Solve The Fluidity Problem In Flame Retardant Plastic Processing: The Wonderful Use Of Magnesium Hydroxide
Surface-modified magnesium hydroxide plays an important role in solving the fluidity problem of flame retardant plastic processing. Here are some key useful points:
Improve compatibility
Principle: Ordinary magnesium hydroxide has poor compatibility with polymer materials and is easy to combine to form large particles, resulting in defects in the plastic matrix and affecting fluidity and mechanical properties. Surface-modified magnesium hydroxide has reduced surface energy and has enhanced interface bonding forces with plastics, thereby better dispersing the plastic matrix.
For example: After surface modification of magnesium hydroxide using silane coupling agents, chemical bonds, such as covalent or hydrogen bonds, can be formed with the polymer, thereby making the interface between magnesium hydroxide particles and the polymer significant, And very compatible. Improvements effectively reduce liquidity problems due to poor compatibility.
Reduce melt viscosity
Principle: Unmodified magnesium hydroxide easily forms aggregates in plastics, thereby increasing the internal friction of the melt, thereby increasing the melt viscosity and poor fluidity. The surface-modified magnesium hydroxide particles dispersed more evenly, thereby reducing aggregation and thus reducing the viscosity of the melt.
For example: In some experiments, plastic melts with unmodified magnesium hydroxide have high viscosity and are difficult to process. After the same amount of surface-modified magnesium hydroxide is added, the melt viscosity is greatly reduced and the fluidity is improved, so that plastics are more likely to form during extrusion or injection molding.
Optimize rheological performance
Principle: Magnesium modified on the surface of magnesium hydroxide can change the arrangement and internal structure of plastics, thereby affecting the rheological behavior of plastics. It can make the flow of plastic more stable and uniform during processing, thereby reducing problems such as shear rate sensitivity and flow instability.
For example: In rheology tests, it was found that after adding an appropriate amount of surface modified magnesium hydroxide, the viscosity of the plastic becomes more stable with the shear rate and the non-Newtonian characteristics are weakened, which helps to improve this Characteristic plastic filling capability of plastic in complex molds. Reduce styling defects such as short lenses and flashes.
Improve processing efficiency
Principle: Because surface-modified magnesium hydroxide improves the fluidity of plastics, plastics can be filled with mold faster during processing, shortening molding cycles and improving production efficiency. At the same time, good fluidity also helps reduce processing temperature and pressure, reduce energy consumption and equipment wear.
For example: In actual production, the molding time of plastic injection parts using surface modified magnesium hydroxide is reduced by 10%-20%, while the quality of the product is more stable and the waste rate is much more stable.
Work in concert with other additives
Principle: Magnesium hydroxide surface modified magnesium can work in conjunction with other processing aids (such as plasticizers, lubricants, etc.) to further improve the processing fluidity of the plastic. Plasticizers can weaken the forces between polymer molecules and increase the flexibility of the molecular chains. Lubricants can reduce friction between plastics and processing equipment. When used in combination with surface-modified magnesium hydroxide, these additives cooperate with each other to produce a synergistic effect.
For example: In production of rigid polyvinyl chloride (PVC) pipes, surface-modified magnesium hydroxide is used in combination with an appropriate amount of plasticizer and lubricant, which not only improves the flame retardant performance of the pipe, but also greatly improves processing. handling. Material. Flowability improves the surface surface and dimensional accuracy of the pipe.
In short, magnesium hydroxide can effectively solve the problem of fluidity hindering plastic processing by improving compatibility, reducing melt viscosity, optimizing rheological properties, improving processing efficiency and synergistically with other additives. , providing important support for improving product quality and reducing production costs.
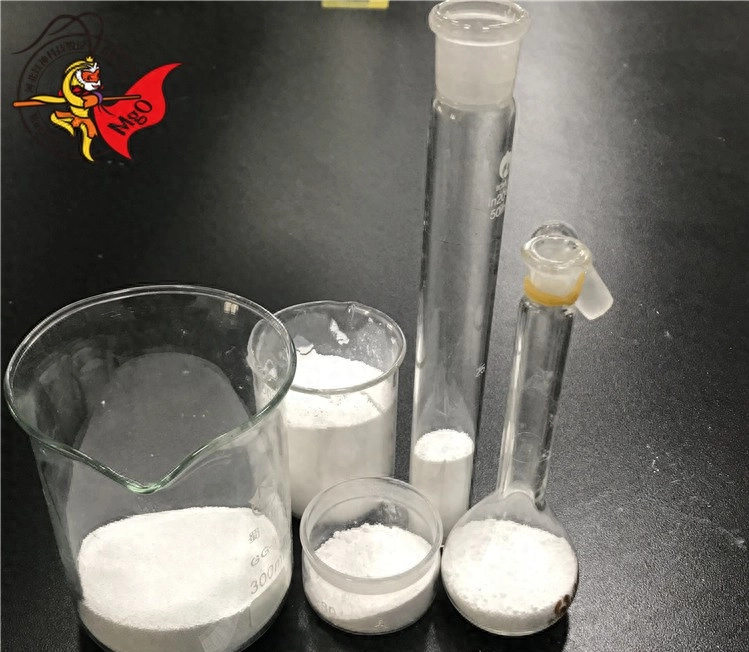