Unveiling the Wonders of CNC Plastic Machining and 3D Printing Parts: Exploring CNC Tool Life
Introduction to CNC Plastic Machining
CNC plastic machining has revolutionized the manufacturing industry. It offers a precise and efficient way to transform plastic materials into intricate components. The process involves using computer numerical control (CNC) machines to cut, shape, and finish plastic parts with a high degree of accuracy. This technology has become a staple in various sectors, from automotive to aerospace, due to its ability to produce parts with tight tolerances and complex geometries.
The Basics of CNC Plastic Machining
At its core, CNC plastic machining starts with a digital design model. This model is then translated into machine-readable code that guides the CNC machine's movements. The machine uses a variety of cutting tools, such as end mills and drills, to remove material from the plastic workpiece. The choice of tool depends on factors like the type of plastic, the desired surface finish, and the complexity of the part.
Materials Used in CNC Plastic Machining
A wide range of plastic materials can be machined using CNC technology. Some common ones include acrylonitrile butadiene styrene (ABS), polycarbonate, polyethylene, and polystyrene. Each material has its own unique properties, such as strength, flexibility, and heat resistance. This allows manufacturers to select the most suitable plastic for a specific application. For example, polycarbonate is often chosen for applications that require high impact resistance, while polyethylene is favored for its chemical resistance.
Advantages of CNC Plastic Machining
One of the major advantages of CNC plastic machining is its precision. It can achieve tolerances as tight as a few thousandths of an inch, ensuring that parts fit together perfectly. Additionally, the process is highly repeatable, meaning that multiple parts can be produced with consistent quality. CNC plastic machining also offers flexibility in terms of design. Complex shapes and features can be easily incorporated into the parts, giving designers more freedom to create innovative products.
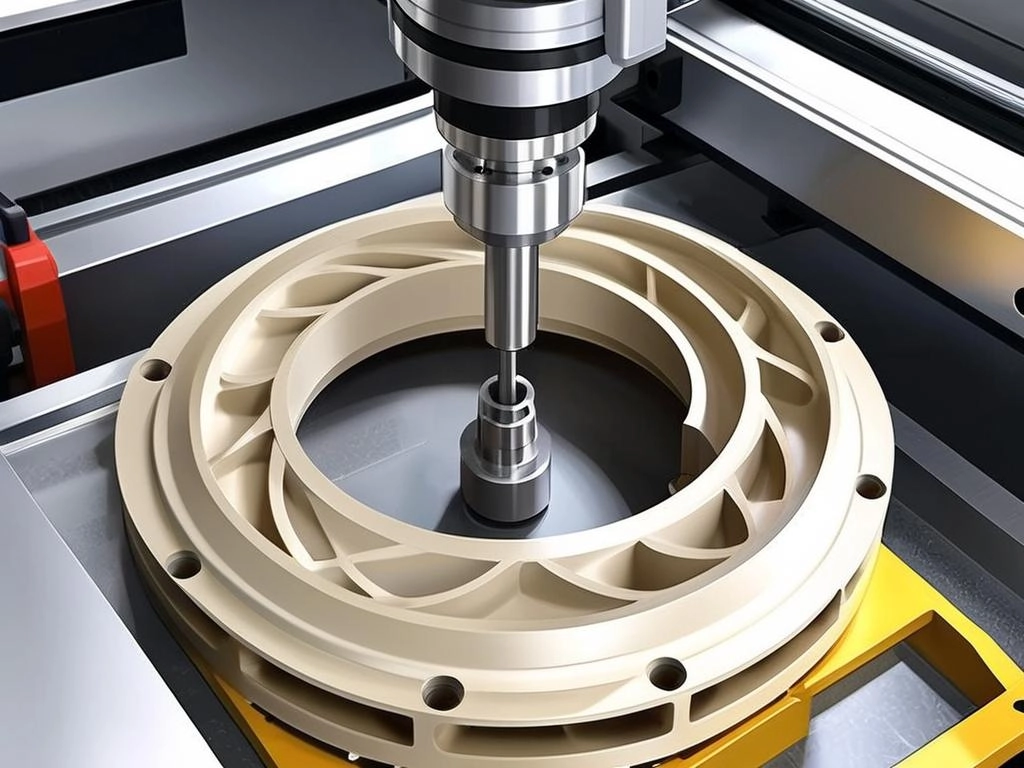
3D Printing Parts: A New Era of Manufacturing
3D printing has emerged as a game-changer in the manufacturing landscape. It allows for the creation of three-dimensional objects by depositing layers of material based on a digital model. This additive manufacturing process has several advantages over traditional manufacturing methods, especially when it comes to producing complex and customized parts.
The 3D Printing Process
The 3D printing process begins with a 3D model created using computer-aided design (CAD) software. The model is then sliced into thin layers, and the 3D printer deposits material layer by layer to build up the object. Different types of 3D printers use various materials, including plastics, metals, ceramics, and even biological materials. For plastic 3D printing, common materials include PLA (polylactic acid), ABS, and PETG.
