Unraveling the Mysteries of CNC Prototyping: How to Find the Right Path and Overcome Connector Pin Inaccurate Calibration
Introduction to CNC Prototyping
CNC (Computer Numerical Control) prototyping has revolutionized the manufacturing industry. It allows for the rapid creation of physical models from digital designs. This process is not only efficient but also highly accurate, enabling manufacturers to test and refine their products before mass production. The ability to quickly produce prototypes using CNC machines has significantly reduced development time and costs.
Finding the right CNC prototyping service or mastering the in - house CNC prototyping process is crucial for businesses across various sectors. Whether it's in automotive, aerospace, electronics, or consumer goods, CNC prototyping plays a vital role in bringing innovative ideas to life.
The Significance of CNC Prototyping in Product Development
CNC prototyping serves as a bridge between concept and production. It provides an opportunity to visualize the final product, check for design flaws, and test functionality. For example, in the automotive industry, engineers can create prototypes of new engine components to test their performance under different conditions. This helps in making necessary design adjustments early in the development cycle, saving both time and resources.
In the electronics field, CNC prototyping allows for the creation of custom enclosures and circuit board prototypes. This enables designers to ensure proper fit and functionality of components before mass - producing electronic devices.
Types of CNC Prototyping
There are several types of CNC prototyping techniques. One of the most common is CNC machining, which involves using subtractive manufacturing processes such as milling, turning, and drilling. This method is suitable for creating complex shapes and high - precision parts. Another type is CNC 3D printing, which builds parts layer by layer, offering more design freedom and the ability to create intricate geometries.
CNC routing is also popular, especially for working with materials like wood, plastic, and foam. It is often used for creating prototypes of signs, fixtures, and decorative elements.
How to Find CNC Prototyping Services
When looking for CNC prototyping services, there are several factors to consider. The first step is to define your requirements clearly. Determine the type of prototype you need, the materials to be used, and the level of precision required.
One of the best ways to find reliable CNC prototyping services is through referrals. Ask colleagues, industry peers, or business partners if they have worked with any good prototyping companies. Online reviews and testimonials can also provide valuable insights into the quality of service and customer satisfaction of different providers.
Evaluating CNC Prototyping Companies
Once you have a list of potential CNC prototyping companies, it's time to evaluate them. Look at their experience in the industry. A company with a long - standing reputation is more likely to have the expertise and skills to handle your project. Check their portfolio to see the range of prototypes they have created in the past. This will give you an idea of their capabilities and the quality of their work.
Another important aspect is the equipment they use. Modern and well - maintained CNC machines are essential for producing high - quality prototypes. Inquire about their quality control processes. A reliable company will have strict quality checks in place to ensure that the prototypes meet the required specifications.
Cost Considerations
Cost is always a significant factor when choosing a CNC prototyping service. However, it should not be the sole determining factor. Cheaper services may not necessarily offer the same level of quality. Get quotes from multiple providers and compare them. Look for a company that offers a fair price without compromising on quality.
Some companies may offer package deals or discounts for larger projects. It's also important to understand what is included in the price, such as design assistance, material costs, and finishing options.
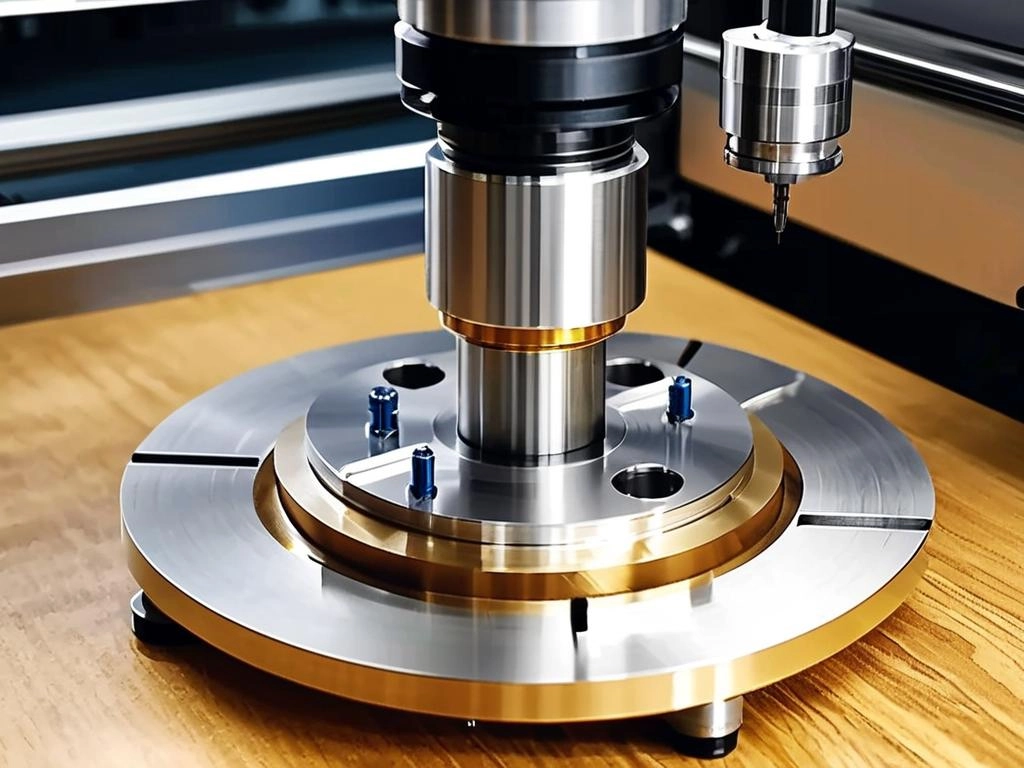
The Problem of Connector Pin Inaccurate Calibration
