Knowledge Sharing | Overview Of Titanium And Titanium Alloy Processing Technology
China's titanium industry started in the 1960s. After more than 60 years of development, a relatively complete titanium industry system with national characteristics has been formed. Over the years, through continuous production line transformation and continuous improvement of process technology level, the gap between my country's titanium processing technology level and the world's advanced level has become smaller and smaller.
Especially in the past ten years, my country's titanium processing technology has made great progress and the quality level has been continuously improved by further strengthening the technological transformation of titanium processing equipment, technological innovation in processing technology, research and development of new products, and implementation of industrial demonstration projects. Some products have reached the international advanced level.
Titanium and titanium alloy processing technology
Titanium and titanium alloys are titanium ingots that are melted and cast from titanium sponge or titanium sponge plus alloying elements, and then processed into materials (plates, strips, tubes, rods, wires) through plastic processing methods such as forging and rolling. extrusion. , profiles and forgings, etc.), through processing, titanium metal is not only prepared into the required shape, but also improves the structure and performance. Parts of various shapes can also be manufactured by casting, powder metallurgy and other methods.
The main features of titanium and titanium alloy processing
Titanium and titanium alloys are highly chemically active
Titanium and titanium alloys are prone to violent reactions with oxygen-containing gases such as oxygen and nitrogen at high temperatures. When heated in air, oxide scale will form on the surface of the steel billet. When the temperature is higher than 900°C, scale begins to form. In addition, when oxygen and nitrogen diffuse deep into the metal, a surface getter layer is formed, which increases the hardness and reduces the plasticity.
In order to eliminate the impact of the getter layer on subsequent pressure processing and final use performance, the intermediate blank and finished product should be surface treated using physical or chemical methods. Commonly used methods are: 1. Use protective coating for protection, which can more effectively prevent the metal from absorbing air during reheating, deformation and cooling. 2. Heat the blank under a protective atmosphere to prevent air absorption. 3. Induction heating and contact heating are more reasonable heating methods, which can greatly shorten the residence time of metal in the violent oxidation temperature range.
Titanium and titanium alloys have poor thermal conductivity
The thermal conductivity of titanium and titanium alloys is usually only 1/15 of that of aluminum and aluminum alloys, and 1/5 of that of steel. The low thermal conductivity causes a large temperature difference along the cross-section of the ingot and billet when titanium is heated, resulting in large thermal stress, and in severe cases, cracks will form. This requires limiting the heating rate, especially the heating rate of steel ingots and large-size billets.
In the hot processing of titanium and titanium alloy billets, large temperature differences may also occur as the billets cool. The sharp edges and thin sections of the blank cool rapidly, making it difficult to ensure uniform deformation and subsequent further deformation, resulting in metal cracking.
This characteristic of titanium alloy fundamentally limits the shape that can be processed by the intermediate blank and finished section, the deformation method of the blank, the deformation feed speed, and the selection range of deformation equipment.
The poor thermal conductivity of titanium alloy also affects its own thermal deformation process. The thermal effect of deformation can easily overheat the metal in the strongest deformation zone, leading to deterioration of the structure and properties. This phenomenon is particularly likely to occur when billet forging (upsetting), bar profile rolling, profile extrusion and other processes are not performed properly. Only by rationally selecting metal deformation heating temperature, deformation rate, deformation speed, etc. can bad tissue areas be avoided.
Polycrystalline transformation of alpha and beta phases
Except for alloys with stable β phase, pure titanium and most titanium alloys will transform into a single-phase β phase state when heated to a certain temperature. The complete α+β→β phase transition temperature of most industrial titanium alloys is between 850 and 1020°C, which is related to the alloy composition and impurity content.
Heating to the β zone temperature can significantly increase plasticity and reduce deformation ability. However, the β-region deformation is not conducive to obtaining a good performance structure. A better structure can only be obtained when deforming in the α+β phase zone, but the plasticity of the metal, especially the plasticity in the casting state, is much lower in the temperature range of the two-phase zone, and the deformation resistance is also reduced. also increased dramatically.
In actual production, this problem can be solved if the deformation is carried out in two stages, that is, the ingot is first deformed in the β phase zone and then in the α+β phase zone. The deformation rates of these two stages should be selected based on the total metal deformation rate required for processing. The minimum deformation rate in the β region depends on whether a fine-grained macrostructure needs to be ensured, while the minimum deformation rate of α+β determines whether a better microstructure can be obtained. Depending on the type of product being processed, different deformation temperatures and deformation rates can be used to achieve this.
Titanium alloys have limited cold transformation capabilities
Although titanium has greater cold deformation ability compared with other hexagonal crystal metals (such as zinc, magnesium, and cadmium), the cold working deformation of most titanium alloys is relatively difficult.
Medium alloy and high alloy two-phase titanium alloys are difficult to process and deform in the cold state, mainly due to their high deformation resistance, work hardening during deformation, and prone to cracks and fractures.
A little preheating (to 200~300℃) during deformation can significantly reduce deformation resistance and improve plasticity. Further increasing the temperature to 550~700℃ will not cause serious oxidation and deterioration of the metal structure, but can fundamentally improve the processing plasticity.
Easy to bond and deform tools and molds
This tendency of titanium and titanium alloys during pressure processing can easily lead to the deterioration of the surface quality of the processed materials. Therefore, more stringent requirements are put forward for process lubrication during deformation tools and molds and pressure processing.
Titanium and titanium alloys have high yield ratio and low elastic modulus
This characteristic of titanium and titanium alloys causes the material to be processed to have greater elastic rebound when straightened in a cooling state. It is very difficult to straighten those high-strength titanium alloy materials in a cooling state.
Based on the above processing characteristics of titanium and titanium alloys, full consideration should be given when formulating the production process to facilitate the production of titanium and titanium alloy processing materials.
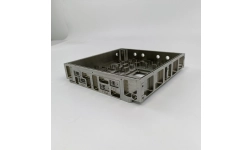