Unlocking the Potential of New Energy CNC Milling with Transistor Socket and Optimized Lighting
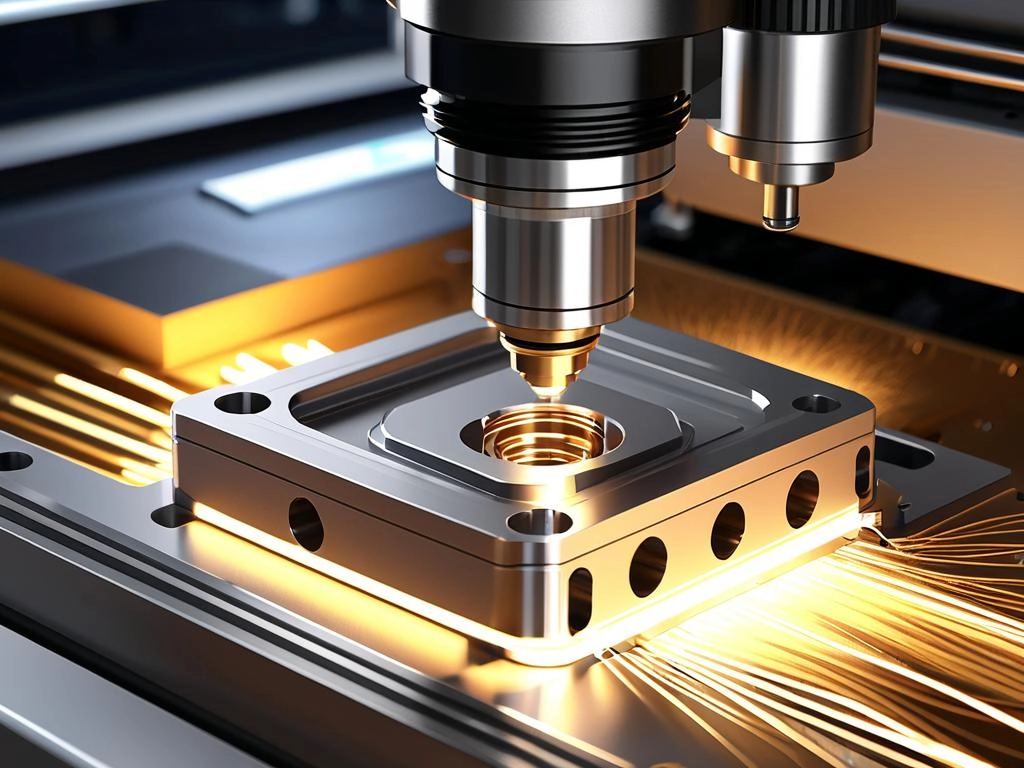
Introduction to New Energy CNC Milling
The Significance of New Energy CNC Milling
New Energy CNC Milling represents a revolutionary approach in the manufacturing industry. It combines the precision and efficiency of Computer Numerical Control (CNC) technology with the focus on sustainable and clean energy sources. This not only reduces the environmental impact but also offers enhanced performance and cost-effectiveness. For example, in the production of complex components for the renewable energy sector, New Energy CNC Milling can ensure high accuracy and repeatability, meeting the strict quality standards required.
Applications of New Energy CNC Milling
The applications of New Energy CNC Milling are vast and diverse. It is widely used in industries such as aerospace, automotive, and medical device manufacturing. In the aerospace industry, it is used to fabricate intricate parts for aircraft engines and airframes. In the automotive sector, it helps in producing high-precision components for electric vehicles, contributing to their efficiency and reliability. In medical device manufacturing, New Energy CNC Milling enables the creation of precise and customized implants and surgical instruments.
Advantages Over Traditional Milling Methods
Compared to traditional milling methods, New Energy CNC Milling offers several advantages. Firstly, it provides higher precision, allowing for the production of components with tighter tolerances. This is crucial in industries where even the slightest deviation can lead to significant performance issues. Secondly, it is more energy-efficient, reducing operational costs and carbon emissions. Additionally, the automated nature of CNC milling reduces the risk of human error, ensuring consistent quality and productivity.
