Youjia Europe And America: Using Cutting-edge Technology And Virtual Debugging Technology To Mass Produce Crankshafts And Drive Shafts
Demand for internal combustion engines will continue for several years until the transformation of traditional car companies and the automotive market to new drive systems is complete. For a long time in the past, we have felt the impact of unclear development strategies, process technologies , and even uncertainty of policies and regulations on automobile manufacturing companies. In addition to the rapid development of exhaust gas purification technology and synthetic fuels (also known as electronic fuels), the development of new engine functions has also been put on the agenda. Until drive technology is completely replaced, the focus of crankshaft manufacturing will remain on production efficiency, quality assurance, cost optimization and cutting-edge technology.
The internal combustion engine will remain irreplaceable for many years to come and will continue to evolve into independent drive systems as part of hybrid drives in motor vehicles. However, the trend of internal combustion engines gradually fading out of the stage of history cannot be changed. What is unknown and variable is the schedule and output of each alternative drive system (see Figure 1).
Figure 1: Forecast of the proportion of fuel engines in total vehicles (internal combustion engines and hybrids), data source: MarkLines/LMC Automotive August 2019
In the early stages of production planning, investors often maximize flexibility in product design and factory capacity. During the unclear planning phase, the construction and procurement of new plants will be delayed, while the need to retrofit existing equipment will increase significantly, provided that there are funds to support the optimization of individual process steps.
Figure 2: “Herringbone” layout of the turnkey 4-cylinder engine crankshaft production plant project planned and constructed by Boehringer
Boehringer Ingelheim offers compatible solutions and applications for the following needs: purchasing new production lines, expanding or retrofitting existing plants and upgrading existing systems.
BOEHRINGER's new VDF 221/226 series machine tools can be easily integrated into any production line and automation system. With a small footprint, high-performance components, high machining accuracy, low energy consumption and high flexibility, all specifications required for crankshaft machining and shaft parts can be achieved. The new series of shaft processing machine tools adopts the unified modular configuration system of Boehringer's shaft parts processing lathes, end face processing machine tools and crankshaft special machines, and is designed and developed on this basis (see Figure 3). The tilting machine bed is made of mineral material (polymer concrete) and all guide rails and slide drives are arranged on the same plane. This structure maximizes the stability and damping of the machine tool and minimizes the effects of temperature. Its compact structure also eliminates unnecessary supports and reduces vibration during processing. The engines of modern cars are getting smaller and smaller, but their performance is getting higher and higher, and the smoothness of the power is becoming more and more satisfactory. For crankshafts in passenger cars, this means lower friction due to smaller bearings, less mass and greater material stability. As we all know, during the machining process, small workpieces have poor stability and require high cutting performance. Guide rails, slide drives and modular systems are designed to achieve the above specifications with higher drive forces of the milling unit.
Figure 3: Modular components for crankshaft and camshaft machining lathes and special machine tools
Figure 4: Machine tool design for single-machine production of shaft parts (maximum shaft diameter 290mm, VDF 221 workpiece length 550mm, VDF 226 workpiece length 750mm)
Side journal turning and milling can be achieved in two ways: internal milling (the cutting insert is mounted on the inner ring of the cutter ring) and external milling (the cutting insert is mounted on the outer ring of the cutterhead). After analysis, the choice of process can be simply described as: small shafts are suitable for external milling, and large shafts are suitable for internal milling. There is a gray area between the two that even process experts still need to debate (see Figure 5). In addition to the processing of fixed workpieces (whirlwind milling), in order to fully meet market demand, the BOEHRINGER VDF 221/226 CIM (see Figure 6) series of machine tools has further expanded the scope of workpiece processing. Traditionally, internal milling is used for roughing.
Figure 5: Comparison of axial parallel feed internal milling and swing radial feed external milling methods (excluding cyclone milling for processing fixed workpieces)
Figure 6: The BOEHRINGER VDF 221 CIM turning/milling machine uses axial parallel machining of the main journal and connecting rod journal and an internal milling unit with radial oscillating feed for machining the two end faces.