Benefits of 3D Printing Parts
One of the key benefits of 3D printing parts is the ability to create complex geometries with ease. Traditional manufacturing methods often face limitations when it comes to producing parts with internal structures or organic shapes. 3D printing allows for the creation of these intricate designs without the need for expensive tooling or complex machining operations. Another advantage is the ability to customize parts quickly and cost-effectively. This makes it ideal for small batch production and rapid prototyping.
Limitations of 3D Printing Parts
While 3D printing offers many advantages, it also has some limitations. One of the main drawbacks is the relatively slow production speed compared to CNC machining, especially for large-scale production. The surface finish of 3D printed parts may also not be as smooth as that of machined parts, requiring additional post-processing in some cases. Additionally, the mechanical properties of 3D printed plastics may be different from those of machined plastics, depending on the printing process and material used.
Understanding CNC Tool Life
CNC tool life is a crucial factor in the success of CNC plastic machining. It refers to the amount of time or the number of parts a cutting tool can be used before it needs to be replaced. Understanding and managing tool life is essential for maintaining productivity, quality, and cost-effectiveness in the machining process.
Factors Affecting CNC Tool Life
Several factors can influence the life of a CNC cutting tool. The type of plastic material being machined is a significant factor. Some plastics may be more abrasive than others, causing the tool to wear out faster. The cutting parameters, such as cutting speed, feed rate, and depth of cut, also play a crucial role. High cutting speeds and feeds can increase tool wear, while a proper combination of these parameters can extend tool life. The quality and geometry of the cutting tool itself are also important. Tools with sharp edges and the right shape for the machining operation tend to last longer.
Tool Wear Mechanisms
There are several types of tool wear mechanisms that can occur during CNC plastic machining. Abrasive wear is one of the most common, where hard particles in the plastic material rub against the tool surface, gradually wearing it down. Adhesive wear can also happen when the plastic material sticks to the tool, causing parts of the tool to be pulled away. Diffusion wear occurs at high temperatures, where atoms from the tool and the plastic material diffuse into each other, weakening the tool. Understanding these wear mechanisms can help in selecting the right tools and optimizing machining parameters.
Tool Life Prediction and Management
Manufacturers use various methods to predict and manage CNC tool life. One approach is to monitor the tool's performance during machining. This can be done through sensors that measure parameters such as cutting force, vibration, and temperature. By analyzing these data, manufacturers can detect early signs of tool wear and schedule tool changes before it affects the quality of the parts. Another method is to use tool life models based on empirical data. These models take into account factors like cutting parameters and material properties to estimate the tool life and help in planning tool replacements.
Comparing CNC Plastic Machining and 3D Printing Parts
When it comes to choosing between CNC plastic machining and 3D printing parts, several factors need to be considered. Each process has its own strengths and weaknesses, and the decision depends on the specific requirements of the project.
Quality and Precision
CNC plastic machining generally offers higher precision and better surface finish compared to 3D printing. It can achieve tighter tolerances, making it ideal for applications where accuracy is crucial. However, 3D printing has made significant advancements in recent years, and with proper post-processing, it can also produce parts with acceptable precision and quality.
Production Speed
For large-scale production, CNC plastic machining is often faster than 3D printing. CNC machines can operate continuously and produce parts at a relatively high rate. On the other hand, 3D printing is more suitable for small batch production and rapid prototyping, where the ability to quickly produce a few parts is more important than high-speed production.
Cost Considerations
The cost of CNC plastic machining includes the cost of the machine, tools, labor, and material. Tooling costs can be significant, especially for complex parts. 3D printing, on the other hand, has lower upfront costs as it does not require expensive tooling. However, the cost of 3D printing materials can be relatively high, and the production time may also impact the overall cost, especially for large quantities.
Applications of CNC Plastic Machining and 3D Printing Parts
Both CNC plastic machining and 3D printing parts find extensive applications in various industries.
Automotive Industry
In the automotive industry, CNC plastic machining is used to produce components such as engine parts, interior trim pieces, and custom fixtures. 3D printing is also increasingly being used for rapid prototyping of new designs, as well as for producing low-volume, customized parts like automotive accessories.
Aerospace Industry
The aerospace industry demands high-precision parts with excellent mechanical properties. CNC plastic machining is used to manufacture components like aircraft interiors, ducting systems, and structural parts. 3D printing is being explored for producing complex parts with lightweight structures, which can help reduce the weight of aircraft and improve fuel efficiency.
Medical Industry
In the medical field, both technologies play important roles. CNC plastic machining is used to produce medical devices with tight tolerances, such as surgical instruments. 3D printing is used for customizing medical implants, as it allows for the creation of patient-specific designs. It can also be used for producing anatomical models for surgical planning.
Final Thoughts
CNC plastic machining and 3D printing parts are two powerful manufacturing technologies that offer unique advantages. CNC plastic machining provides precision, speed, and high-quality parts for a wide range of applications, while 3D printing offers the flexibility to create complex and customized designs. Understanding CNC tool life is essential for optimizing the CNC machining process. By carefully considering the requirements of each project, manufacturers can choose the most suitable technology to meet their needs and drive innovation in the manufacturing industry.