Development Trends And Cutting-edge Trends Of Ultrasonic Precision Machining Technology
As a core technology in the field of advanced manufacturing, ultrasonic precision processing technology has formed a complete theoretical system and technical framework decades later. Since its first application in the industrial sector in the 1950s, the technology has been widely used in high-end manufacturing fields such as aerospace, medical equipment and precision molds, with its unique handling advantages. Its core principle is to use cavitation effects and shock waves generated by high frequency mechanical vibrations to achieve precise processing of hard and brittle materials, with high characteristics such as high machining accuracy, good surface quality and small heat-affected zones.
However, with the development of science and technology and the continuous upgrading of industrial demand, the technology of related processes and equipment still needs further exploration and improvement. At present, there are still many technical bottlenecks in terms of processing efficiency, complex surface treatment capabilities, intelligent control, etc. Especially in handling new generation semiconductor materials, optical glass and other ultrasonic materials, traditional ultrasonic processing technology no longer meets the requirements of micro-nano-scale processing accuracy. In addition, there is a need to urgently develop key technologies such as vibration stability control, tool wear monitoring and process parameter optimization.
To address these challenges, domestic and foreign research institutions are committed to developing new composite ultrasonic processing technologies, such as ultrasonic-assisted laser processing, ultrasonic-assisted electric spark processing, etc. At the same time, the in-depth integration of modern information technologies, such as the development of artificial intelligence and big data and ultrasonic processing technologies, has become the process in this field. These innovations will not only promote the further development of ultrasonic precision processing technology, but will also provide strong technical support for the transformation and upgrading of high-end manufacturing industries.
(1) Ultrasonic vibration cutting technology>
With the development of traditional processing technology and high-tech, ultrasonic vibration cutting technology is becoming more and more widely used, and the research on vibration cutting is becoming more and more in-depth, mainly reflected in the following aspects.
① Develop and adopt new tool materials.
② In-depth study of vibration cutting mechanism.
③Design and develop new ultrasonic vibration systems and practical and effective equipment and equipment.
④ Research and promotion of ultrasonic elliptical vibration cutting.
⑤ Ultrasonic milling processing technology. Ultrasonic milling is a relatively new approach to processing. There is little information about the optimization of processing parameters and studies are needed to provide a reference for ultrasonic milling.
(2) Ultrasonic compound processing technology>
In recent years, a variety of ultrasonic composite processing technologies, such as ternary composite processing of ultrasonic electric spark abrasives, ultrasonic pulse electrolysis treatment and ultrasonic electrolytic composite composite grinding treatment, have developed rapidly. And have good application prospects. Its future main development direction is reflected in the following aspects.
①Combined with multiple treatment methods.
② Development is developing towards green manufacturing to achieve pollution-free processing.
③In-depth research on processing mechanisms, processing technologies and actual processing technologies.
(3) Rotating ultrasonic processing>
The development of domestic advanced ultrasonic processing machine tools is very backward, and there are still no rotating ultrasonic processing machine tools for the market. In rotary ultrasonic processing, how to effectively connect the tool and the ultrasonic vibration system to smoothly transmit ultrasonic energy; how to achieve high rotation of the ultrasonic processing machine tool and effective propagation and conversion of ultrasonic energy; the material removal mechanism model is only suitable for workpiece materials used by researchers, and a new material removal mechanism model is needed to comprehensively consider various mechanisms of action to establish a new material removal mechanism model suitable for the rotation treatment of hardened and brittle materials; linking force with the torque amplitude and energy distribution during the treatment process will be an important study in future rotary ultrasonic processing.
(4) Ultra-precision processing technology>
With the improvement of product accuracy requirements, applying ultrasonic processing technology to precise processing lathes is a development trend of ultrasonic processing technology. Ultrasonic processing technology is divided into three categories: ultrasonic cutting, ultrasonic grinding, and ultrasonic grinding and polishing.
With the application and development of ultrasonic processing technology, ultra-precision processing technology has developed in the following directions: high precision and high efficiency; awareness of grinding rather than research, grinding rather than polishing, etc. so that a single device can complete various processing (such as turning, drilling, milling, grinding, grinding and optical finish); realize ultra-precision processing equipment required to handle large-scale optoelectronic equipment, micromotor machinery, optoelectronic information equipment, etc.; reduce energy consumption and waste liquid emissions during processing.
(5) Microphone ultrasonic processing technology>
With the increasing miniaturization and immobilization of industrial products represented by micro machinery, especially in the wide application of hardened and brittle materials such as crystalline silicon, optical glass and engineering ceramics in micro machinery, high-priority three-dimensional energy processing technology has become an important research topic in the manufacturing industry.
Currently, the main methods that can be used to deal with hard and brittle materials include lithography, electric spark processing, laser processing, sonication, ultrasonication and other special processing technologies. Compared with electrospraying, electrolytics, laser treatments, and other technologies, ultrasonic treatment does not depend on the conductivity of the material and has no thermal physical effects. It can also handle three-dimensional shapes with high depth and width ratios compared to lithography. This determines that sonication technology has unique advantages in handling non-metal hard and brittle materials such as ceramics and semiconductor silicon. With the successful production of micro-tools in the Institute of Production Technology at the University of Tokyo, and a reasonable solution to the accuracy of micro-tool clamping and tool rotation, the use of engineering vibrations allows sonication to make ultrasound a Micro-engineered material, thus treating micro-POREs with a minimum diameter of φ5μm on engineered ceramic materials.
