Exploring the World of CNC Miling Companies and the Significance of Laser Marking, with a Focus on the Mysterious Question: What is the Sampling Ratio?
Introduction to CNC Miling Companies
The Core Business of CNC Miling Companies
CNC Miling companies play a crucial role in the manufacturing industry. They specialize in using Computer Numerical Control (CNC) technology to precisely shape and cut various materials. This technology allows for highly accurate and repeatable production processes. CNC milling machines are capable of working with a wide range of materials, including metals like aluminum, steel, and titanium, as well as plastics and composites. These companies often serve a diverse clientele, from small businesses looking for custom parts to large industrial manufacturers in need of mass-produced components.
Advantages of CNC Miling
One of the main advantages of CNC milling is its precision. The computer-controlled machines can achieve extremely tight tolerances, ensuring that each part produced meets the exact specifications. This level of accuracy is essential in industries such as aerospace and medical device manufacturing, where even the slightest deviation can have serious consequences. Additionally, CNC milling is highly efficient, allowing for faster production times compared to traditional machining methods. It also reduces the need for manual labor, minimizing the risk of human error and increasing overall productivity.
Applications of CNC Miling
CNC milling has a wide range of applications across various industries. In the automotive industry, it is used to produce engine components, transmission parts, and body panels. In the electronics industry, CNC milling is used to fabricate circuit boards and precision components for devices such as smartphones and computers. It is also widely used in the construction industry for creating custom architectural elements and fixtures. The versatility of CNC milling makes it an indispensable technology in modern manufacturing.
The Significance of Laser Marking
What is Laser Marking?
Laser marking is a process that uses a high-powered laser beam to create permanent marks on a variety of materials. These marks can include text, logos, serial numbers, barcodes, and other identifying information. The laser beam interacts with the material's surface, either by engraving, etching, or annealing, depending on the material and the desired effect. Laser marking offers several advantages over traditional marking methods, such as inkjet printing or mechanical engraving.
Advantages of Laser Marking
One of the key advantages of laser marking is its permanence. The marks created by lasers are highly resistant to wear, fading, and corrosion, ensuring that the information remains legible over time. This is particularly important for products that are subjected to harsh environments or frequent handling. Laser marking is also a non-contact process, which means there is no physical contact between the marking tool and the material. This reduces the risk of damage to the material and allows for marking on delicate or sensitive surfaces. Additionally, laser marking is a highly precise process, capable of producing marks with extremely small dimensions and high resolution.
Applications of Laser Marking
Laser marking has numerous applications in various industries. In the medical field, it is used to mark surgical instruments, implants, and medical devices with unique identification codes for traceability and safety purposes. In the electronics industry, laser marking is used to mark circuit boards, chips, and other components with serial numbers and product information. It is also widely used in the automotive and aerospace industries for part identification and quality control. The ability to create permanent, high-quality marks makes laser marking an essential technology for product branding, serialization, and anti-counterfeiting measures.
