Traditional Aluminum Processing Enterprises Embark On The Road Of Digitalization And Intelligence
Science and Technology Daily reporter Zhu Hong Li Liyun correspondent Li Jingyi
In the production plant of Northeast Light Alloy Co., Ltd., workers are controlling a crane to transport aluminum coils. Photo by Xinhua News Agency reporter Xie Jianfei
Intelligent production organization, networked tracking of in-process products, automated robot operations, accurate risk warning... Enter Northeast Light Alloy Co., Ltd. (hereinafter referred to as Dongqing), which enjoys the reputation of "Light Alloy Silver Pillar" "Motherland" CNC items, reporter The first impression of the visit is that it has a "full sense of technology".
During the "14th Five-Year Plan" period, Dongqing regards digital transformation as a key source of power for the high-quality development of high-end manufacturing, seizes the opportunity of information reform, and strives to promote the comprehensive integration of new and old driving forces. Elements of intelligent manufacturing and traditional aluminum processing industry chains. In the process of "Holding Faith", we will further promote the transformation and upgrading of enterprises and support the construction of new industrialization.
Create a smoothly connected digital workshop>
"Intelligent manufacturing promotes the reshaping and reengineering of production organizations." said Qi Yan, deputy director of Dongqing Medium and Thick Plate Factory.
The plate factory where Qiyan is located is at the forefront of creating high-precision aluminum products in my country. Here, from the moment the aluminum alloy ingot enters the first rolling process, its production progress, process requirements, work report materials and other relevant information have been uploaded to the digital intelligent network platform. The intelligent system records the status of the work-in-progress in real time, realizing paperless tracking of the entire process, and "no information is landed".
"The use of new technologies makes the production process control of Dongqing products more precise and efficient." Qi Yan said: "With the help of the information system, every material on the production line is given a unique identity code, which can be obtained by scanning the code. Obtain corresponding information. From the initial input to packaging acceptance, the accuracy of on-site management has been directly positioned from the original "certain batch" to the specific "certain one", stimulating the smooth connection of the upstream and downstream production systems. overall efficiency.”
The purchase, sales and inventory system places orders, the manufacturing execution system (MES) schedules manufacturing, the quality inspection system strictly controls, and the energy management system assists production... As the digital and intelligent layout becomes more and more perfect, Dongqing is gradually establishing an efficient and interconnected "digital workshop". Next to key parts such as the plate re-shearing machine and the casting dispatch room, various data collected from the MES and equipment intelligent monitoring platform are updated and jumped on the comprehensive electronic control screen, bringing clearer and more intuitive work guidance to the site. On-site personnel, combined with smart tools such as robots and unmanned refining vehicles, completely bridge the "last mile" of online planning and execution. Since the intelligent transformation, Dongqing’s overall production capacity, especially the output of high-end products, has repeatedly hit record highs. The working efficiency of some production lines has increased by nearly 30%, and the ability to support key materials in key areas has been significantly improved.
Build a safe and efficient digital intelligent ecosystem>
In the first half of 2024, Dongqing Digital Intelligent Ingot Processing Park will be officially completed. On the aluminum alloy small and medium diameter round ingot production line in the park, robots with size and shape recognition capabilities can complete loading, filling, processing, unloading and palletizing in a short time through fully automatic positioning and grabbing without manual intervention. The whole process. Wang Xiaorui, leader of the equipment support team of Dongqing Foundry, said that before the intelligent transformation, all processes of the production line required manual participation, which was inefficient and involved high-intensity repetitive labor. "Robot operations not only ensure production progress and improve work quality, but also effectively alleviate the pressure on manpower allocation. After the separation of humans and machines, the intrinsic safety of the site has also been significantly improved."
In the new era, Dongqing focuses on safety and efficiency, and is building all elements of the digital intelligent ecosystem, integrating automation and intelligent tools and methods into the "nerve endings" of production and operations. In Dongguan's largest main body plate and strip factory, intelligent inspection equipment connected to the manufacturing system is distributed in "key parts" of each work area. Once an abnormality is detected, an alert is issued immediately. Since the device was put into use for 5 years, the factory has continuously achieved "zero accidents". This device effectively maintains production safety and stability and provides support for Dongqing's risk management and control model to transform from post-event response to early warning.
At Harbin Dongqing Special Materials Co., Ltd., regional engineer Zhu Chaodong demonstrated the LDC lean digital cloud platform on his mobile phone. The reporter saw through the display interface that once on-site risk points such as channel fragments and pollution source leakage are submitted, the system background will automatically analyze the problem and associate the person responsible, and immediately generate a clear task description and clear task instructions. Processing time limits. The work list requires the responsible person to implement rectifications according to the time points. "Now this portable App allows us to check for leaks and fill vacancies anytime and anywhere and perform our duties. It has become an essential tool for our front-line employees to carry out their daily work. This not only enriches Dongqing Digital's intelligent application scenarios, but also makes basic management and lean The production concept is more deeply rooted in people's hearts," said Zhu Chaodong.
Enter the future factory of intelligent manufacturing>
2024 is the peak year for Dongqing project construction, and it is also a key year for Dongqing to consolidate the development of "digital base" and enter the "future factory" of intelligent manufacturing.
As the "intelligent core" of manufacturing enterprises, MES and full production line coverage have always been an important task for Dongqing's digital intelligent transformation. In 2024, the second phase of Dongqing MES project is taking root at Dongqing Plate and Strip Factory and Harbin Dongqing Special Materials Co., Ltd. "The project is expected to be completed before the end of November. By then, MES will give full play to its core functions in aluminum alloy rolling, extrusion, forging and other aspects, and will be linked with existing warehouse spare parts management systems, quality online inspection systems and other intelligent tools , producing a growth effect of 1+1>2. Li Qiang, chief engineer of Dongqing Company’s Operations Management Department, told reporters: “We will focus on transforming the old production methods of aluminum alloys and continue to expand the manufacturing of the company’s strategic support products and competitive advantage products. ability. "
Adhering to demonstration leadership and key research, starting this year, Dongqing will join hands with Chinalco Group High-end Manufacturing Co., Ltd. to launch the "intelligent chemical factory" benchmark construction project at the Dongqing Medium and Thick Plate Factory. During the project advancement process, Dongqing actively linked with the new generation industrial Internet big data platform to conduct detailed planning and piloting of intelligent technologies such as automated information collection, homogeneous centralized control, AGV unmanned logistics, etc., striving to achieve more advanced and advanced intelligent technologies. manufacturing technology. Operate efficiently. This development model seizes the opportunities of the new round of industrial revolution and realizes the rediscovery and redevelopment of its own high-end aluminum alloy manufacturing capabilities.
"Intelligent manufacturing is of great significance to building a 'Century Dongqing' with lasting vitality, strategic contribution, and social influence. We will base ourselves on the present and plan for the long term, and truly implement the digital and intelligent upgrading and transformation work." Transformation and optimization Strengthen CNC center, promote the improvement of quality and efficiency of traditional aluminum processing manufacturing industry, and accumulate momentum for accelerating the construction of the world's leading light alloy processing enterprise. "General Manager and Deputy Secretary of the Party Committee Zhang Rongwang said that the smart manufacturing leader group.
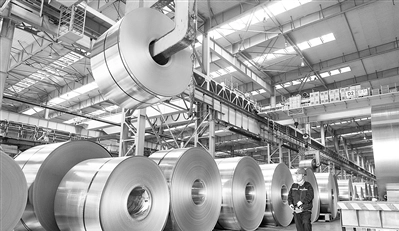