Mechanical Manufacturing Technology And Precision Processing Technology
The manufacturing and production process of modern machinery, as well as its technology and processing links, mainly use intelligence and automation as technical means, which can effectively improve the quality and production efficiency of the manufacturing process and play a major role in promoting the sustainable development of the machinery manufacturing industry. Machinery manufacturing industry. On this basis, a comprehensive analysis of the mechanical manufacturing process and its precision grinding technology, precision broaching technology, grinding technology, ultra-high-speed cutting technology, polishing technology and other precision machining technologies was conducted, aiming to provide a reference for the mechanical manufacturing process. Development of modern machinery manufacturing.
With the rapid development of our country's economy, the machinery manufacturing industry continues to innovate with the support of intelligent technology. The modern process flow used in machinery manufacturing and the related technologies used in production are all based on intelligence and automation, which has led to a qualitative improvement in the technical level of the entire manufacturing production. Analyzing and discussing modern processes and emerging processing technologies in the machinery manufacturing process can effectively improve the production capacity of machinery manufacturing enterprises and help them obtain higher economic benefits.
The extensive development of modern manufacturing processes not only makes rational use of limited resources, but also protects the environment and improves manufacturing quality and efficiency.
The carbon dioxide gas shielded welding process means that during the welding process, technicians use carbon dioxide gas for welding and use the arc as the heat source for the welding operation to fully burn the arc, effectively isolate the air, and ensure the final welding effect. Welding quality. Modern machinery manufacturing processes use carbon dioxide as an insulating gas, mainly because carbon dioxide is an inert gas with strong stability and low cost, which can improve the welding effect. For example: During the mechanical welding process, when the thickness of the plate to be welded is less than 12mm, the welding method can be I-bevel double-sided single-pass welding. Swinging the welding gun laterally can make the weld smooth and smooth, and avoid the problem of bulging in the middle when welding thin plates. For fillet welding, a combination of different methods is required for welding. For example: a 6mm welding leg can be moved directly for welding during the welding process; an 8mm welding leg can be welded by lateral movement during the welding process. During the operation, it is necessary to avoid welding in windy conditions to avoid affecting the final welding effect, so the operation is best performed indoors.
As an important process in mechanical processing and manufacturing, mold forming technology has the ultimate goal of making products more standardized and meeting people's requirements for product production, investment, and use. Mold forming technology is widely used in fields such as household appliances, instrumentation production, and automobile production. The special process of machinery manufacturing in these fields uses electrolytic molding, which has high processing accuracy and can control the accuracy within 10-6. Improving the precision of mechanical parts requires technicians to reasonably control the cutting template area. In the actual processing process, such as when processing the front and rear shells, brackets, etc. of products such as electric fans or cooling fans, the molding conditions require the mold temperature to be 40 to 60°C, the drying conditions to be 80°C for 2 to 4 hours, and the temperature to be controlled at 190 to 190°C. 230℃, the heat deformation temperature is controlled at about 80℃, and the mold shrinkage is controlled at 0.5%~0.7%. In order to solve the problem of rough surface of some workpieces, the mold forming process can be used to complete 75% rough machining and 25% finishing machining. In the mechanical manufacturing process, other manufacturing processes can be used to superimpose physical production. This method mainly uses foil and uses CNC laser machines to efficiently process the contours. After cutting off the excess, lay out a layer of foil and run it over with a heated roller to soften the surface. Apply the cured adhesive to fuse the entire material together, which can improve the production effect and work efficiency after multiple cuts.
The biggest advantage of applying friction stir welding process is that the welder can complete the entire welding process only based on stir head welding. Especially for aluminum alloy products, a welding stirring head can perform 800cm welding. It is not only widely used in machinery manufacturing processes, but also in railway and shipbuilding machinery manufacturing. The friction stir welding process involves many parameters, including the tilt angle of the stir head, rotation speed, insertion depth, insertion speed and welding pressure. The design index of the mixing head inclination angle is generally ±5°. For thin plates with a thickness of 1 to 6 mm, the inclination angle of the mixing head should be a small angle, that is, 1° to 2°; for medium and thick plates with a thickness greater than 6 mm, the inclination of the mixing head needs to be adjusted according to the welding pressure or workpiece structure. Angle, the tilt angle is set to 3°~5°. For thin plate materials, the depth can be set to 0.1~0.3mm; for medium and thick plate materials, the depth can be set to about 0.5mm. The mixing head speed specifications are shown in Table 1.
