Copper Processing Plant Vertical Furnace Flue Gas Waste Heat Recovery: Green Conversion From Energy Consumption Point To Degreasing Tank Heating
With the rise in global energy costs and tightening of environmental protection policies, the demand for energy conservation and emission reduction in industrial sectors has become increasingly urgent. As one of the industries of high-energy consumption, if the waste heat of flue gas generated during the production process is directly discharged, it will not only lead to energy waste, but also increase the environmental burden. This paper takes the 520℃ high-temperature gas waste recycling project as an example, and deeply analyzes the application principle, technical advantages and the comprehensive benefits of refueling heat exchangers in reducing storage tank heating to provide the industry with a replicated green upgrade solution.
1. Necessity of waste heat recovery in copper treatment industry
During the copper treatment process, as the core equipment, the flue gas temperature generated by natural gas combustion is higher than 520℃. In traditional processes, these high-temperature flue gases are usually directly discharged without treatment, resulting in a heat loss of about 30%-40%. Meanwhile, as a key connection to the surface treatment of copper materials, degreasing tanks usually rely on electrical heating or steam boiler heating, and the energy consumption cost remains high.
The waste heat of the flue gas can be recovered through a gas-water heat exchanger, which can convert the waste heat into hot water required for the degreasing water tank, thereby achieving closed-loop energy utilization. According to statistics, such technologies can reduce heating energy consumption in degreasing tanks by 50%-70%, while reducing carbon emissions by more than 15%.
2. Working principle and design optimization of refueling heat exchanger
1. Core working principle
The gas-water heat exchanger uses metal pipe walls to transfer the heat from high-temperature gas to cold water medium according to the principles of heat conduction and convection. The specific process is as follows:
Flue gas side: The 520°C flue gas discharged from the vertical furnace enters the outer space of the heat exchanger tube, and transfers heat through the pipe wall to the cold water in the tube;
Water side: Cold water absorbs heat in the pipe and heats it to the target temperature (usually 80°C-120°C) cnc inquiry and transports it to a degreased storage tank heating system;
Flue gas cooling: After heat exchange is completed, the flue gas temperature drops below 150° and reduces, meeting environmental protection emission standards.
2. Special design of copper processing
Lightweight tube structures replace fin tubes: Because the flue gas contains traces of metal dust, if fin tubes are used, it is easy to block due to dust accumulation or deformation at high temperatures. Lightweight piping design reduces maintenance frequency and extends the service life of the equipment;
Strengthen heat transfer technology: Add spiral spoilers to the pipes to allow water to flow and improve heat transfer efficiency by more than 20%;
Dual process layout: Cold water flows first through the high-temperature part and then returns to the low-temperature part to maximize the use of the temperature difference and ensures a thermal recovery rate of ≥85%.
3. Analyze implementation cases and technical advantages
1. Project overview of copper processing plants
The factory's vertical furnace emits 120,000 cubic meters of flue gas per day, while the original degreased tank consumes about 1.8 million kilowatt-hours of electricity per year. After introducing the gas-water heat exchange system:
Energy saving and efficiency: annual heat recovery is equivalent to reducing standard coal consumption by 420 tons, reducing power in storage tanks by 65%;
Environmental Benefits: Reduce emissions of 1,100 tons of carbon dioxide each year, and reduce the flue gas emission temperature from 520°C to 130°C, greatly reducing thermal pollution.
2. Summary of technical advantages
High efficiency and energy saving: heat exchange efficiency is as high as 90%, and heat recovery rate is 30% higher than that of traditional equipment;
High temperature and corrosiveness: Made of 316L stainless steel or ND steel, adapting to high temperature and weak acid flue gas environment of 520℃;
Intelligent control: Integrate temperature sensors and variable frequency pumps to achieve dynamic adjustment of heat and avoid excessive energy consumption;
Compact structure: The modular design covers a small area suitable for refurbishing existing production lines. The construction period is only 15-20 days.
4. Economic interests and social values
1. Direct economic returns
The investment recovery period is very short: taking a medium-sized copper factory as an example, the equipment investment is about RMB 1.2 million, saving RMB 800,000 in annual energy costs and can recover the costs within 1.5 years;
Low operating and maintenance costs: Light pipe structures reduce cleaning frequency, with annual maintenance costs less than 5% of the total investment.
2. The significance of sustainable development
Policy compliance: meet the requirements of “technical specifications for energy saving of industrial boilers” and avoid the risks of environmental protection punishment;
Brand Enhancement: Pass the green production certification, improve the enterprise ESG rating and help develop the high-end market.