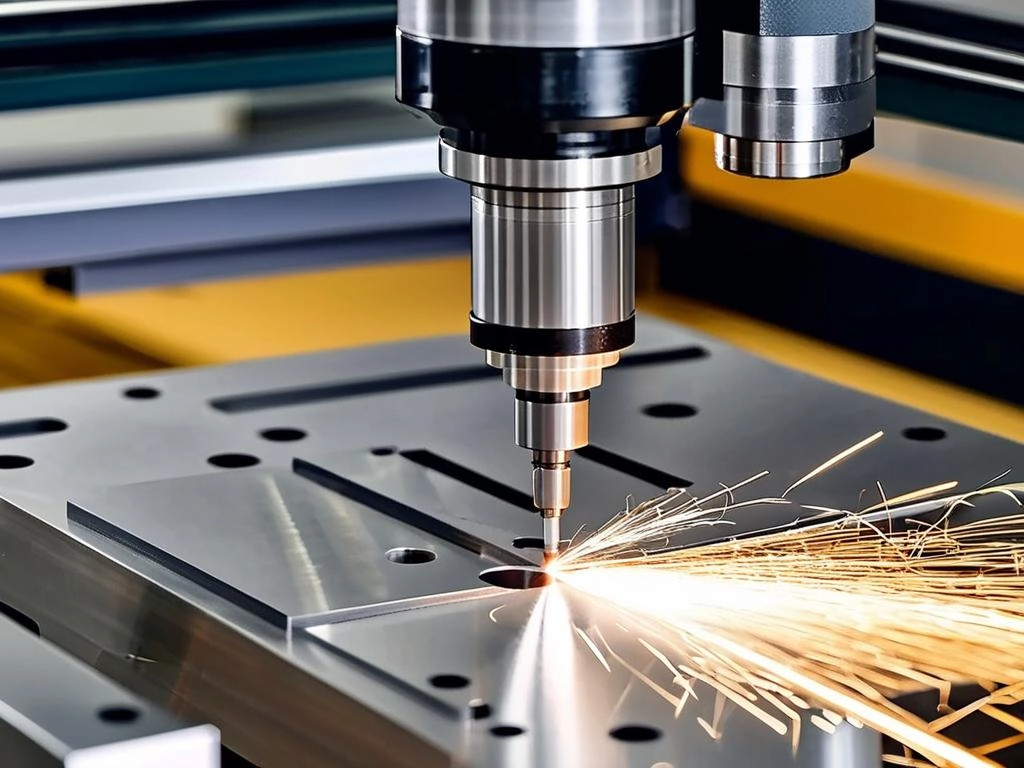
The Mysterious Question: Sampling Ratio?
Understanding Sampling Ratio in Manufacturing
The sampling ratio refers to the proportion of products or parts that are selected for inspection or testing from a larger production batch. In the context of CNC Miling companies and laser marking, determining the appropriate sampling ratio is crucial for ensuring product quality. A too-low sampling ratio may result in undetected defects, while a too-high sampling ratio can be time-consuming and costly. The sampling ratio is typically determined based on factors such as the complexity of the product, the manufacturing process, and the quality requirements of the customer.
Factors Affecting Sampling Ratio
Several factors can influence the sampling ratio. For example, if the CNC milling process is highly automated and has a proven track record of producing consistent, high-quality parts, a lower sampling ratio may be sufficient. On the other hand, if the product has complex geometries or critical dimensions that require precise control, a higher sampling ratio may be necessary. The quality requirements of the customer also play a significant role. If the customer has strict quality standards, a higher sampling ratio may be required to ensure compliance. Additionally, the cost of inspection and testing should also be considered when determining the sampling ratio. If the inspection process is expensive or time-consuming, a balance needs to be struck between the cost of inspection and the risk of undetected defects.
Best Practices for Determining Sampling Ratio
To determine the appropriate sampling ratio, CNC Miling companies and manufacturers using laser marking should follow some best practices. First, they should conduct a thorough risk assessment of the manufacturing process and identify potential sources of defects. Based on this assessment, they can determine the critical control points where inspection and testing are most necessary. Second, they should consider historical data on product quality and defect rates. If there is a history of high-quality production, a lower sampling ratio may be appropriate. However, if there have been issues with quality in the past, a higher sampling ratio may be needed. Finally, they should communicate with the customer to understand their quality requirements and expectations. By working together, both the manufacturer and the customer can determine a sampling ratio that meets the needs of both parties.
Conclusion
In conclusion, CNC Miling companies and laser marking technologies are integral parts of modern manufacturing. CNC milling offers precision and efficiency in producing a wide range of products, while laser marking provides a reliable and permanent method of marking and identification. The question of sampling ratio is an important consideration for ensuring product quality, and it should be determined based on a careful assessment of various factors. By understanding the capabilities and applications of CNC milling and laser marking, and by implementing appropriate sampling strategies, manufacturers can produce high-quality products that meet the demands of their customers and the requirements of the market.