Innovation And Development Of Plastic Blow Molding
Plastics are an indispensable material in modern life and have penetrated into every corner of our lives. From packaging to construction, from medical equipment to everyday supplies, plastic applications are almost everywhere. In many plastic processing technologies, plastic blow molding has become an important part of the plastics industry, with its unique advantages and a wide range of applications. Depth of discussionPlastic blow molding> Process principles, application areas, environmental challenges and future development trends will bring you into the mystery and charm of the technology.
Plastic blow molding is a method of heating and softening plastic using air pressure to expand the mold cavity and close to the mold cavity wall, and finally cooling and mold. This process can produce hollow plastic products such as bottles, containers, cnc manufacturers, toys, etc. Its core steps include the preparation of plastic raw materials, the use of extruders or injection molding machines, the formation and inflation of Parison, cooling and molding, and the de-definition and subsequent treatment of the finished product.
During the blow molding process of plastics, the choice of raw materials is crucial. Common plastic materials include polyethylene (PE), polypropylene (PP), polyethylene glycol diphthalate (PET), etc. The choice of these materials depends on the product's performance requirements and cost budget. For example, pets are often used in the production of food and beverage bottles due to their transparency and chemical stability. Although PP is suitable for the production of automotive parts and household appliance shells due to its heat and chemical resistance.
The advantages of plastic blow molding are its high production efficiency, good product consistency and the ability to produce large hollow structures. In addition, investment in blow molding equipment is relatively low compared to other molding methods, and mold replacement is flexible and can quickly adapt to the needs of different product designs. However, this process also has some disadvantages, such as uneven distribution of product wall thickness, low precision in size and high requirements for operator skills.
With the development of science and technology and society, plastic molding is facing new opportunities and challenges. On the one hand, the market demand for high-quality and high-performance plastic products has been growing, which has promoted the innovation and development of blow molding technology. For example, the emergence of multi-layer co-cutting blow molding technology makes the product more functional, such as obstacles, UV resistance, etc. On the other hand, environmental protection requirements have prompted the plastics industry to seek more sustainable solutions. The research and development of biodegradable materials and the concept of circular economy are gradually changing the face of the traditional plastics industry.
Looking ahead, plastic blow molding will continue to develop under the promotion of new materials, new technologies and new applications. The application of intelligent manufacturing and automation technologies will further improve production efficiency and product quality, and reduce labor costs and resource waste. At the same time, the development and application of green plastics will become an important direction for industry development to meet global concerns about environmental protection.
In short, as an efficient and economical plastic processing technology, plastic blow molding technology plays an important role in modern society. In the face of future challenges, continuous technological innovation and sustainable development will become the driving force for its continuous progress. By optimizing processes and adopting new materials and technologies, plastic blow molding is expected to bring more convenience and comfort to our lives while protecting the environment.
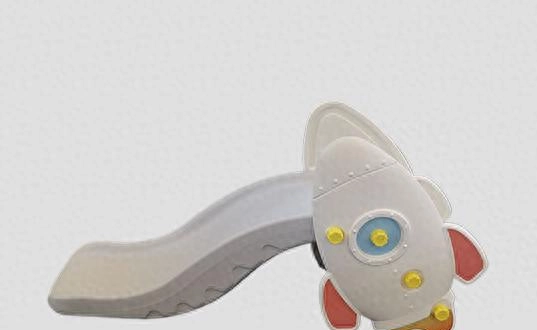