Popular Science | Mechanical Engineers Tell You 19 Plastic Processing Skills
Plastic molding is the process of shaping plastics in various forms (powders, granules, solutions and dispersions) into products or blanks of the desired shape. The manufacturing process of most cosmetic packaging products mainly involves four key processes: mold forming, surface treatment, printing, and assembly. The molding process is an indispensable key link. Today, the editor will give you a quick look at 19 plastic molding processes.
Injection molding
It is a method of producing industrial product shapes. Products are usually made of rubber injection molding and plastic injection molding. Injection molding can also be divided into injection molding and die casting.
Extrusion molding
The material is heated and plasticized through the interaction between the extruder barrel and the screw, and is pushed forward by the screw and continuously passes through the machine head to be made into various special-shaped products or semi-finished products. part.
Rotational molding
Also known as rotational molding, rotational molding, rotational molding, rotary casting, rotational molding, etc., this molding method is to first add measured plastic (liquid or powder) into the mold, and after the mold is closed, it is molded along both sides. The vertical rotary axis rotates while heating the mold. Under the action of gravity and heat energy, the plastic raw materials in the mold are gradually and evenly coated, melted, and adhered to the entire surface of the mold cavity, forming the same shape as the mold cavity. After cooling, shaping and demoulding, the product in the desired shape is obtained.
Blow molding
Also known as hollow blow molding, it is a rapidly developing plastic processing method. Put the tubular plastic parison obtained by extrusion or injection molding of thermoplastic resin into the split mold while it is hot (or heated to a softened state). After the mold is closed, compressed air is immediately introduced into the parison to blow the plastic parison. It expands and adheres tightly to the inner wall of the mold. After cooling and demoulding, various hollow products are obtained.
Blister molding
A plastic processing technology whose main principle is to heat and soften a flat hard plastic sheet, then use vacuum to adsorb it to the surface of the mold, and then cool it to form. It is a technical process used in all walks of life.
Compression molding
Also known as press molding or compression molding, it is an operation in which powdery, granular or fibrous plastic is first placed into the mold cavity at molding temperature, and then the mold is closed and pressurized to form and solidify. Compression molding can be used on thermosets, thermoplastics and rubber materials.
Calendering
The melted and plasticized thermoplastic passes through the gap between two or more parallel counter-rotating rollers, causing the melt to be squeezed, stretched, and stretched by the rollers to become a continuous sheet with certain specifications and quality requirements. product. Finally, the natural cooling molding method is used for processing.
foam molding
It is a process of adding appropriate foaming agents to foam materials (PVC, PE, PS, etc.) to create microporous structures in plastics.
Winding forming
The process is to wind continuous fibers (or cloth tapes, prepreg yarns) impregnated with resin glue around a mandrel according to a certain pattern, and then solidify and demould to obtain the product.
Laminated molding
It refers to a molding processing method that combines multiple layers of the same or different materials into a whole under heating and pressure.
Painting and molding
It is a process that uses plastisol or organosol to coat the surface of substrates such as cloth or paper to make imitation leather products, varnished cloth or plastic wallpaper, or coat powder plastic on metal surfaces.
casting
It is a method of plastic processing. In early casting, liquid monomer or prepolymer or polymer is injected into the mold under normal pressure. After polymerization and solidification, it becomes a product with the same shape as the inner cavity of the mold.
Drop plastic
This technology takes advantage of the state-changeable characteristics of thermoplastic polymer materials, that is, it has viscous flow characteristics under certain conditions and can return to a solid state at room temperature. Appropriate methods and specialized tools are used for inkjet to achieve viscosity. The flow is molded in them into the designed shape as required and then solidified at room temperature.
Cold press forming
It is a type of compression molding. Different from ordinary compression molding, the material is pressed and molded at room temperature. After demoulding, the molded product can be cured by heating again or chemical action.
Compression molding
Mainly used in the production of thermosetting plastic products. After molding, it is heated and melted, pressurized and punched, then heated and cross-linked to solidify, and the finished product is obtained after demoulding.
resin transfer molding
It is the process of injecting resin into a closed mold to penetrate the reinforcement material and solidify.
extrusion
It is a pressure processing method that uses a punch or punch to pressurize a blank placed in a concave mold to cause plastic flow, thereby obtaining parts corresponding to the shape of the die hole or concave and convex mold.
thermoforming
It is a special plastic processing method that processes thermoplastic sheets into various products.
3D printing
It is a rapid prototyping technology. It is a technology that uses adhesive materials such as powdered metal or plastic to construct objects by printing layer by layer based on digital model files.
Data integration comes from the Internet
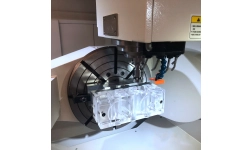