How Should We Solve The Difficulties Encountered In Stainless Steel Processing?
First of all, we need to understand the reasons why stainless steel materials are difficult to process:
1. High high temperature strength and high work hardening tendency
Compared with ordinary steel, the strength and hardness of stainless steel are not high, but because it contains a large amount of Cr, Ni, Mn and other elements, it has good plasticity and toughness, high high-temperature strength, and a large tendency to work harden, so it has a heavier cutting load. In addition, during the cutting process of austenitic stainless steel, some carbides will precipitate inside, which will increase the scratching effect on the tool.
2. High cutting force
Stainless steel undergoes large plastic deformation during the cutting process, especially austenitic stainless steel (its elongation is more than 1.5 times that of 45 steel), which increases the cutting force.
3. Severe combination of chips and tools
Built-up edges are easily generated during the cutting process, which not only affects the roughness of the machined surface, but also easily causes the tool surface to peel off.
4. Chips are not easy to curl or break.
For closed and semi-closed chip-containing tools, built-up edges are prone to occur, which increases the roughness of the machined surface and causes tool chipping.
5. Large linear expansion coefficient
The linear expansion coefficient is about one and a half times that of carbon steel. Under the influence of cutting temperature, the workpiece is prone to thermal deformation, affecting dimensional accuracy.
6. Small thermal conductivity
Generally, the thermal conductivity is about 1/4~1/2 of medium carbon steel. The cutting temperature is high and the tool wears quickly.
Based on the above difficulties in stainless steel processing, we can start from the following aspects:
1. Tool materials should be selected with high hardness, good toughness and heat resistance, and low chemical affinity with stainless steel;
2. When using high-speed steel, high-performance high-speed steels such as W2Mo9Cr4VCo8, W6Mo5Cr4V2Al, and W10Mo4Cr4V3Al should be used;
3. When using cemented carbide, YT alloy should not be used. It is best to use YW or YG tungsten cobalt alloys (ISO M and K categories) containing Ta (Nb). Such as YS2, YG3X, YG8W, YG6A, YG6X, YG643, YG813, YW3Y, YG8N, etc.;
4. Coated cemented carbide can be CA15, CA25, YBM151, YBM251, YBM351, YBG202, YBG252, YBG302, CN251, YB425, ZC05, ZC07, ZM10, etc.;
5. YNG151 can be used for cermets; YNG151C can be used for coated cermets;
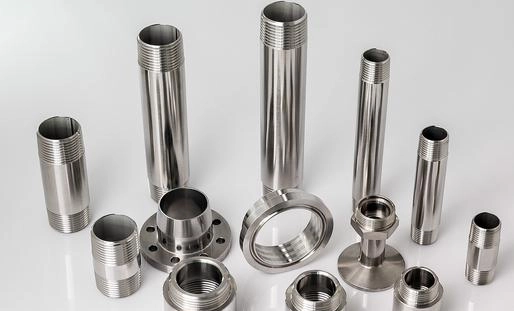