Unlocking the Potential: The Role of CNC Simulation and the Improvement of CNC Tool Coating Technology in Closet Rod Production
Understanding CNC Simulation
The Concept of CNC Simulation
CNC simulation is a powerful tool that allows manufacturers to virtually model and test the entire machining process before any physical cutting takes place. It provides a detailed preview of how the CNC machine will operate, including the movement of the tool, the interaction with the workpiece, and the resulting final product. In the context of closet rod production, CNC simulation can be used to optimize the cutting paths, reduce material waste, and ensure the dimensional accuracy of the rods.
Benefits of CNC Simulation in Closet Rod Manufacturing
One of the key benefits of CNC simulation is the ability to detect and correct errors early in the design and production process. By simulating the machining operations, manufacturers can identify potential collisions between the tool and the workpiece, incorrect tool paths, or other issues that could lead to defective parts. This not only saves time and materials but also improves the overall quality of the closet rods. Additionally, CNC simulation allows for rapid prototyping and design iterations, enabling manufacturers to quickly test different design concepts and make adjustments as needed.
Real-World Applications of CNC Simulation
In the closet rod industry, CNC simulation has been widely adopted by leading manufacturers. For example, a company may use CNC simulation to optimize the cutting process for different types of closet rod materials, such as wood, metal, or plastic. By accurately simulating the cutting forces and tool wear, they can select the most appropriate cutting parameters and tool coatings to achieve the best results. This not only improves the efficiency of the production process but also extends the tool life, reducing the need for frequent tool changes.
The Significance of Closet Rod Production
The Role of Closet Rods in Interior Design
Closet rods are an essential component of any closet system, providing a convenient and organized way to hang clothes and accessories. They come in a variety of styles, materials, and finishes, allowing homeowners and designers to customize their closets according to their specific needs and aesthetic preferences. In addition to their functional role, closet rods can also enhance the overall look and feel of a room, adding a touch of elegance and sophistication.
Market Demand for High-Quality Closet Rods
With the growing demand for custom-built closets and organized storage solutions, the market for high-quality closet rods is on the rise. Consumers are increasingly looking for closet rods that are not only durable and functional but also aesthetically pleasing. This has led manufacturers to focus on improving the quality and design of their products, using advanced manufacturing technologies such as CNC machining and innovative materials to meet the evolving needs of the market.
Challenges in Closet Rod Production
Despite the advancements in manufacturing technology, closet rod production still faces several challenges. One of the main challenges is ensuring the dimensional accuracy and surface finish of the rods, especially when working with complex designs or tight tolerances. Another challenge is the need to balance production efficiency with quality control, as any defects or errors in the manufacturing process can lead to costly rework or customer dissatisfaction.
Improvement of CNC Tool Coating Technology
Overview of CNC Tool Coating Technology
CNC tool coating technology involves the application of a thin layer of material onto the surface of the cutting tool to improve its performance and durability. These coatings can provide a range of benefits, such as reducing friction, increasing wear resistance, and improving heat dissipation. In the context of closet rod production, advanced tool coatings can help to achieve better surface finishes, extend tool life, and improve the overall efficiency of the machining process.
Latest Developments in CNC Tool Coating Technology
Recent years have seen significant advancements in CNC tool coating technology. New coating materials and application methods have been developed to meet the increasingly demanding requirements of modern manufacturing. For example, some of the latest coatings are designed to provide enhanced protection against high temperatures and abrasive materials, making them ideal for machining hard-to-cut alloys and composites used in high-end closet rod production. Additionally, nanotechnology has been applied to develop ultra-thin and highly uniform coatings that offer superior performance and precision.
Impact of Improved Tool Coatings on Closet Rod Production
The improvement of CNC tool coating technology has had a profound impact on closet rod production. By using advanced coatings, manufacturers can achieve higher cutting speeds and feeds, reducing the machining time and increasing productivity. At the same time, the improved wear resistance of the coated tools means that they can maintain their sharpness and performance for longer periods, resulting in fewer tool changes and lower production costs. Moreover, the better surface finishes achieved with coated tools can enhance the aesthetic appeal of the closet rods, meeting the high standards of quality and design expected by consumers.
Synergy between CNC Simulation and Tool Coating Technology
Optimizing the Machining Process
The combination of CNC simulation and improved tool coating technology can further optimize the machining process for closet rod production. By using simulation software to analyze the cutting forces and heat generation during machining, manufacturers can select the most appropriate tool coatings and cutting parameters to achieve the best results. This synergy allows for more precise control over the machining process, resulting in higher quality closet rods with improved dimensional accuracy and surface finish.
