How Powerful Are Tools For Removing High-temperature Alloys?
The reason why aerospace parts are difficult to machine is because the materials are difficult to machine.> , the core components use a large number of nickel-based high-temperature alloy materials; secondly, most of the metal materials must be removed from a single piece of material, and the processing time takes several weeks> ;Third, parts require high precision.> It can be said that the safety and stability of processing are the top priority.
So many powerful tools to remove high-temperature alloys? These are our two players, the latest golden tiger blade material from "Walter"> There are also Tungaloy’s BX815 material knives.>
01>
Walter>
The latest Golden Tiger blade material>
Difficulties in processing
1. High requirements for programming and tooling>
Looking at the shell itself, the parts are generally larger in size, have irregular contours, require a lot of material removal, and have average rigidity. They must be machined on a four- or five-axis machine tool, so the requirements for programming and tools are high: a set of cutting edges must be machined within a certain time. Knives may be slightly worn, but must not chip.
2. Thread processing>
Another processing difficulty is processing threads on high-temperature alloy materials: the traditional method is to use a tap, but if the tap accidentally breaks in the part hole, it will be very troublesome. First, it must be removed using special methods. Secondly, the threads of the part may become damaged and may be scrapped. risk.
Solution>
1. The latest golden tiger blade material>
Walter offers its customers three insert materials: coated carbide, ceramic and CBN inserts. Considering the economy of the cutting tools, most customers will use coated carbide cutting tools. Walter's latest Golden Tiger blade material is fully qualified for this difficult task. The blade matrix contains rare metal elements , so the matrix has good high-temperature red hardness and toughness . With Walter's patented Golden Tiger technology and ultra-low pressure CVD-TiAlN coating process , higher hardness and longer life can be achieved. Even if the machining allowance is uneven or the tool overhang is long, edge chipping will not occur. In this way, the tool change interval is longer, the processing is safer, and there is no risk of parts being scrapped.
Processing case
2.Thread milling cutter TC630>
Walter has specially developed the thread milling cutter TC630cnc manufacture for such working conditions, which can meet the needs of metric [M1.6 - M18], inch [UNC No.1-64 - UNC 3/4-10] customers], [UNF No.1 -72 - UNF 3/4-16], [STI UNF No.10-32 - STI UNF 3/8-24] Various specifications, cutting edge design equipped with Megatron() technology . Since the process is changed from tapping to thread milling, the surface quality of the processed threads is better, and the thread tolerances are accurately controlled. Since the diameter of the tool is smaller than the diameter of the thread bottom hole, the risk of the tool being damaged and difficult to remove is avoided, making processing simpler, safer and more efficient.
02>
Tacro>
BX815 material cutting machine
Difficulties in processing>
High-speed machining can lead to increased wear and tool tip breakage, thereby limiting production efficiency.>
Because process safety and quality are of paramount importance, manufacturers of critical components for the aerospace industry have strict requirements for the surface integrity of finished products. Existing machining processes often use traditional PVD-coated carbide inserts for machining because high-speed machining increases wear. The problem of tool tip breakage is quite prominent, which seriously restricts production efficiency.
Solution>
Tungaloy has launched CBN material processing solutions for difficult-to-process materials such as high-temperature alloys. Especially in the finishing process, Tungaloy BX815 material can ensure long and stable tool life.
BX815 material
BX815 metallographic structure diagram
BX815 material properties:
▶BX815 contains submicron-sized fine CBN particles and an alumina binder to obtain a material with high thermal stability;
▶ Evenly distributed zirconia particles improve chip resistance;
▶ Achieve high-speed processing of nickel-based high-temperature alloys such as 718, achieving higher processing efficiency than traditional materials;
▶ The matrix with evenly distributed CBN and binder in the material enables high surface accuracy quality under high cutting parameters.
The new BX815 grade inserts offer two edge treatments optimized for surface integrity: LT chip breaker with a slight chamfer and ground edge, commonly found in PCBN inserts for superalloy machining, and E-shaped chip breaker with a slight chamfer edge, suitable for low cutting forces.
BX815-grade inserts can also provide customized edge processing to achieve optimal performance in target areas, while also ensuring process safety and processing efficiency under high-temperature and high-speed machining conditions.
BX815 material blade treatment type
Processing cases>
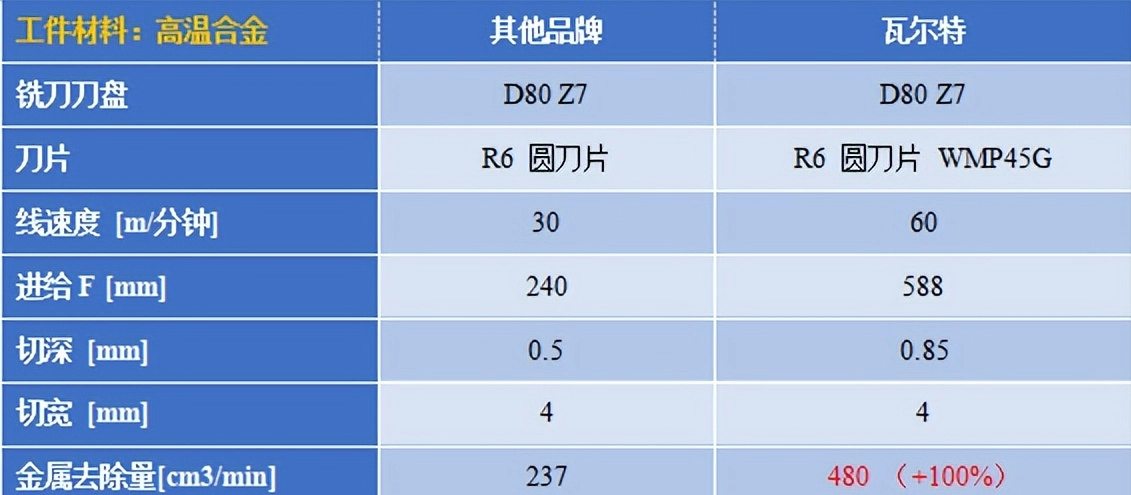