Exploring the World of Cheap CNC Machining: The Significance of Brake Pad Production and Composite Machining CNC Tool Path Planning
Cheap CNC Machining: An Overview
Cheap CNC machining has emerged as a game-changer in the manufacturing industry. It offers a cost-effective solution for producing high-quality components without sacrificing precision and accuracy. With the advancements in technology, CNC machining has become more accessible and affordable, enabling small and medium-sized enterprises to compete in the global market. One of the key advantages of cheap CNC machining is its ability to reduce production costs significantly. By automating the machining process, it eliminates the need for manual labor, thereby reducing human errors and increasing productivity. This not only saves time but also ensures consistent quality across all produced parts.
The Role of Software in Cheap CNC Machining
The software used in CNC machining plays a crucial role in determining its cost-effectiveness. Advanced software allows for precise control of the machining process, enabling manufacturers to optimize tool paths and reduce material waste. It also provides real-time monitoring and feedback, allowing for immediate adjustments to be made if any issues arise. Additionally, user-friendly software interfaces make it easier for operators to program and operate CNC machines, reducing the need for extensive training and expertise.
Materials and Cheap CNC Machining
The choice of materials is another important factor in cheap CNC machining. By selecting appropriate materials, manufacturers can further reduce costs without compromising on quality. For example, using lightweight and durable materials can reduce the overall weight of the components, leading to lower shipping costs. Moreover, some materials are easier to machine, which can result in faster production times and lower tool wear.
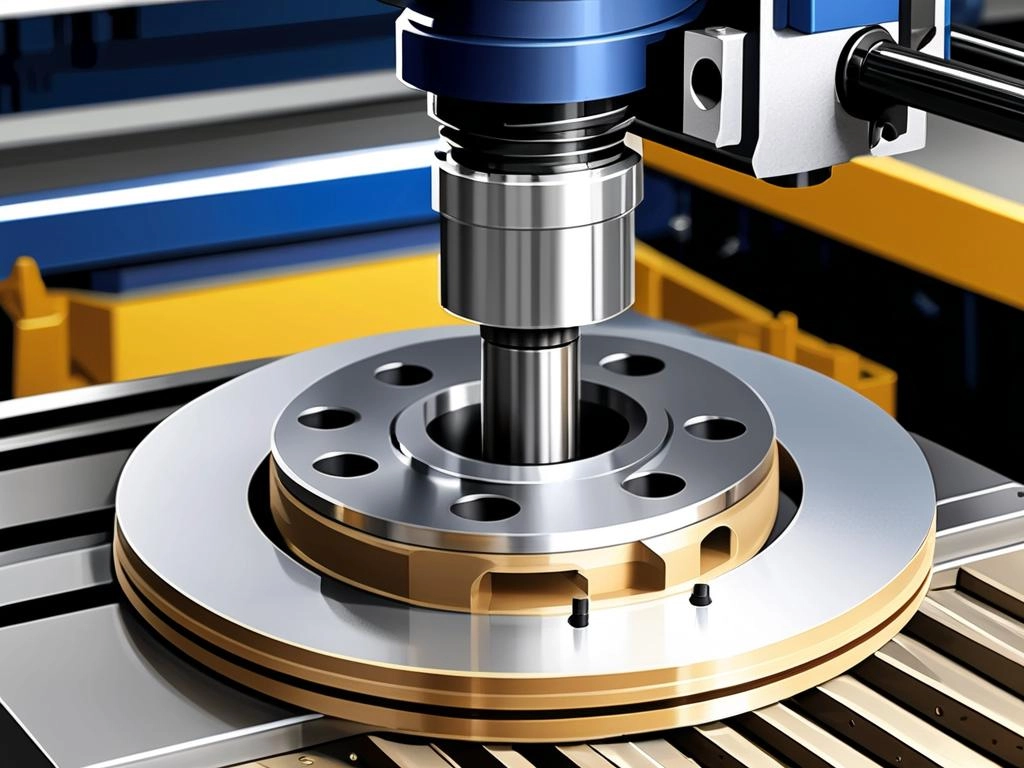
Brake Pad Production through CNC Machining
Brake pads are a critical component in any vehicle's braking system. The production of high-quality brake pads requires precision and accuracy, which can be achieved through CNC machining. Cheap CNC machining offers an ideal solution for brake pad production, as it allows for the precise shaping and cutting of the materials used in brake pads. CNC machines can accurately follow complex tool paths, ensuring that the brake pads are manufactured to the exact specifications required for optimal performance and safety.
Quality Control in Brake Pad Production
Quality control is of utmost importance in brake pad production. CNC machining enables strict quality control measures to be implemented throughout the production process. By using advanced sensors and monitoring systems, any deviations from the desired specifications can be detected and corrected immediately. This ensures that each brake pad produced meets the highest quality standards and is safe for use in vehicles.
Innovation in Brake Pad Design with CNC Machining
CNC machining also allows for innovation in brake pad design. Manufacturers can experiment with different shapes, sizes, and materials to develop more efficient and effective brake pads. For example, by using composite materials and advanced machining techniques, brake pads can be made lighter and more durable, improving the overall performance of the braking system.
Composite Machining CNC Tool Path Planning
Composite machining CNC tool path planning is a complex yet essential aspect of the manufacturing process. Composites are widely used in various industries due to their excellent strength-to-weight ratio and other desirable properties. However, machining composites requires careful planning of the tool path to avoid damage to the material and ensure a high-quality finish. The tool path planning process involves determining the optimal sequence of cutting operations, the speed and feed rates, and the depth of cuts.
Challenges in Composite Machining CNC Tool Path Planning
One of the main challenges in composite machining CNC tool path planning is the anisotropic nature of composites. Composites have different mechanical properties in different directions, which means that the cutting forces and tool wear can vary depending on the direction of the cut. This requires careful consideration when planning the tool path to ensure that the material is machined evenly and without causing excessive damage. Another challenge is the presence of fibers in composites, which can cause delamination and other defects if not machined properly.
Strategies for Effective Composite Machining CNC Tool Path Planning
To overcome these challenges, several strategies can be employed in composite machining CNC tool path planning. One approach is to use adaptive machining techniques, which adjust the cutting parameters based on the real-time feedback from the machining process. This allows for more precise control over the cutting forces and reduces the risk of damage to the material. Another strategy is to use specialized cutting tools and tool geometries that are designed specifically for machining composites.
The Future of Composite Machining CNC Tool Path Planning
The future of composite machining CNC tool path planning looks promising, with ongoing research and development efforts focused on improving the efficiency and quality of the process. Advances in software and simulation technologies will enable more accurate prediction of the machining behavior of composites, allowing for better tool path planning. Additionally, the integration of artificial intelligence and machine learning algorithms may lead to more intelligent and automated tool path planning systems.
Conclusion and Outlook
In conclusion, cheap CNC machining has revolutionized the manufacturing industry, offering a cost-effective solution for producing high-quality components. The production of brake pads through CNC machining ensures the safety and performance of vehicles, while composite machining CNC tool path planning enables the efficient and precise machining of composite materials. As technology continues to advance, we can expect further improvements in these areas, leading to even more efficient and sustainable manufacturing processes. Manufacturers should continue to invest in research and development to stay competitive in the global market and meet the ever-increasing demands of customers for high-quality products at affordable prices.