Enhancing Productivity and Cost-Effectiveness
When CNC simulation and tool coating technology are used together, manufacturers can significantly enhance their productivity and cost-effectiveness. The ability to accurately predict and optimize the machining process through simulation reduces the need for trial and error, saving time and materials. At the same time, the extended tool life provided by advanced coatings reduces the frequency of tool changes, further increasing production efficiency and reducing operating costs.
Meeting the Demands of a Competitive Market
In today's highly competitive market, manufacturers of closet rods need to constantly innovate and improve their production processes to stay ahead of the competition. The integration of CNC simulation and tool coating technology provides them with a powerful combination of tools to achieve this goal. By producing high-quality closet rods with improved performance and aesthetics, manufacturers can attract more customers and gain a competitive edge in the market.
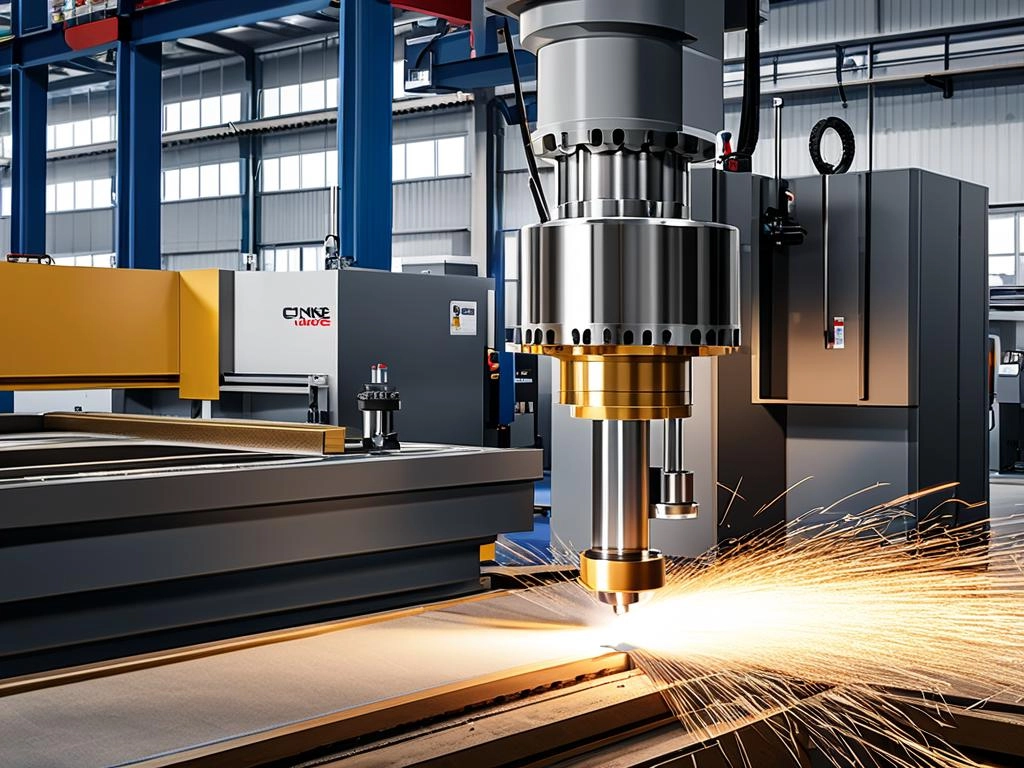
Conclusion and Future Outlook
Summary of Key Findings
In conclusion, CNC simulation and the improvement of CNC tool coating technology play crucial roles in the production of high-quality closet rods. CNC simulation allows manufacturers to optimize the machining process, detect and correct errors early, and improve the overall efficiency and quality of production. The advancement of tool coating technology, on the other hand, enhances the performance and durability of cutting tools, leading to better surface finishes, extended tool life, and reduced production costs. The synergy between these two technologies further amplifies their benefits, enabling manufacturers to meet the demands of a competitive market.
Future Trends and Opportunities
Looking ahead, we can expect to see continued advancements in both CNC simulation and tool coating technology. As manufacturing processes become more complex and demanding, the need for more accurate and sophisticated simulation software will increase. Similarly, research and development in tool coating materials and application methods will continue to drive improvements in tool performance and durability. These advancements will not only benefit the closet rod industry but also have a broader impact on the manufacturing sector as a whole.
Call to Action for Manufacturers
For manufacturers in the closet rod industry, it is essential to embrace these technologies and invest in the necessary training and equipment to stay competitive. By leveraging the power of CNC simulation and improved tool coating technology, they can enhance their production capabilities, improve product quality, and meet the evolving needs of their customers. This will not only lead to increased profitability but also contribute to the long-term success and sustainability of their businesses.