The Role of Transistor Socket in CNC Milling
Understanding Transistor Sockets
Transistor sockets play a vital role in the operation of CNC milling machines. They provide a secure and reliable connection for transistors, which are essential components for controlling the electrical signals and power supply within the machine. A well-designed transistor socket ensures proper heat dissipation, preventing overheating and extending the lifespan of the transistors. It also allows for easy replacement and maintenance of transistors, reducing downtime and improving the overall efficiency of the milling process.
Enhancing Performance with Transistor Sockets
By using high-quality transistor sockets, the performance of New Energy CNC Milling machines can be significantly enhanced. The sockets help in maintaining stable electrical connections, minimizing signal interference and ensuring accurate control of the milling tools. This results in improved surface finish and dimensional accuracy of the machined parts. Moreover, transistor sockets with advanced features such as better insulation and shielding can protect the sensitive electronic components from external electromagnetic interference, further enhancing the reliability of the machine.
Compatibility and Customization of Transistor Sockets
It is important to ensure the compatibility of transistor sockets with the specific requirements of the CNC milling machine. Different machines may have different power and signal requirements, and the transistor sockets need to be selected accordingly. Additionally, customization options are available to meet the unique needs of certain applications. For example, in high-power CNC milling operations, sockets with higher current-carrying capacity can be designed to handle the increased electrical load.
Optimization of Machining Area Lighting
Importance of Adequate Lighting
Proper lighting in the machining area is crucial for the safety and efficiency of the CNC milling process. Adequate illumination allows operators to clearly see the workpiece, cutting tools, and machine components, reducing the risk of accidents and errors. It also helps in detecting any defects or irregularities in the machined parts at an early stage, enabling timely corrective actions. In addition, good lighting conditions can improve the working environment, reducing eye strain and fatigue among operators.
Types of Lighting Solutions
There are various types of lighting solutions available for optimizing the machining area lighting. LED lights are a popular choice due to their high energy efficiency, long lifespan, and excellent color rendering properties. They can provide bright and uniform illumination, ensuring clear visibility of the work area. Fluorescent lights are another option, offering good light output and relatively low cost. However, they may have limitations in terms of color temperature and lifespan. Additionally, some machining areas may require specialized lighting such as spotlights or task lights for specific operations that require focused illumination.
Design Considerations for Lighting Optimization
When optimizing the machining area lighting, several design considerations need to be taken into account. The layout of the lights should be carefully planned to ensure uniform coverage of the work area, avoiding shadows and glare. The color temperature of the lights should be appropriate for the task, with a balance between cool white and warm white to provide a comfortable visual environment. The intensity of the lighting can be adjusted according to the specific requirements of the milling operation, such as higher intensity for detailed work and lower intensity for general monitoring.
Conclusion and Future Outlook
Summary of Key Points
In summary, New Energy CNC Milling, along with the proper use of transistor sockets and optimization of machining area lighting, offers significant benefits in terms of precision, efficiency, and safety. The combination of these elements can enhance the performance of CNC milling machines and improve the quality of machined parts. Transistor sockets provide reliable electrical connections and contribute to the overall reliability of the machine, while optimized lighting ensures a clear and safe working environment for operators.
Potential for Further Development
Looking ahead, there is still room for further development and improvement in these areas. Research and development efforts can focus on advancing the technology of New Energy CNC Milling to achieve even higher precision and productivity. The design and materials of transistor sockets can be continuously optimized to meet the increasing demands of modern manufacturing. In terms of lighting, the development of more intelligent lighting systems that can automatically adjust the intensity and color temperature based on the machining conditions will further enhance the user experience and operational efficiency.
Call to Action
Manufacturers and operators in the CNC milling industry should recognize the importance of these factors and invest in the latest technologies and solutions. By embracing New Energy CNC Milling, using high-quality transistor sockets, and optimizing machining area lighting, they can stay competitive in the market and achieve better results in their production processes. It is time to take action and unlock the full potential of CNC milling for a more sustainable and efficient future.