The Machining Center Is Clamped In This Way To Prevent The Aluminum Plate From Deforming During Processing.
It occurs frequently in thin plate parts processing. When processing thin plate parts using traditional processing techniques and existing processing equipment, it is easy to cause deformation of the parts. First, the types and causes of deformation of thin plate parts should be analyzed, and then solutions to the processing deformation of thin plate parts should be studied from the aspects of processing technology, processing technical conditions, processing tools, clamping methods, etc.
Today I will mainly discuss with you how to choose the appropriate clamping method to minimize deformation.
The aluminum clamping of the machining center should try to follow the following principles:
The selected datum should be able to ensure the accurate positioning of the workpiece and ensure various processing accuracy; the dimensions of the datum and each processed part are simple to calculate, and the calculation amount of the dimension chain is small; the workpiece is easy to load and unload, the clamping is reliable, and the fixture structure is simple;
Aluminum alloy plate parts processing
Common clamping methods when processing aluminum alloy sheet parts mainly include pressure plates , vise , vacuum suction cups (workbench) , glue (double-sided tape), frozen suction cups, etc. Let’s analyze them one by one first.
Pressure plates , vises, and toad pliers (the side tops can be either rough or flat) need to be clamped during processing, so sometimes they need to be clamped multiple times, which is troublesome.
Pressure plates and vise are the basic clamping methods for thin plate parts, relying on jaw clamping or surrounding pressure plates. The cutting force and thermal stress generated during the milling of thin plate parts will cause the workpiece to deform and thermally expand outward. However, due to the limitations of the jaws or the surrounding pressure plate, the workpiece cannot extend in this direction, so it can only be convex upward. (Vibration may also occur during processing), so the processing dimensions in the thickness direction of the workpiece are inconsistent, especially the center part will be cut off more.
Toad clamp can use side top clamping method for processing plates with insufficient rigidity. At this time, the workpiece is not restricted by external forces in the vertical direction, but is in a relatively free state. Processing in this state can fully release the processing stress, the deformation of the workpiece after processing is small (mainly affected by the cutting force, there is slight deformation in the vertical direction), and usually higher accuracy (flatness, parallelism) can be obtained .
Vacuum suction cups (desktop), glue (double-sided tape), and frozen suction cups are relatively easier to process thin sheet parts.
The vacuum suction cup method has certain requirements on the structure of the parts. There must be a place for adsorption, no air leakage, and the workpiece must be relatively rigid. Otherwise, machining can only ensure equal thickness on both major surfaces. In actual use, the parallel accuracy is often acceptable, but the flatness does not meet the requirements.
The glue coating method prevents the workpiece from being easily displaced in the vertical direction during processing, thereby achieving consistent processing thickness. Since the workpiece is not restricted by additional external forces, it can be in a relatively free state during deformation, allowing the processing stress to be fully released, so the deformation of the workpiece after processing is small. However, special attention should be paid to the fact that the cutting force and cutting amount must be very small during processing.
I personally have never come across the method of freezing suckers . It is said to enable stress-free processing. The specific processing effects will not be commented here.
How should we choose specifically?
The first condition: The Z axis and XY axis of the machine tool must have good verticality. Please make sure of this first.
Secondly: the clamping force should be as small as possible, the clamping force should be as small as possible, the clamping force should be as small as possible, and important things should be said three times.
On the premise that the plane consistency of the bottom surface (positioning surface) is high, first look at the processing requirements.
If you want to pursue quality, it requires very high output and small output.
Clamping devices with small clamping force should be used whenever possible. It can be bonded with AB glue or 502 glue. At the same time, it is necessary to use small diameter tools, small depth of cut, and high feed to reduce cutting forces. The process needs to be repeated for the front and back. .
If the requirements for processing efficiency are relatively high.
The above method may not be appropriate. It is still necessary to use multiple processes and pneumatic clamps with small clamping force. Based on the empirical estimation of the deformation amount, a margin for back and forth clamping is left, the clamping force is gradually reduced, and the processing is repeated. until the requirements are met.
Of course, you can also consider making a cover mold to directly cover the workpiece and press it tightly to ensure that it will not bend and act like glue. But this depends on the specific processing requirements and is not universal.
Finally, if a worker wants to do his job well, he must first sharpen his tools. It is still recommended that you use a specialized aluminum processing center.
Small area aluminum plate processing center
Why do you say that? Because this type of equipment is specially developed for the aluminum or non-metal processing industry, its efficiency will be much higher than that of general machining centers!
The workbench is configured as a universal T-slot workbench, with an optional vacuum adsorption workbench (our factory is equipped with double workbench as standard). Configure cutting spindles with a wider speed range for the industry. For example, in our factory, it is from 4000-24000RPM. Under the premise of ensuring a certain processing accuracy (generally around 0.03mm, our factory's is generally higher, 0.02mm downward), the XY axis and rack transmission are used to make the processing efficiency higher.
The aluminum processing center has multiple functions such as drilling, milling, and tapping, and can process materials such as aluminum, copper, titanium alloy, PC, PA, bakelite, FR4, and wood boards. At the same time, the aluminum processing center has high precision and high processing efficiency, and is suitable for personalized periodic production. It is very suitable for packaging mold processing, automobile parts processing, aerospace parts processing, electrical and electrical parts and other industries.
It is more suitable for the industry than general machining centers, and the price is also more advantageous. Moreover, you can always find professional technical personnel from the manufacturer for process guidance. It is definitely a powerful tool for aluminum processing.
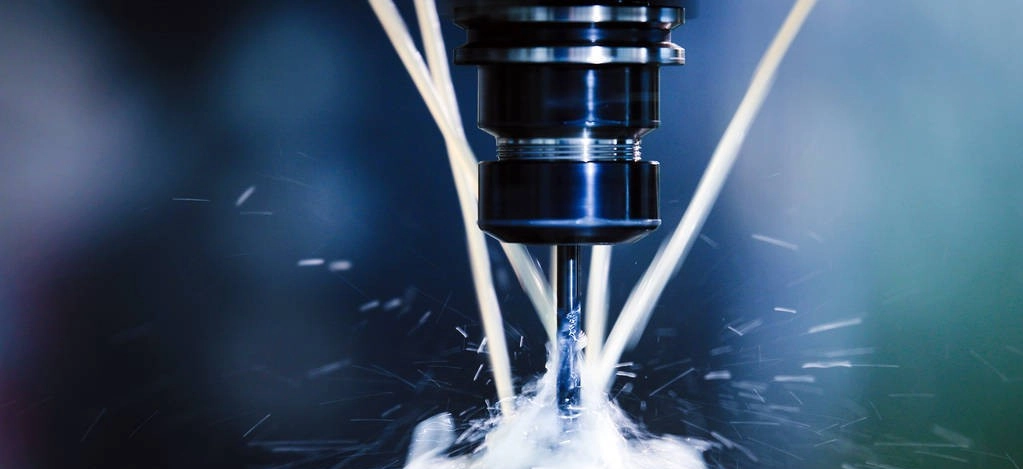