Zhikai 40 Medium Wire Cutting Machine Tool: Innovative Solutions For Beryllium Bronze/Tiol Alloy Treatment In Elastic Assembly
As high-end manufacturing industry flourishes, performance requirements for elastic components are becoming increasingly stringent. Beryllium bronze and titanium alloys have excellent strength, corrosion resistance and good elastic properties, and have become ideal for elastic components in key areas such as aerospace and precision instruments. However, the problem of surface discoloration when dealing with such materials has always been a difficult problem in the industry, seriously affecting the appearance and performance of the product. Recently, we have received many consultations from clients in related fields, eager to find effective solutions to this problem. The 40 centerline cutting machine is equipped with patented high-frequency technology, which brings light to overcome this problem.
1. Analysis of problem handling
1. Difficulty in dealing with beryllium bronze> : Beryllium bronze has high hardness and strength. In traditional wire cutting, due to the instantaneous high temperature caused by emission, it is easy to cause oxidation reactions on the surface of the workpiece, resulting in surface discoloration. In addition, the generation of oxide layers may change the surface characteristics of the material, affecting its conductivity and corrosion, thereby affecting the overall performance of the elastic element. At the same time, beryllium bronze has extremely high requirements for processing accuracy, and slight machining errors may lead to changes in the elastic coefficient of the elastic element, which cannot meet the actual use requirements.
2. Difficulty in treating titanium alloys> : Titanium alloys have active chemical properties and are easily reacted with oxygen, nitrogen and other elements in the air at high temperatures to form a brittle layer with high hardness, which not only causes surface discoloration, but also reduces fatigue strength and toughness. Material. In addition, the thermal conductivity of titanium alloy is very low, making it difficult to dissipate the heat generated during processing, which further aggravates the thermal chemical reaction on the surface and makes the surface discoloration problem more serious. Furthermore, the elastic modulus of titanium alloy is small, which makes it easy to deform during the processing, so it is difficult to ensure processing accuracy.
Titanium alloy
2. Analysis of patented high-frequency technology 40 wire cutting machine tool
1. Technical Principles> : 40 obtained patented high-frequency technology for wire machine tools, with the core lying precisely controlling the discharge frequency and discharge energy. Through high-frequency pulse power supplies, high-energy pulses can be released in a very short time, making the emission process more concentrated and efficient. When processing beryllium bronze and titanium alloys, this high-frequency discharge method can reduce the energy emitted by a single discharge and reduce the temperature peak in the processing area, thereby effectively inhibiting the occurrence of oxidation reactions and avoiding surface discoloration.
2. Technical Advantages> :
1. Avoid surface discoloration> : Compared with traditional wire shearing technology, the patented high-frequency technology obtained can control the temperature of the processing area below the critical temperature of the material oxidation, fundamentally solving the problem of surface discoloration during processing beryllium bronze and titanium alloys. This ensures not only the appearance quality of the product, but also the original properties of the material are not affected.
2. High-precision machining> : High-frequency technology can achieve more refined discharge control, so that the motion trajectory of the electrode lines is more accurate, thus meeting the microscopic accuracy requirements of the elastic elements. Whether in complex shapes or small sizes, the 40 midwire cutting machine can be handled accurately to ensure dimensional accuracy and shape accuracy of elastic components.
3. Improving processing efficiency> : Because high-frequency discharge can quickly erode the material, while ensuring the processing quality, processing efficiency is greatly improved. Compared with traditional processing methods, using 40 medium-sized wire cutting machines to handle elastic components can shorten the processing cycle by 30%-50%, thereby effectively improving production efficiency and reducing production costs.
3. Detailed description of the processing process
1. Preliminary preparation> :
1. Plot Analysis and Programming> : In-depth analysis of its shape, size and accuracy requirements based on the design drawing of elastic components, and program using professional CAD/CAM software to generate accurate processing paths. Ensure that every processing detail can be performed accurately through the machine tool.
2. Workpiece clamping and alignment> : Choose a high-precision fixture to firmly clamp the fixed wafer particles or titanium alloy workpieces on the machine workbench. Advanced alignment instruments (such as electronic level and optical core instruments) are used to accurately align workpieces to ensure that the processing position of the workpiece is consistent with the programming path.
3. Wires and Wires Installation and Adjustment> : Install high-quality electrode wires and accurately adjust the tension and perpendicularity of the electrode wires according to the workpiece material and processing requirements. Suitable electrode wire tension and perpendicularity are key factors in ensuring processing accuracy and stability.
