Unveiling the World of CNC Miling Search, Compressors, and the Intricacies of Fine-tuning Parameters in CNC Systems
CNC Miling Search: An In-depth Exploration
Understanding the Basics of CNC Miling Search
CNC milling search plays a crucial role in the manufacturing industry. It involves the precise search and optimization of milling processes in Computer Numerical Control (CNC) machines. These machines are the backbone of modern manufacturing, enabling highly accurate and efficient production of complex parts. The search aspect focuses on finding the most optimal milling strategies, tool paths, and cutting parameters to achieve the desired results. For example, when manufacturing a complex aerospace component, the CNC milling search helps determine the best way to remove material with minimal waste and maximum precision.
Advanced Techniques in CNC Miling Search
Advanced techniques in CNC milling search include the use of simulation software. This software allows manufacturers to virtually test different milling scenarios before implementing them on the actual machine. By simulating the milling process, potential issues such as tool collisions, excessive material removal, or inaccuracies can be identified and corrected. Another important aspect is the integration of artificial intelligence and machine learning algorithms. These technologies can analyze large amounts of data from previous milling operations and suggest improvements for future processes. For instance, they can predict the optimal cutting speed and feed rate based on the material being milled and the desired surface finish.
Applications of CNC Miling Search
CNC milling search finds applications in various industries. In the automotive industry, it is used to manufacture engine components with high precision. The search algorithms help optimize the milling process to ensure that the parts meet the strict quality standards required for automotive applications. In the medical field, CNC milling search is crucial for producing custom implants and surgical instruments. The ability to fine-tune the milling parameters ensures that these medical devices are of the highest quality and compatibility with the human body.
Compressors: The Heart of Many Industrial Processes
Types of Compressors
There are several types of compressors, each with its unique characteristics and applications. Reciprocating compressors are commonly used in small to medium-scale applications. They work by using a piston-cylinder arrangement to compress the gas. Rotary screw compressors, on the other hand, are more suitable for continuous operation and higher flow rates. They operate by trapping and compressing the gas between two rotating screws. Centrifugal compressors are ideal for large-scale industrial applications where high flow rates and relatively low pressure ratios are required. They use the principle of centrifugal force to compress the gas.
Working Principles of Compressors
The working principle of a compressor involves reducing the volume of a gas to increase its pressure. In a reciprocating compressor, the piston moves back and forth within the cylinder, creating a pressure difference that draws in the gas and then compresses it. Rotary screw compressors use the rotation of the screws to continuously compress the gas as it moves through the compressor. Centrifugal compressors accelerate the gas using a rotating impeller and then convert the kinetic energy into pressure energy as the gas slows down in a diffuser.
Applications of Compressors
Compressors have a wide range of applications. In the refrigeration and air conditioning industry, compressors are used to circulate and compress the refrigerant, enabling the transfer of heat. In the oil and gas industry, they are used for gas transportation and processing. Compressors are also essential in pneumatic systems, where they provide the necessary compressed air for various tools and equipment, such as drills, paint sprayers, and pneumatic actuators.
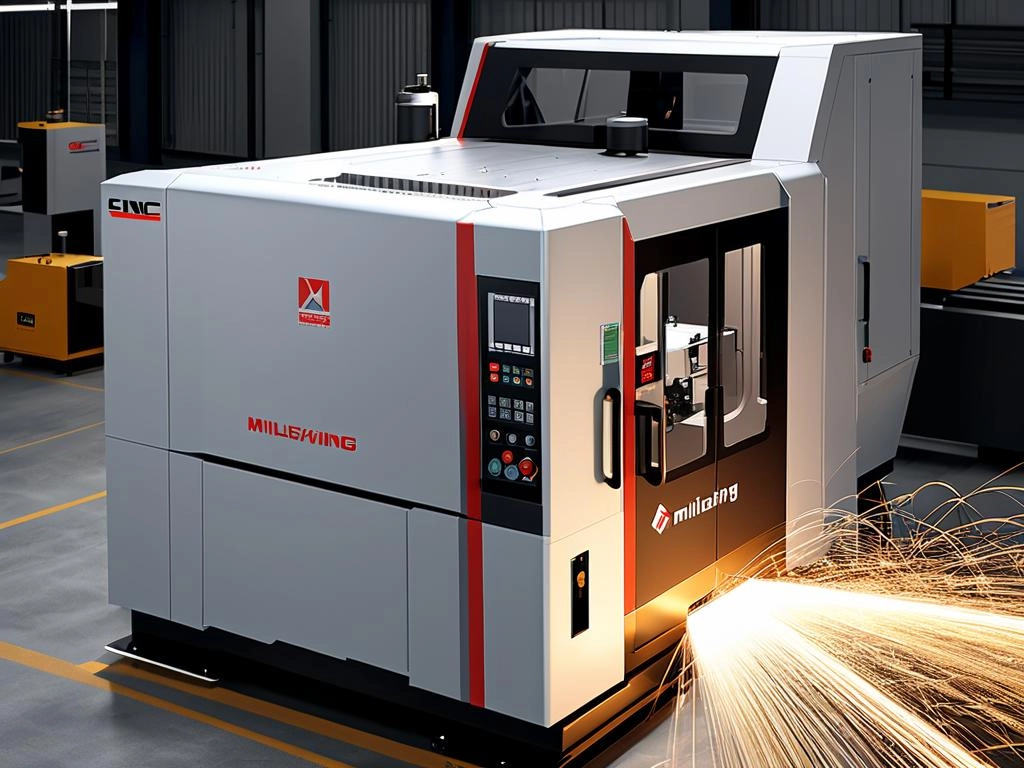
Fine-tuning Parameters in CNC Systems: A Delicate Art
The Importance of Parameter Fine-tuning
Fine-tuning the parameters in CNC systems is of utmost importance to achieve the desired machining accuracy and surface finish. Parameters such as cutting speed, feed rate, and depth of cut directly affect the quality of the machined part. Incorrect parameter settings can lead to issues such as tool wear, poor surface finish, and dimensional inaccuracies. For example, if the cutting speed is too high, it can cause excessive heat generation, leading to tool damage and a degraded surface finish.
Key Parameters to Consider
Some of the key parameters to consider when fine-tuning a CNC system include the cutting speed, which determines how fast the tool moves relative to the workpiece. The feed rate, which controls the rate at which the tool advances into the material, also plays a significant role. The depth of cut, which specifies how much material is removed in each pass, needs to be carefully adjusted to balance the machining efficiency and quality. Additionally, parameters such as spindle speed and coolant flow rate also need to be optimized for different materials and machining operations.
Techniques for Parameter Fine-tuning
There are several techniques for fine-tuning the parameters in CNC systems. One approach is to conduct trial cuts and measure the results. By gradually adjusting the parameters and observing the changes in the machined part, the optimal settings can be determined. Another technique is to use mathematical models and simulation software to predict the effects of different parameter settings. This allows for more efficient and accurate fine-tuning without the need for extensive trial and error.
In conclusion, CNC milling search, compressors, and the fine-tuning of parameters in CNC systems are all integral parts of modern manufacturing. Understanding and optimizing these aspects can lead to improved productivity, higher quality products, and a competitive edge in the global market.