor chip
The manufacturing process of resistor chips involves several steps. First, the resistive material is deposited on a substrate. This can be done using various techniques such as sputtering or chemical vapor deposition. Then, the resistive material is patterned to define the resistor's shape and value. This is typically achieved through photolithography or other etching processes. Finally, the resistor chips are encapsulated to protect them from environmental factors and ensure their long-term reliability.
Construction of Processing Process Data Acquisition and Analysis System
Importance of Data Acquisition
In the context of Semiconductor CNC Turning and resistor chip manufacturing, data acquisition is of utmost importance. By collecting data during the processing process, manufacturers can gain valuable insights into the performance of the manufacturing equipment, the quality of the products being produced, and any potential issues that may arise. For example, data on cutting forces, spindle speeds, and tool wear can be monitored in real-time to optimize the machining parameters and ensure the highest quality of semiconductor components and resistor chips.
Components of the Data Acquisition System
A typical processing process data acquisition system consists of several components. Sensors are used to measure various physical quantities such as temperature, pressure, and vibration. These sensors are placed at strategic locations on the manufacturing equipment to capture relevant data. The data collected by the sensors is then transmitted to a data acquisition card, which converts the analog signals into digital signals that can be processed by a computer. The computer is equipped with specialized software that stores, analyzes, and visualizes the acquired data.
Data Analysis and Optimization
Once the data is acquired, it needs to be analyzed to extract meaningful information. Data analysis techniques such as statistical analysis, machine learning, and data mining can be used to identify patterns, trends, and correlations in the data. For example, by analyzing the data on tool wear, manufacturers can predict when a tool needs to be replaced, thereby reducing downtime and improving productivity. Based on the analysis results, the manufacturing process can be optimized by adjusting the machining parameters, improving the tooling, or implementing other process improvements.
Integration and Synergy
Integrating Semiconductor CNC Turning and Resistor chip Manufacturing
The integration of Semiconductor CNC Turning and resistor chip manufacturing processes can lead to significant benefits. For example, by using CNC turning techniques to precisely shape the substrates used in resistor chip manufacturing, the overall quality and performance of the resistor chips can be improved. Additionally, the data acquisition and analysis system can be used to monitor and optimize both the CNC turning and resistor chip manufacturing processes simultaneously, further enhancing the efficiency and quality of production.
Synergy between Data Acquisition and Manufacturing Processes
The synergy between the data acquisition and analysis system and the manufacturing processes is crucial for continuous improvement. The data collected during the processing process can be used to identify areas for improvement, and the insights gained from the data analysis can be used to implement targeted process changes. This iterative process of data collection, analysis, and improvement can lead to higher quality products, increased productivity, and reduced costs.
Conclusion
In conclusion, Semiconductor CNC Turning, resistor chips, and the construction of processing process data acquisition and analysis systems are all essential elements in the modern electronics manufacturing industry. The precision and repeatability offered by Semiconductor CNC Turning enable the production of high-quality semiconductor components, while resistor chips play a vital role in controlling electrical currents in electronic circuits. The data acquisition and analysis system provides valuable insights into the manufacturing process, allowing for continuous optimization and improvement. By integrating these elements and leveraging their synergies, manufacturers can achieve higher levels of efficiency, quality, and competitiveness in the global market.