What Are The Industry Standards For CNC Processing?
In the field of CNC machining, there are diverse machine configurations, imaginative design solutions, cutting speed selection, size specifications and type of processing materials. However, not every design can be seamlessly connected to every processing process. Again, not all functions can be handled accurately to any size, and not all types of materials can withstand any cutting speed. An incompatible design with cutting speed or specific features with the desired size is likely to result in safety risks or some form of machining failure.
To guide the implementation of processing technology, a series of standards have been formulated. Some of these standards come from the accumulation of long-term trials, errors and practical experience, while the other is obtained through carefully planned scientific experiments. In addition, CNC companies, the International Organization for Standardization (ISO) has officially recognized some standards and enjoys international authority. Other standards, although informal, are well known in the industry, with slightly different standards.
Design Standard>
Design standards are informal guiding principles and are specifically used to guide computer-aided design links in the CNC machining design process. This set of standards focuses on the geometric specifications of parts. It should be clear that these standards serve as suggestive reference only and that their specific applications can be adapted due to performance differences in CNC machine tools and different practices of processing companies.
Tube wall thickness>
During the process, the vibration generated may cause insufficient wall thickness or deformed parts, which is especially important when the material is stiffer. Generally speaking, the standard minimum wall thickness for metal walls is set to 0.794 mm, while the standard minimum wall thickness for plastic walls is 1.5 mm.
Hole/Cavity Depth>
An overly deep cavity may make it difficult to perform milling operations efficiently, as this may be due to tool drape or tool offset. In some cases, the tool cannot even reach the surface that needs to be processed. To ensure machining, the minimum depth of the cavity should be at least four times its width, i.e., if the width of the cavity is 10 mm, the depth must not exceed 40 mm.
Hole>
It is recommended to design holes according to existing standard drill bit sizes. As for the depth of the hole, it is generally recommended to design based on a standard depth of 4 times the diameter. Although in some cases, the maximum depth of the hole can extend to 10 times the nominal diameter.
Function size>
The key design criteria for high-rise structures such as walls is the ratio of height to thickness (H:L). Specifically, this means that if the width of the function is 15 mm, its height should not exceed 60 mm. In contrast, for small holes (such as holes), they may be as small as 0.1 mm in size. However, for practical application reasons, 2.5 mm is recommended as the minimum design standard for these small functions.
Part size>
Currently, ordinary CNC milling machines are widely used and are usually able to handle workpieces with dimensions of 400 mm x 250 mm x 150 mm. CNC lathes can usually handle workpieces with a diameter of φ500mm and a length of 1000mm. When facing large parts with sizes of 2000 mm x 800 mm x 1000 mm, an oversized CNC machine is required for processing.
Tolerance>
Tolerance is a key consideration in the design process. However, it should be noted that the application of tolerances should focus on key features, as excessively loose tolerances can lead to significant improvements in processing time and cost. The tolerances set in the design should be determined based on the tolerance function of the CNC machine tool used. Although precise tolerances of ±0.025 mm can be technically achieved, in fact, 0.125 mm is generally considered a standard tolerance range.
ISO Standard>
ISO standards are official norms officially recognized by the International Organization for Standardization. In the CNC machining field, there are hundreds of ISO standards to comply. Here are some of the most critical criteria.
ISO 230
This is a series of 10-part standard standards that determine the geometric accuracy of a machine tool operating in quasi-static or unloaded conditions, accuracy and repeatability of the CNC axis, thermal effects of the machine, noise emissions and vibration at the processing level.
ISO 229:1973
This standard is specifically used to specify the speed setting and feed speed of CNC machine tools.
ISO 369:2009
On the body of a CNC machine tool, certain specific symbols and descriptions are usually marked. This standard clarifies the specific meaning of these symbols and their corresponding interpretations.
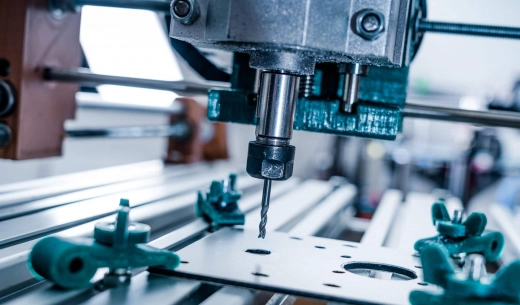