An In-depth Analysis of CNC Turning Shops Quote for Evaporator Production Amid a Dusty Production Environment
Introduction to CNC Turning Shops Quote
CNC turning shops play a crucial role in the manufacturing industry. When it comes to getting a quote from these shops, there are several factors to consider. A CNC turning shops quote is essentially an estimate provided by the shop for the cost and time required to complete a specific turning job. This quote takes into account various elements such as the complexity of the part to be machined, the materials used, the quantity required, and the specific machining processes involved. For example, if a client needs a custom-made evaporator component, the CNC turning shop will assess all these aspects before providing an accurate quote.
Key Components of a CNC Turning Shops Quote
The first component is the material cost. Different materials have different prices, and the quality and type of material chosen for the evaporator will significantly impact the overall cost. For instance, if a high-grade stainless steel is required for the evaporator due to its corrosion resistance properties, the material cost will be relatively higher compared to a standard steel alloy. The second component is the machining cost. This includes the cost of operating the CNC turning machines, the labor cost of the skilled machinists, and the cost of any special tools or fixtures needed for the job. Complex parts with intricate designs will require more machining time and specialized tools, thus increasing the machining cost.
Factors Affecting the Accuracy of a Quote
One of the main factors is the clarity of the client's requirements. If the client provides detailed and accurate specifications for the evaporator, such as the exact dimensions, tolerances, and surface finish requirements, the CNC turning shop can provide a more precise quote. On the other hand, if the requirements are vague or incomplete, the shop may have to make assumptions, which could lead to inaccuracies in the quote. Another factor is the market conditions. Fluctuations in the prices of raw materials and the availability of skilled labor can affect the cost and, consequently, the accuracy of the quote.
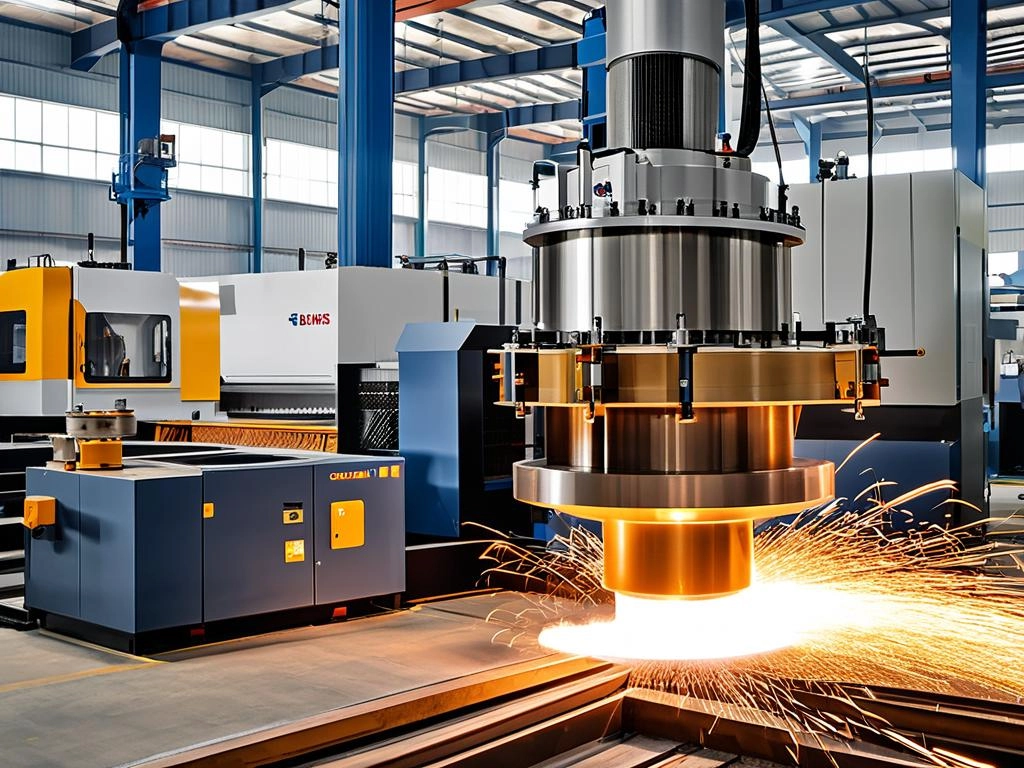
Challenges of Evaporator Production
Evaporators are critical components in many industrial and refrigeration systems. Their production comes with its own set of challenges. One of the primary challenges is ensuring the proper heat transfer efficiency. Evaporators need to be designed and manufactured in such a way that they can effectively transfer heat from one medium to another. This requires precise machining and the use of appropriate materials. For example, the tubes and fins of an evaporator need to be fabricated with high accuracy to ensure maximum heat transfer surface area.
Material Selection for Evaporator Production
The choice of materials for evaporator production is crucial. Different applications require different materials based on factors such as the operating temperature, the type of fluid being evaporated, and the corrosive environment. Copper and aluminum are commonly used materials due to their excellent heat conductivity. However, in some corrosive environments, stainless steel or other alloys may be more suitable. The material selection not only affects the performance of the evaporator but also has an impact on the cost and the manufacturing process.
Design Considerations for Evaporators
The design of an evaporator must take into account factors such as the flow rate of the fluid, the pressure drop across the evaporator, and the overall size and shape constraints. A well-designed evaporator will have an optimized layout of the tubes and fins to ensure efficient heat transfer while minimizing pressure drop. Additionally, the design should also consider ease of maintenance and cleaning to ensure the long-term performance of the evaporator.
Impact of a Dusty Production Environment
A dusty production environment can have several negative impacts on the manufacturing process, especially in the production of evaporators. Dust particles can contaminate the machined parts, affecting their surface finish and dimensional accuracy. For CNC turning operations, dust can interfere with the cutting tools, leading to premature wear and reduced tool life. This, in turn, can increase the cost of tool replacement and affect the production schedule.
Measures to Mitigate the Effects of Dust
One of the effective measures is the implementation of a proper dust control system. This can include the use of dust collectors, air filters, and ventilation systems to remove dust particles from the production area. Regular cleaning and maintenance of the production environment are also essential to prevent the accumulation of dust. Another measure is the use of protective covers and enclosures for the CNC turning machines and the workpieces to minimize the exposure to dust.
Quality Control in a Dusty Environment
Quality control becomes even more critical in a dusty production environment. Inspections and testing procedures need to be more rigorous to ensure that the evaporators meet the required specifications. This may include visual inspections for surface defects, dimensional measurements to check for accuracy, and performance tests to verify the heat transfer efficiency. Any defective parts should be identified and rectified promptly to avoid further issues.
Conclusion and Recommendations
In conclusion, obtaining an accurate CNC turning shops quote for evaporator production is essential for both the client and the shop. It requires clear communication of requirements and a thorough understanding of the various cost factors involved. The production of evaporators presents its own set of challenges, particularly in terms of material selection and design considerations. A dusty production environment can further complicate matters, but with the implementation of appropriate measures, its negative impacts can be mitigated. It is recommended that clients work closely with CNC turning shops to ensure that all aspects of the project are well-planned and executed. Shops, on the other hand, should invest in proper dust control and quality control systems to maintain high production standards.