2. Process> :
1. Parameter settings> : According to the material and processing requirements of the workpiece, the machine tool control system has set up relevant parameters of patented high-frequency technology, including discharge frequency, emission energy, pulse width, etc. For the characteristics of beryllium bronze and titanium alloys, the parameter combination is optimized to ensure the stability and efficiency of the processing process.
2. Rough processing> : Use larger emission energy and feed speed for rough treatment to quickly remove most margins, while the process margins are 0.1-0.2mm for subsequent completion. During the rough processing, the intelligent monitoring system of the machine tool is used to monitor the processing status in real time, such as discharge seams, electrode losses, etc.
3. Fine machining> : Switch to a smaller emission energy and feed speed for finishing, using the high-precision control capabilities of patented high-frequency technology to strictly control the accuracy of the processing and surface quality. Through multiple cuttings and fine adjustment of CNC turning, the dimensional accuracy of the elastic element reaches the micron level and the surface roughness reaches RA0.65-RA0.8μm.
4. Handle monitoring and adjustment> : During the entire processing process, the machine tool's intelligent monitoring system continues to work and collects and processes data in real time. Once the exception handling parameters are found or the processing state is unstable, the system will automatically adjust to ensure the smooth progress of the processing process.
3. After processing> :
1. Workpiece cleaning and testing> : After the processing is completed, remove the elastic element from the workbench and place it in a special cleaning device to remove surface processing debris and oil stains. Then, high-precision measuring instruments, such as micron, three-coordinate measuring instruments and roughness measuring instruments, are used to conduct a comprehensive inspection of the dimensional accuracy, accuracy and surface roughness of elastic components.
2. Quality analysis and feedback> : Perform a detailed analysis of the inspection data and evaluate whether the processing quality of the elastic components meets the design requirements. If quality problems are found, please find the reasons in time, such as improper processing parameters setting, excessive electrode loss, etc., and make corresponding adjustments and improvements. Feedback to the R&D department and the process department of experience and problems during the process process provides a foundation for product optimization and process improvement.
4. Actual case processing
To more intuitively demonstrate the outstanding effect of the 40 intermediate line shear machine in elastic components of beryllium bronze and titanium alloys with patented high-frequency technology, we share the following practical processing cases:
1. Berry Bronze Elastic Assembly in Aerospace Field> : Some aerospace companies need to deal with a batch of beryllium bronze elastic components used for key components of aircraft. These elastic elements have complex shapes, very high precision requirements, and have strict surface quality standards, so discoloration is not allowed. After processing using the 40 midwire cutting machine tool, the surface discoloration problem not only successfully solved the CNC plastic, but also fully met the design requirements. After actual flight testing, these elastic components have stable performance and provide reliable guarantees for the safe operation of the aircraft.
2. Precision Instruments in Tiol Alloy Elastic Assembly> : When precision instrument manufacturing companies produce high-end instruments, it needs to deal with titanium alloy elastic components. Surface discoloration and accuracy problems caused by traditional processing methods have always plagued enterprises. After using a 40-center cutting machine, the surface of the processed titanium alloy elastic element is as smooth as the new element, the dimensional accuracy is controlled within ±0.005mm, and the surface roughness reaches RA0.65μm. The companies that produce these elastic components have significantly improved the performance of precision instruments and their products are highly recognized in the market.
From the above actual situation, it can be seen that the patented high-frequency technology equipped with a 40-center cutting machine has significant advantages in solving the problems of elastic elastic components of beryllium bronze and titanium alloys and the surface of titanium alloys. High precision and high efficiency can be ensured. The processing provides strong support for the development of high-end manufacturing industries. If you are interested in operating videos, usage tutorials, maintenance, handling cases and more application solutions, 40 medium walking wire cutting machines, welcome to continue to follow us. You can also communicate with us through private messages or messages. We will continue to share application skills and cutting-edge technologies in machine tools in various fields.
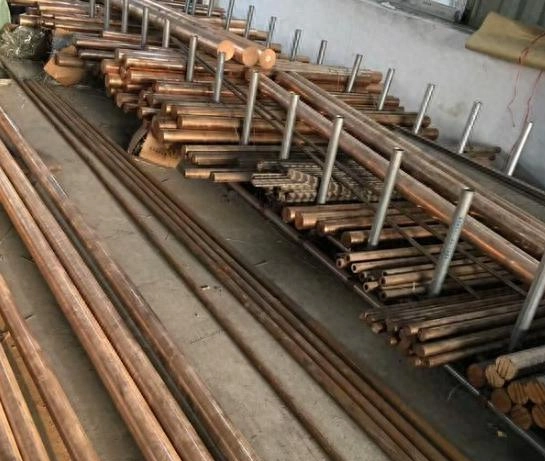