中文yeda| Application Of PCD Tool In Titanium Alloy Processing
Titanium alloys have a wide range of applications in the fields of aircraft, ships, armor and missiles due to their high strength ratio, high corrosion and good high temperature performance. However, these characteristics of titanium alloys also present processing challenges such as high temperature chemical reactivity, low thermal conductivity and low elastic modulus, making titanium alloys one of the difficult materials to handle. When processing titanium alloys, traditional tool materials such as high-speed steel and cemented carbides often face severe wear and low processing efficiency. Therefore, it is especially important to find tool materials that are more suitable for titanium alloy processing.
PCD (poly crystal diamond) tools are one of the ideal choices for treating titanium alloys due to their excellent hardness and wear resistance, high thermal stability and chemical stability, and excellent thermal conductivity. The hardness of PCD tools is much higher than that of cement carbides and high-speed steel. It can resist cutting forces and cutting heat generated during titanium alloy processing, reduce tool wear, thereby improving processing efficiency and processing quality.
In recent years, significant progress has been made in the research on titanium alloys that deal with PCD tools. Research shows that when cutting titanium alloys, PCD tools can maintain higher cutting speeds and reduce cutting forces while achieving better handling surface quality. For example, under dry cutting conditions, the PCD tool can obtain the same surface roughness as grinding when the cutting speed reaches 120 m/min, and the average surface roughness is lower than that of the carbide tool. In addition, the use of high-pressure cooling treatment methods can further extend the life of the PCD tool and obtain a better treatment surface layer.
However, there are some challenges in handling titanium alloys with PCD tools. Titanium alloys produce greater cutting heat during cutting, and despite the high thermal stability of PCD tools, thermochemical wear may still occur under extreme conditions. Therefore, it is necessary to select appropriate cutting parameters and cooling methods during the processing to reduce the temperature of the cutting area and reduce tool wear. In addition, the blade shape and geometric parameters of the PCD tool also have an important impact on the processing effect. Using positive geometric inserts can reduce cutting forces, cutting heat and workpiece deformation, thereby improving processing quality.
In practical applications, the processing effect of PCD tools is also affected by various factors (such as workpiece material, cutting parameters CNC part, tool geometry and cutting fluid). Therefore, when processing titanium alloys, it is necessary to select appropriate PCD tools and cut parameters according to specific processing requirements and conditions to obtain the best processing effect.
To sum up, PCD tools show great application potential in titanium alloy treatment due to their excellent performance. With the continuous development of technology and the deepening of research, the processing efficiency and processing quality of PCD tools will be further improved, thus providing more reliable tool support for the widespread application of titanium alloys.
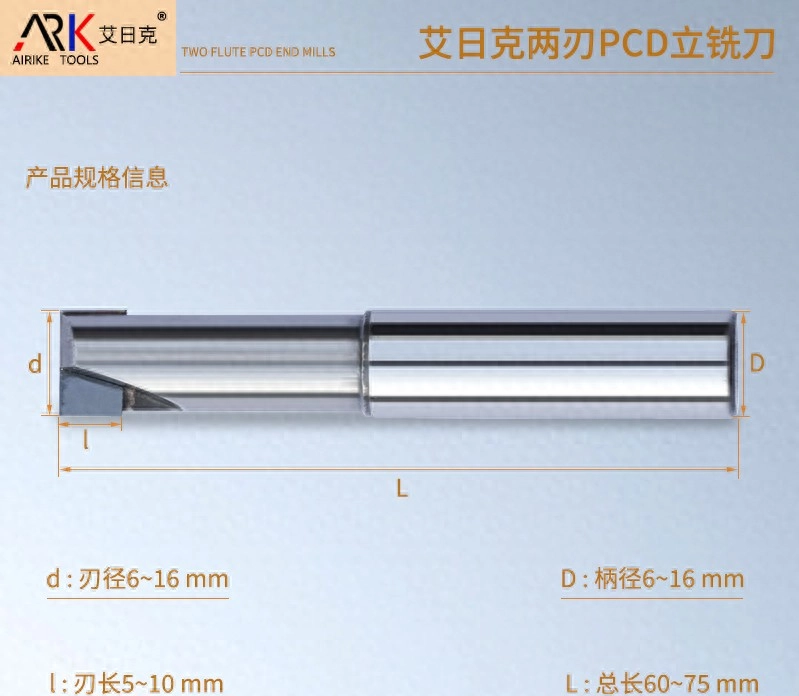