Connector pins are crucial components in many electronic and mechanical systems. They are used to establish electrical connections or provide mechanical support. However, inaccurate calibration of connector pins can lead to a host of problems.
Inaccurate calibration can result in poor electrical conductivity. This can cause signal loss, interference, or even complete failure of the electronic device. In mechanical applications, misaligned connector pins can lead to improper fitting of components, affecting the overall functionality and durability of the product.
Causes of Inaccurate Calibration
One of the main causes of inaccurate calibration of connector pins is human error. During the manufacturing or assembly process, if the operator fails to follow the correct calibration procedures, it can lead to misaligned pins. Another cause is worn - out or malfunctioning equipment. CNC machines that are not properly maintained or calibrated can produce connector pins with inaccurate dimensions.
Environmental factors can also play a role. Temperature and humidity changes can affect the materials used in connector pins, causing them to expand or contract and leading to calibration issues.
Impact on Product Performance
The impact of inaccurate connector pin calibration on product performance can be severe. In electronic devices, it can lead to intermittent faults, reduced battery life, or even damage to other components. For example, in a smartphone, inaccurate connector pins for the battery can cause the phone to shut down unexpectedly or have a shorter battery charge time.
In mechanical products, such as automotive engines, misaligned connector pins can cause vibrations, increased wear and tear, and reduced efficiency. This can ultimately lead to costly repairs and product recalls.
Solutions to Connector Pin Inaccurate Calibration
To address the issue of inaccurate connector pin calibration, several measures can be taken. First and foremost, training and education are essential. Operators should be well - trained on the proper calibration procedures and the importance of accuracy. Regular refresher courses can help keep them updated on the latest techniques.
Investing in high - quality equipment and maintaining it properly is also crucial. CNC machines should be regularly calibrated and serviced to ensure they are operating within the required tolerances. Using advanced measurement tools can help detect and correct calibration issues early.
Quality Control Measures
Implementing strict quality control measures is vital. This includes conducting thorough inspections at various stages of the manufacturing process. Sampling and testing of connector pins can help identify any calibration problems before they reach the final product.
Using statistical process control (SPC) techniques can also be beneficial. SPC allows for the monitoring of the manufacturing process in real - time, enabling quick identification and correction of any trends towards inaccurate calibration.
Design Improvements
Design improvements can also help mitigate the effects of inaccurate connector pin calibration. For example, designing connector pins with self - aligning features can reduce the impact of minor calibration errors. Using materials with stable properties under different environmental conditions can also improve the reliability of the connector pins.
Final Thoughts
Finding the right CNC prototyping solution is essential for successful product development. It offers numerous benefits in terms of speed, accuracy, and cost - effectiveness. At the same time, addressing the issue of connector pin inaccurate calibration is crucial to ensure the performance and reliability of the final product.
By following the guidelines for finding CNC prototyping services, evaluating providers, and implementing solutions to calibration problems, businesses can enhance their product development processes and bring high - quality products to the market.
As the manufacturing industry continues to evolve, staying updated on the latest trends and technologies in CNC prototyping and calibration will be key to maintaining a competitive edge. Whether it's through continuous learning, investing in new equipment, or collaborating with industry experts, the goal should be to produce prototypes and final products that meet or exceed customer expectations.