Table 1 Mixing head speed specifications
Precision grinding technology has precise precision and can obtain sub-micron dimensions, which can effectively ensure the production quality and level of mechanical products. When technicians apply precision grinding technology, they mainly rely on diamond abrasive grinding wheels. They need to ensure that the average particle size of the grinding wheels is about 3 mm. When using a 280mm silicon wafer integrated system for processing and manufacturing, the diamond grinding wheel or finishing should be at the same level. After the silicon wafer is precision ground and polished, the surface roughness of the silicon wafer can be effectively reduced and controlled to 0.8 μm. In addition, the flatness of mechanical products will also be reduced to 0.3μm, which will help improve the manufacturing accuracy of product processing. Some factories use ultra-precision hydrostatic guide rail technology when applying precision grinding technology to transmit hydraulic oil from the external hydraulic power system to each hydraulic slide block, and each slide block is equipped with 6 bearing seats. Use high-pressure oil to support the slider so that it floats evenly on the slide rail. As the cutting force gradually increases, the oil pressure in the bearing seat gradually increases, which can realize the automatic compensation function to ensure that the cutting force and the support force of the oil pressure maintain a certain balance. The circulated hydraulic oil returns to the tank from the slider end in a normal state and can be reused. With its powerful functions, this technology enables the straightness of machine tools to reach 0.4μm and ensures that the geometric processing accuracy of products reaches about 0.9μm. The flatness of products processed using this technology can reach 4.8μm. It should be noted that if the machine tool is not rigid enough during processing, it is easy to cause product deformation due to excessive product temperature. In order to improve cutting accuracy, technologies such as micro-feeding and aerostatic bearings should also be introduced. The machine tool processing flow is shown in Figure 1.
Figure 1 Machine tool processing process flow
The processing requirements for gears and transmission shafts are relatively high, mainly involving connection strength and post-installation operations. Therefore, great attention must be paid to the detailed processing of the internal splines of the gear. When controlling position accuracy, a precise broaching process is required. When precision broaching, the same paving requirements of the involute internal spline indexing circle and the gear inner hole should be analyzed, and different broach structures should be used for precision broaching. For example: Comprehensive analysis of the contact between the guide rail and the inner hole of the gear in each link of processing. By understanding the precision CNC milling produced by these two links, coaxiality control can be achieved. In addition, a set of fixtures composed of a rear guide sleeve, a workpiece fixture, and a front guide sleeve can be used, and internal positioning is used to make the broach and fixture cooperate with each other, thereby effectively controlling and actively responding to the influence of the broach's rear guide belt. .
Precision grinding technology can improve the quality and precision of grinding machinery products. Technicians should use precision grinding techniques when polishing laser mirrors. After the technicians complete the polishing work, they perform coating work on the mirror surface to ensure that the processing flatness of the product can be controlled at 0.048μmcnc quote, the surface roughness of the product can be controlled at 0.81μm, and the mirror reflection efficiency can be controlled at 99.80%. Technicians use polishing machines to precisely grind ceramic bearing balls to control the grinding accuracy of ceramic bearings to 0.1 μm [5]. In the field of automotive machinery manufacturing, it is necessary to effectively control the grinding allowance, and reasonable selection can be made based on the impact of different grinding allowances on the roughness and flatness of the moving ring. Combining Table 2, it can be seen that qualified products can be obtained by controlling the grinding allowance between 0.02~0.03μm.
Table 2 Effects of different grinding allowances on the flatness and roughness of the moving ring
Ultra-precision profiling technology used in the mechanical manufacturing process can be divided into chemical profiling, electrochemical profiling and ultrasonic profiling, among which ultrasonic profiling is the most widely used. Technicians use sound waves to polish the surface of the material to achieve the desired polishing purpose. The ultrasonic profiler can control the product accuracy to 0.02μm, and the roughness deviation can be controlled to 0.1~0.2μm. The ultra-precision polishing process can use new technologies such as liquid grinding, mechanical chemical grinding, and magnetic fluid precision grinding. For machinery manufacturing and processing enterprises, the most commonly used is mechanical chemical grinding technology. This processing technology mainly relies on chemical reactions to grind machinery and can be divided into dry and wet types. Under dry conditions, small-scale chemical reactions facilitate processing. SiO2 abrasive grains with a particle size of 0.01 to 0.02 have strong chemical activity, so the grinding amount is large. When grinding with magnetic fluid, the magnetic abrasive between the magnetic poles is mainly used to form abrasive through the action of the magnetic field. After being adsorbed on the surface of the magnetic pole, the surface of the workpiece is ground. This processing method can effectively grind uneven and complex curved surfaces, improving grinding quality and effect.
With the advancement of modern mechanical design and manufacturing technology, precision processing technology provides important technical support for improving the efficiency of modern mechanical design and manufacturing. Relevant companies need to continuously optimize and innovate precision processing technology to make up for the shortcomings of traditional processing technology in cutting, profiling grinding and other aspects. The article focuses on the study of precision processing technologies such as precision grinding technology, precision cutting technology, precision profile technology, and precision grinding technology, which can effectively improve product accuracy and help comprehensively accelerate the development of the manufacturing industry.
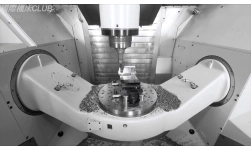