Innovation in internal hard milling of the crankshaft journal position enables an alternative solution to expensive post-quenching roughing equipment, thus significantly reducing procurement costs. The BOEHRINGER VDF 221 CIM machining center uses an innovative tunnel design to machine crankshaft connecting rod journals, main journals and open gears through internal milling. The machine's highly rigid design enables vibration-free heavy cutting at full load. The VDF 221 CM cylindrical milling machine successfully applies hard finishing technology to achieve finishing machining of shaft parts after quenching. Several major advantages of this technology are:
As a development partner for hard finishing internal milling technology, Ingersoll (Tools) has given us great support in technology optimization. The successfully launched new VDF 221 CIM internal milling machine tool has the following technical highlights in heavy cutting/precision machining of complex workpieces:
The latest CNC end-face processing machine tool BOEHRINGER VDF 221/226 CET is the result of unremitting efforts by experts in crankshaft and shaft processing technology to further improve production efficiency and optimize processing technology. The core component of this new 6-axis machining center is two sets of crown-shaped turrets, each with 8 tool stations, which act as a 3-axis machining unit at either end of a fixed (firmly clamped) workpiece. In addition, specially designed spindle heads and multi-axis heads can be installed on the slide block for special processing. The main technical features of the above components are as follows:
Compared with other commonly used finishing units, the advantage of the top turret is that the driving force of its feed unit directly drives the turret, and each spindle has high power (40kW) and strong feed force (10kN) at the processing position. ). .
The processing unit moves in the Z-axis direction through a stable entrance slide (truss slide), and the transverse slide on it can achieve highly dynamic positioning of the turret in the X and Y-axis directions (refer to the chip-to-chip tool change time). Based on the compact structural design of the VDF 221 CET machining center, the workpiece length can be clamped up to 650mm (maximum weight 280kg), while the extended version VDF 226 CET machining center can clamp shafts up to 3000mm (maximum weight) to 1,400kg). Machine tools can be loaded manually using lifting equipment or automatically using a robot near the front door or a truss manipulator above the machine tool.
Figure 7: BOEHRINGER VDF 221 CET finishing machine, used for machining shaft parts, equipped with 8-spindle powered turret
The modular components of VDF BOEHRINGER machines not only ensure machining quality but also reduce storage costs for spare and wear parts by applying a common parts strategy when installing a complete production line.
All VDF series machine tools are ergonomically designed and can be loaded manually or automatically. The wide processing area meets the needs of part position adjustment, and the workpiece clamping device can be conveniently and easily operated during loading and unloading, even when using lifting equipment. The rotating operation panel can adjust the direction according to the operator's needs. In most cases, automatic loading is done by a truss manipulator from above (Figure 8) or a robot from the front. The standardized design of the "MAG Cell" can be connected to the machine tool as a production cell. It installs a robot on the floor inside to pick up workpieces from storage racks or belt loading mechanisms and send out the processed workpieces in the same way. The “MAG Cell” can add extended functions such as cleaning and/or measurement (Fig. 9). The MAG factory automation program integrates stand-alone machines with loading capabilities into composite turnkey production systems for immediate installation and immediate production. (Example: see Figure 2).
Figure 8: Production line system consisting of shaft machining machines with top loading mechanism designed and produced by MAG Factory Automation
Figure 9: Function expansion of shaft processing machine tools through the “MAG Cell” with automatic workpiece measurement and pallet loading mechanism
First, the process flow and workshop layout will be simulated and optimized through advanced planning tools (see Figure 10). Therefore, whether it is a new machine tool, an old machine tool, or a production line containing both new and old machine tools, output and product quality can be planned during the quotation stage. To achieve maximum production capacity, logistics planning and the management of parallel (redundant) workstations and bottleneck areas (sequential workstations) are crucial. Taking turnkey projects as an example, cutting equipment, measuring equipment, cleaning equipment and assembly equipment can be connected through automated transport systems. In addition, the corresponding process steps can be verified by digital models, and their variant digital production models can also be used to determine the layout of workstations and simulate the material flow. During the project execution phase, these models were further refined and virtual commissioning techniques were implemented to ensure higher product quality and significantly shorten delivery times. Through virtual shadow analysis of system components and virtual commissioning in production models, retrofit planning can be carried out more conveniently and efficiently throughout the entire life cycle of the equipment. Factory digital management can bring more advantages such as operator training, maintenance training and remote services.
Figure 10: Simulation and virtual debugging of shaft machining through tool software "NX CAM" and "Visual Components"
Until fuel engines are completely replaced, efficient factories will continue to produce parts. But as fuel engines are gradually replaced by other alternative drive solutions, it will become possible to use Boehringer's cutting-edge technology and virtual commissioning technology to virtually plan other drive technologies in the future. As the quality requirements for drive shafts in electric drive systems become increasingly higher, the robust and durable Boehringer VDF series machine tools are undoubtedly the ideal choice for processing equipment.
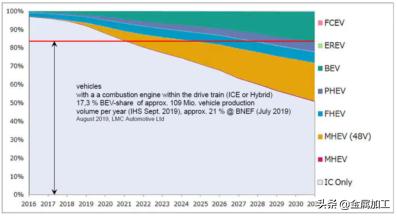