0.02mm! Luoyang's Copper Processing Industry Adds "world's First"
In the 1930s, the copper foil industry emerged in the United States and was widely used in electronic circuits and other fields. For nearly a century, it has been "unparalleled."
In 2024, a company in Luoyang will use disruptive technology to upgrade and improve, bringing a more economical and lighter alternative to traditional copper foil, with broad prospects.
Yesterday, at Luoyang Copper Metal Materials Development Co., Ltd. in Mengjin District Advanced Manufacturing Development Zone, a roll of carrier copper foil 1 meter wide and 0.02 mm thick was slowly rolled up and was about to be sent to a well-known domestic company. Leading photovoltaic company. As a new type of copper-aluminum composite foil, this is the first time in the world that batch industrial application of carrier copper foil has been achieved, and it is expected to replace traditional copper foil and become the mainstream technology route.
Behind this is the company's innovative practice of the world's first oxygen-free semi-molten rolling composite technology through more than ten years of "innovation journey", which reflects the pioneering spirit and strength of Luoyang's copper processing industry.
Copper-aluminum composite has the advantages of “having both your cake and eat it too”>
The mill hums as the foil moves in and out.
A few days ago, I walked into the production site of Luotongyi Company, which has an annual output of 20,000 tons of metal composite materials and circuit boards for new energy vehicles. The second phase of the project has just been put into operation and has entered full production.
"Orders are in short supply." Liu Li, the person in charge of the project, said excitedly: "Compared with traditional pure copper foil materials, its performance is better and the price is cheaper. Customers are rushing to 'try' it!"
From photovoltaic power generation panels, to new energy batteries, to electronic products such as mobile phones and computers, copper foil is inseparable from the conductive material of their circuit boards. Copper foil is therefore known as the "blood vessel" and "nerve" of electronic circuits. Now, with the introduction of "Luoyang Innovation" carrier copper foil to the market, the pure copper foil that has been "popular" for nearly a hundred years has ushered in a new "replacement" - carrier copper foil.
"Although the name is still copper foil, it is actually a copper-aluminum composite foil." Wang Xiang, the company's chief engineer, said that compared with traditional pure copper foil, one side of the carrier copper foil is copper with excellent conductivity and corrosion resistance. One side is low temperature copper foil. The low cost and low density of aluminum not only retain the excellent conductivity and corrosion resistance of aluminum foil, but also reduce the weight by about 60% to 75% and the cost by 50% to 55% compared with traditional copper foil.
"This means that wherever there are circuits, such as copper substrates, flexible circuit boards, busbars, etc., they can replace traditional copper foil. It is reflected in terminals, making photovoltaic panels, mobile phones, computers, electric vehicles, lighting The equipment is lighter, cheaper and more reliable," Wang Xiang said.
The birth of “the world’s first” and the formulation of national standards>
At the entrance of the R&D room, a wastebasket filled with copper-aluminum composite foil witnesses the arduous process of R&D.
"Copper and aluminum are basically two metals that are firmly attached to each other and cost controllable. They were not favored by the industry at the beginning. We only tested more than a thousand tons of scrap copper and aluminum plates and foils!" It was more than ten years ago. Something happened! Wang Xiang still remembers when he first came into contact with copper-aluminum composite technology.
This R&D work began with the relatively difficult production of copper-aluminum composite panels. At that time, the copper-aluminum composite technology required friction welding equipment imported from abroad. Not only was it limited by manpower, but the technical route was also inefficient and costly, making it difficult to promote industrialization.
"The imported equipment sells for 2 million yuan each, and there is no possibility of counter-offering." Wang Xiang said, "We are determined to develop domestic processes suitable for industrial promotion to meet domestic demand for new materials."
But without reference parameters and successful precedents, research and development is like "raising a high building from the ground." At the beginning, the company's R&D personnel collectively discussed it for three days and three nights, but during the trial production process, the "two layers of skin" of copper and aluminum could be torn as soon as they came off the production line. unarmed.
In order to avoid detours, the company has introduced a team of academician Zhang Guocheng, an academician of the Chinese Academy of Engineering and one of the leaders in rare earth material metallurgy in my country, and has invested a total of nearly 100 million yuan in research and development funds. Eventually, oxygen-free semi-molten rolling composite technology gradually became clear.
Using this low-cost process, the company pioneered the world's first oxygen-free semi-molten rolling composite technology to achieve a high-strength metallurgical bond between copper and aluminum. Not only did it produce a 1-meter-wide copper-aluminum composite strip for the first time in the world, but it also took the lead in formulating my country's first national standard for copper-aluminum composite panels and strips. During the technical appraisal and other activities, Ding Wenjiang, academician of the Chinese Academy of Engineering, said it was "eye-opening", and academician Zhang Guocheng commented that it "filled the gap at home and abroad"!
From "board" to "foil", become the "hidden champion">
"The development of plates has been successful, but what is more difficult is thin copper-aluminum composite foil." Wang Xiang said.
The successful research and development of copper-aluminum composite panels has enabled the company's products to be widely supplied to well-known new energy vehicle companies such as BYD and Tesla. Over the years, the company has supplied billions of copper-aluminum composite connecting sheets for new energy power batteries, but it has always maintained industry records of "zero heat generation" and "zero shedding".