(6) Expand to new areas>
Ultrasonic treatment has achieved remarkable results in the manufacturing field and is widely used in the military, aerospace, automotive industries, etc. With the continuous development of ultrasonic processing technology, this technology has rapidly developed into a new spiritual practice, and has expanded the implementation-based for of Micro Cot in the fields of biology, daily life, etc. The system is implemented, the model is implemented, the model is implemented, the model is implemented, the model is implemented, the model is implemented, the model is implemented, the model is implemented, the model is implemented, the model is implemented, the model is implemented, the model is implemented, the model is implemented, the model is implemented, the model is implemented, the model is implemented. The technology has achieved the integration of the system and used this system to perform ultrasonic vibration micro-cutting experiments on the brain tissue of newborn mice, proving the feasibility and effectiveness of this technology. Like other special processing technologies, ultrasonic processing technology is constantly improving and moving towards high precision and refinement. Microsonic ultrasonic processing technology is expected to be a powerful complement to micro-electromechanical system (MEMS) technology.
The future prospects of ultrasonic welding technology>
Looking ahead, ultrasonic welding technology will develop towards higher accuracy, higher efficiency and more environmentally friendly directions. As the first domestic enterprise to master servo controlled pressure ultrasonic welding technology, international brand ultrasonic ultrasonic has played a leading role in this trend.
On the one hand, with the continuous emergence of new materials and new processes, ultrasonic welding technology will face more challenges and opportunities. On the other hand, through continuous technological innovation and process optimization by enterprises such as ultrasonic welding technology, more effective and environmentally friendly solutions will be provided for material processing. Meanwhile, the application of ultrasonic welding technology in emerging fields such as micro-nanofabrication and biomedicine will continue to expand, thus contributing to scientific and technological advancement and social development.
In short, ultrasonic welding technology has broad development prospects, and its position in the field of material processing will become increasingly important. As research and technological progress deepens, ultrasonic welding technology will bring more surprises and possibilities to industrial manufacturing.
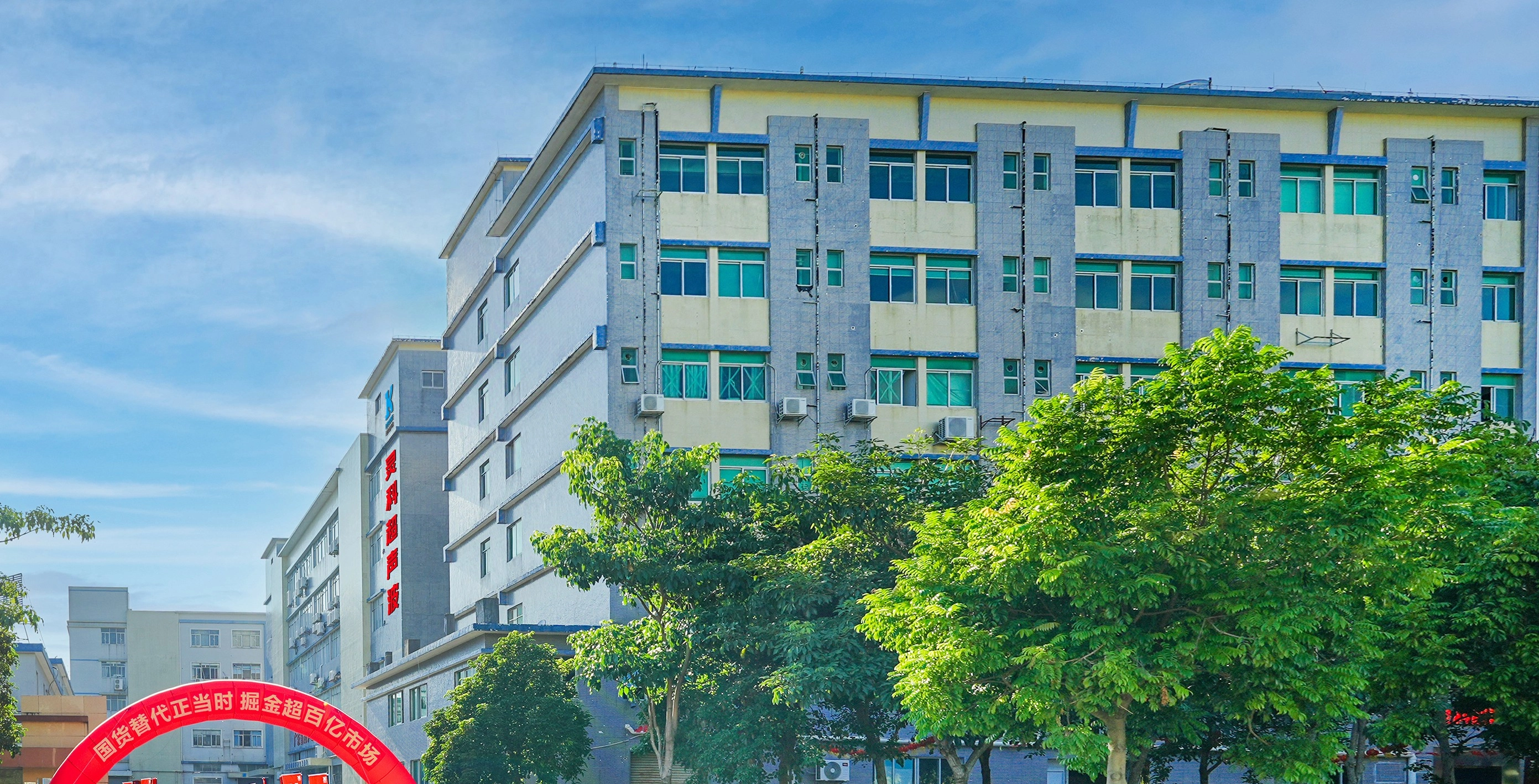