Discover the Best CNC Machining Factory for Precision Universal Joint Production with Exceptional Vibration Isolation Capabilities
Introduction to the Best CNC Machining Factory
In the world of manufacturing, finding the best CNC machining factory is crucial for businesses that rely on high-quality and precise components. A top-notch CNC machining factory possesses state-of-the-art equipment, highly skilled technicians, and a commitment to delivering excellence. Such a factory can handle complex machining tasks with utmost precision, ensuring that the final products meet the highest industry standards.
Advanced Machining Technologies
The best CNC machining factory utilizes advanced technologies to achieve superior results. These technologies include high-speed machining, multi-axis machining, and computer-aided design and manufacturing (CAD/CAM). High-speed machining allows for faster production times without sacrificing accuracy, while multi-axis machining enables the creation of complex geometries. CAD/CAM software ensures precise design and programming, minimizing errors and maximizing efficiency.
Skilled and Experienced Workforce
A key factor that sets the best CNC machining factory apart is its skilled and experienced workforce. The technicians and operators at such a factory have extensive knowledge and expertise in CNC machining. They are trained to operate the advanced machinery with precision and efficiency, and they can quickly troubleshoot and resolve any issues that may arise during the machining process. Their experience also allows them to offer valuable insights and suggestions for improving the design and manufacturing of components.
Quality Control and Assurance
Quality control is of utmost importance in a CNC machining factory. The best factories have rigorous quality control procedures in place to ensure that every component produced meets the required specifications. This includes inspections at various stages of the machining process, such as raw material inspection, in-process inspection, and final inspection. Advanced measuring equipment, such as coordinate measuring machines (CMMs), is used to verify the dimensional accuracy of the components.
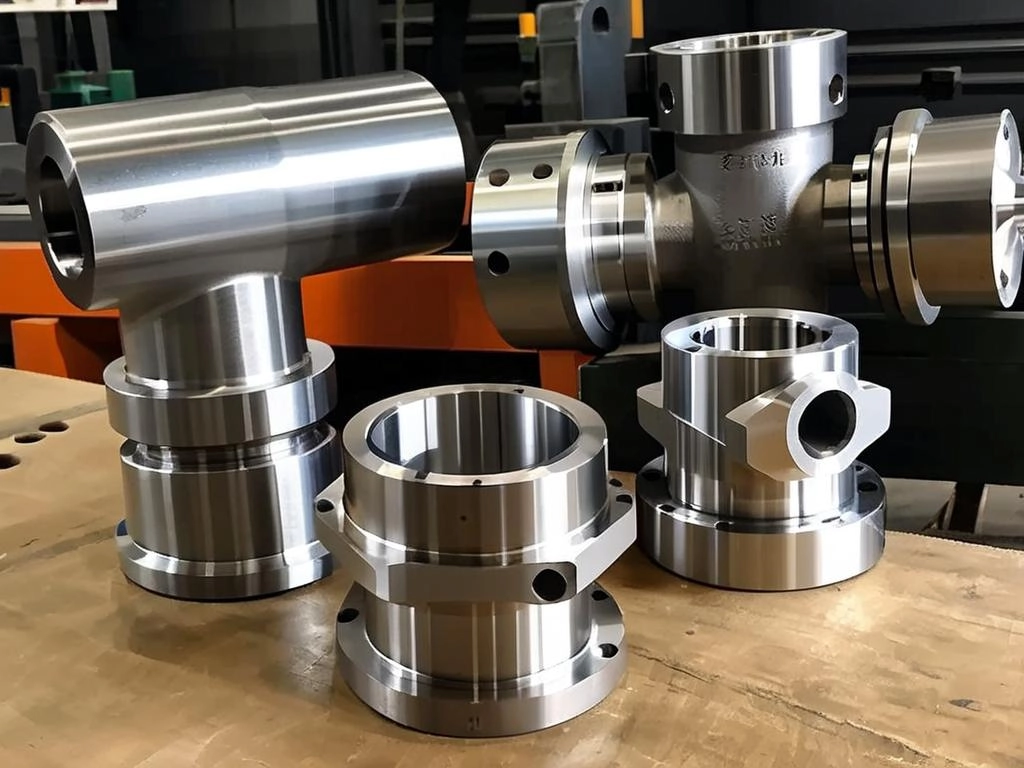
The Significance of Universal Joints
Universal joints play a vital role in many mechanical systems. They are used to transmit torque and rotational motion between shafts that are not in a straight line. This allows for flexibility and smooth power transmission, even in applications where the shafts are at an angle or have some misalignment. Universal joints are commonly found in automotive drivetrains, industrial machinery, and robotics.