5. Future prospects and technological upgrade directions
With the development of materials science and intelligent control technology, gas-water and heat exchangers will further develop towards high efficiency and intelligence:
Nanotechnology: Coating the tube wall with graphene to enhance heat transfer coefficient and inhibit dust accumulation;
Use waste heat cascade: In combination with heat pump systems, the waste heat at medium and low temperatures is converted into high-level heat energy and extended to other uses such as factory heating;
Digital twin monitoring: Real-time optimization of heat exchange parameters through IoT platform to maximize energy efficiency.
in conclusion
The copper processing plant of the vertical furnace factory of the copper gas waste gas heat recovery project successfully transformed "waste heat" into "resources" through the innovative application of innovative gas-water heat exchangers, thus achieving a win-win situation between economic and environmental welfare. This technology path not only provides a replicable energy-saving model for the copper processing industry, but also injects new impetus into the green conversion of the high-energy consumer industry.
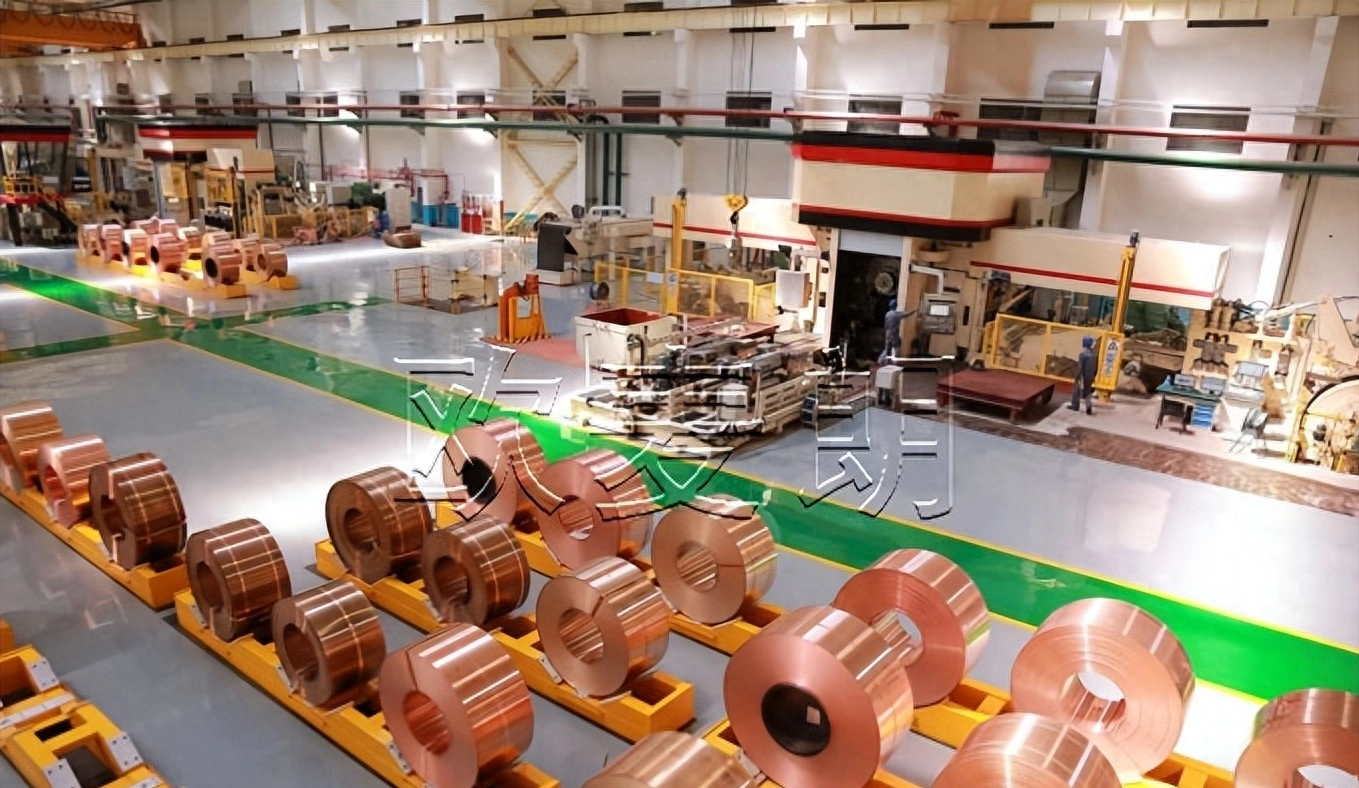