On this basis, the company has vigorously promoted the research and development of carrier copper foil with thinner thickness and more complex process since last year. The surface thickness tolerance reaches less than 2 microns, which is only 1/30 of the diameter of copper foil. A human hair. Moreover, even when folded in half, the copper-aluminum bonding layer remains strong. At present, the company's copper-aluminum composite new material plate, strip and foil market share ranks first in the industry, and sales revenue jumped from 160 million yuan in 2020 to about 900 million yuan last year, achieving "explosive growth."
In the 1950s, marked by the launch of Luoyang Copper Industry during the "First Five-Year Plan" period, Luoyang became an important copper processing and production base in the country. Today, the strength of Luoyang's copper processing industry remains the same. In addition to long-established enterprises such as Luotong, "professional, special and innovative" private enterprises such as Luotong No. 1 Company also assume a leading role in industrial innovation.
"Whenever I think back to the glory of Luoyang's copper processing industry, I always have a sense of mission." Wang Xiang said from the bottom of his heart that in the future, the company will increase the research and development of high value-added products and promote products from "single zero foil" to "Double Zero Foil" transforms and upgrades CNC milling, and uses it to create more original and disruptive "Luoyang Innovations" to contribute to the country's promotion of innovative development of the new material industry and accelerate the formation of new high-quality productivity.
Luobao Media·Pocket Luoyang Client Reporter Zhang Ruixin Correspondent Chen Lijunwen/Photo
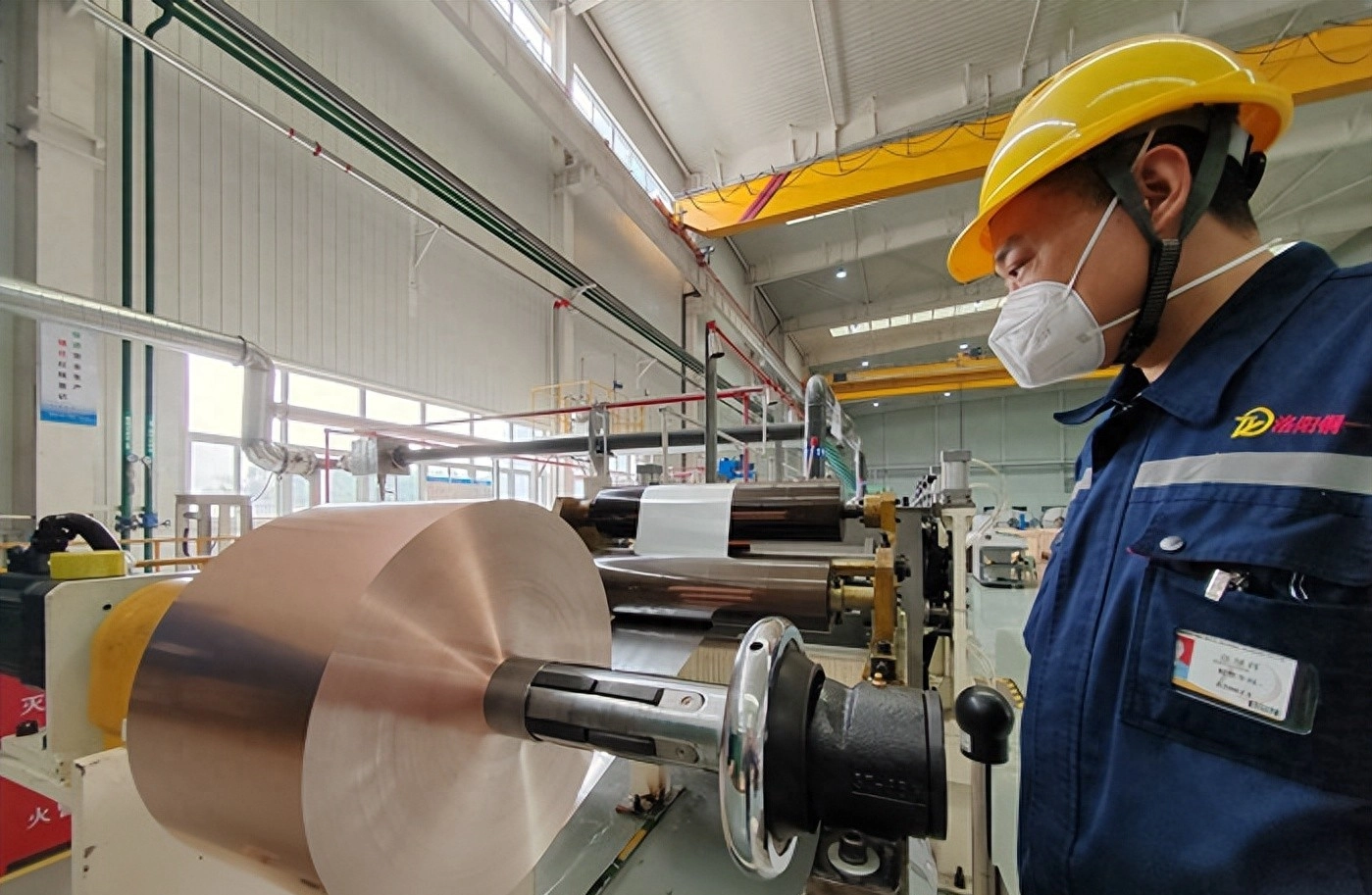