Types of Universal Joints
There are several types of universal joints, each with its own unique design and characteristics. The most common types include the cross-type universal joint, the double-cardan joint, and the constant-velocity joint. The cross-type universal joint is simple and cost-effective, but it has limitations in terms of angular displacement. The double-cardan joint offers improved angular displacement capabilities, while the constant-velocity joint provides a constant rotational speed, making it suitable for high-performance applications.
Applications of Universal Joints
Universal joints have a wide range of applications across various industries. In the automotive industry, they are used in the drivetrain to transmit power from the engine to the wheels. In industrial machinery, they are used in conveyor systems, machine tools, and printing presses. In robotics, universal joints are used in robotic arms to provide flexibility and precise movement.
Manufacturing Considerations for Universal Joints
Manufacturing universal joints requires precision and attention to detail. The components of a universal joint, such as the yokes and cross shafts, must be machined to exact tolerances to ensure smooth operation and long service life. The material selection is also crucial, as it affects the strength, durability, and corrosion resistance of the joint. Additionally, proper heat treatment and surface finishing processes are applied to enhance the mechanical properties of the components.
The Importance of Vibration Isolation
Vibration isolation is essential in many applications to reduce the transmission of vibrations and noise. In CNC machining, vibration isolation helps to improve the accuracy and surface finish of machined components. It also reduces the wear and tear on the machinery, increasing its lifespan. In addition, vibration isolation is crucial in sensitive equipment, such as optical instruments and medical devices, to prevent interference and ensure accurate operation.
Methods of Vibration Isolation
There are several methods of vibration isolation, including the use of rubber mounts, spring isolators, and air springs. Rubber mounts are simple and cost-effective, but they have limitations in terms of load capacity and frequency range. Spring isolators offer higher load capacity and better isolation performance at specific frequencies. Air springs provide excellent vibration isolation over a wide frequency range and can handle heavy loads.
Benefits of Effective Vibration Isolation
Effective vibration isolation offers numerous benefits. It reduces the noise and vibration levels in the workplace, creating a more comfortable and productive environment for workers. It also improves the quality of the products by minimizing the effects of vibrations on the machining process. Moreover, vibration isolation can help to comply with regulatory requirements and industry standards related to noise and vibration emissions.
Implementation of Vibration Isolation in CNC Machining Factories
CNC machining factories implement vibration isolation measures in various ways. They may install vibration isolation pads or mounts under the machinery to reduce the transmission of vibrations to the floor. They may also use isolation enclosures or cabinets to protect sensitive equipment from external vibrations. Additionally, proper machine layout and placement can help to minimize the effects of vibrations on adjacent machinery.
Conclusion and Key Takeaways
In conclusion, finding the best CNC machining factory is essential for businesses that require high-quality and precise components, such as universal joints. The best factories have advanced machining technologies, a skilled workforce, and strict quality control procedures. Universal joints are important components in many mechanical systems, and their manufacturing requires precision and attention to detail. Vibration isolation is crucial in CNC machining to improve accuracy and reduce noise and vibration levels. By understanding these factors, businesses can make informed decisions when choosing a CNC machining factory and ensure the success of their projects.