Trends And Applications Of Laser Precision Manufacturing Processing In 2025
As one of the core technologies of modern manufacturing, laser precision manufacturing companies show diversified and high-end development trends by promoting technological innovation and market demand. Laser precision machining equipment is developing intelligence and integration. In terms of intelligence, the processing process can be monitored and accurately controlled through sensors and control systems in real time. Integration combines control, process and lasers to enable integrated optical, mechanical, electrical and material handling, and improves production efficiency and processing quality.
Laser precision manufacturing and processing
Application Area>
Micro-nanofabrication and optical assembly processing: In micro-nanofabrication, it is used to manufacture micro-electric devices, mechanical parts, and more. As far as optical component processing is concerned, high-precision optical mirrors, gratings, etc. can be made to ensure surface quality, shape accuracy and optical performance of optical components.
Automotive Manufacturing Field: In terms of cutting, it can cut auto parts with high precision, cutting into complex shapes, narrow cuts and less material waste. In terms of welding, precise welding of body welded components can be achieved, such as connection between the top cover and the side cover, door interior panels and body frame, reducing body deformation and achieving a lightweight design.
Aerospace Field: As far as hole punching is concerned, it is used to make cooling holes in aircraft engines to ensure engine stability and efficiency. In terms of structural parts manufacturing, aerospace materials such as titanium and aluminum alloys can be cut and welded to manufacturing components such as aircraft wings and fuselage frames.
Electronic equipment manufacturing field: In terms of chip manufacturing, laser etching technology can achieve high-precision circuit mode on microelectrode chips. In terms of connection, it is used to accurately connect chips, circuit substrates and other electronic components to ensure connection stability and electrical performance.
Area of medical device manufacturing: In terms of cutting, it is used to cut implantable devices and surgical tools in human bodies such as medical catheters and needles. In terms of welding, it is used to weld small parts for precision instruments such as pacemakers and surgical blades. In terms of marking, company logos and product information can be permanently marked on medical devices.
New Energy Field: In the photovoltaic industry, it is used to produce efficient solar cells such as PERC, IBCcnc metal machining, HJT and to improve battery conversion efficiency and reduce costs. In the field of new energy vehicles, it is used to precisely weld key components such as LiDAR integration, battery battery batteries and packaging modules.
Ocean Bridge Manufacturing Field: High precision cutting can be performed to ensure the vertical and smoothness of the cutting edges of the ship sheets and pipes. It can also enable smart welding, combining visual recognition and robot adaptive programming to improve welding quality and efficiency.
Technical Performance>
Accuracy reaches a high level: The laser beam can be focused to a small size, so high accuracy can be achieved in the field of precision machining. For example, laser precision processing of thin plates (0.1-1.0mm) is the main processing object, and the processing accuracy is usually ten microns. In certain specific micro-nano manufacturing cases, micro- or even nano-processing accuracy has been achieved. For example, laser precision machining technology can generate very small mechanical structures and sensor components during the manufacturing process of micro-motor electromechanical systems (MEMS).
Various processing technologies coexist and developed: Laser precision machining has many types of processes and is rapidly developing, involving hole punching, cutting, welding, welding, etching, surface treatment, etc.
As far as hole drilling is concerned, lasers can be used to process small holes and have a diameter of tens of microns on hard materials (such as carbonized alloys) and can handle various special shapes of holes with special requirements on brittle materials ( For example, ceramics, etc.), such as blind holes, square holes, etc.
During the cutting process, laser-precision cutting can cut sheet material at high speed and high precision, with smooth flat cutting and small heat-affected areas. For example, in mobile phone screen cutting, fingerprint recognition table cutting and other processes that require high precision. It has a good application; laser welding technology can achieve better welding quality, whether it is welding of the same or different materials, with smaller heat-affected areas and rapid welding speeds, especially in automobile manufacturing, electronic equipment manufacturing and Medical equipment manufacturing. It is widely used in many fields for precision welding parts.
Laser etching technology plays an important role in high-precision processing fields such as electronic semiconductor materials. By laser etching, very fine patterns and patterns can be formed on the surface of the material, and the etching depth and width can be adjusted as needed.
Product Recommendations>
Electric Coaxial Optical Module
The working area of the scan head can be observed according to the camera. Typical applications include process monitoring or positioning workpiece positions and angles. During laser machining, coaxial modules ensure easy integration into new and existing systems. The mechanical interface of the module can be directly installed between the galvanometer scan head and the laser flange. Main applications: laser marking, laser welding, laser cutting, machine vision, laser micromachining, laser resistance adjustment.
355 UV/532 green light precision cutting head
In the PCB board industry, it is mainly used for UV cutting PCB laser panels such as FR4, reinforced steel plates, FPC, soft and hard adhesive plates and fiberglass boards. Ultrathin metal material Ultrathin metal refers to metal materials less than 0.2mm, such as copper foil, aluminum foil, stainless steel and alloy materials. UV laser cutting requires no burrs, low carbonization and no deformation for precise cutting. It is commonly used in military spare parts, photovoltaic copper foils and other industries.
Rotary cutting micropore treatment head
The cutting head is a precision fiber (λ=) cutting head. The collimation and focus lenses are multi-piece combinations. The focus point is small and the accuracy is very high. You can cut it into small holes and rotate the XY drive. Micro-pores can be made on thin titanium plates, aluminum plates, copper plates and stainless steel plates below 1 mm, with hole diameters of φ0.1-0.5 mm, combined with coaxial blowing, good cutting roundness and smooth edges.
Constant temperature laser welding system
The photoelectric laser welding system consists of coaxial vision laser welding heads (optional variety of spots), 976/980NM constant temperature semiconductor laser, real-time temperature feedback system, CCD coaxial positioning system and feeding mechanism (wire feeding mechanism/distribution mechanism) by Mechanism composition; explores the independently developed intelligent welding software through years of welding process to support the import of multiple format files. The original PID online temperature regulation feedback system can effectively control constant temperature welding and ensure welding yield and accuracy. This is more suitable for precise welding of highly accurate microelectronics. This product is widely used and can be used for online production or independent processing.
Future prospects>
It is estimated that by 2025, the size of China's precision laser processing market will exceed 150 billion yuan, with an average annual growth rate of more than 15%. With the in-depth integration of 5G, AI and new energy, laser technology will further penetrate into emerging fields such as quantum communication and flexible electronic devices, becoming the core driving force for "intelligent manufacturing upgrade". Companies need to seize the window period of policy support (such as the "14 Five-Year Plan" high-end equipment plan) and develop differentiated product and technology reserves to cope with global competition.
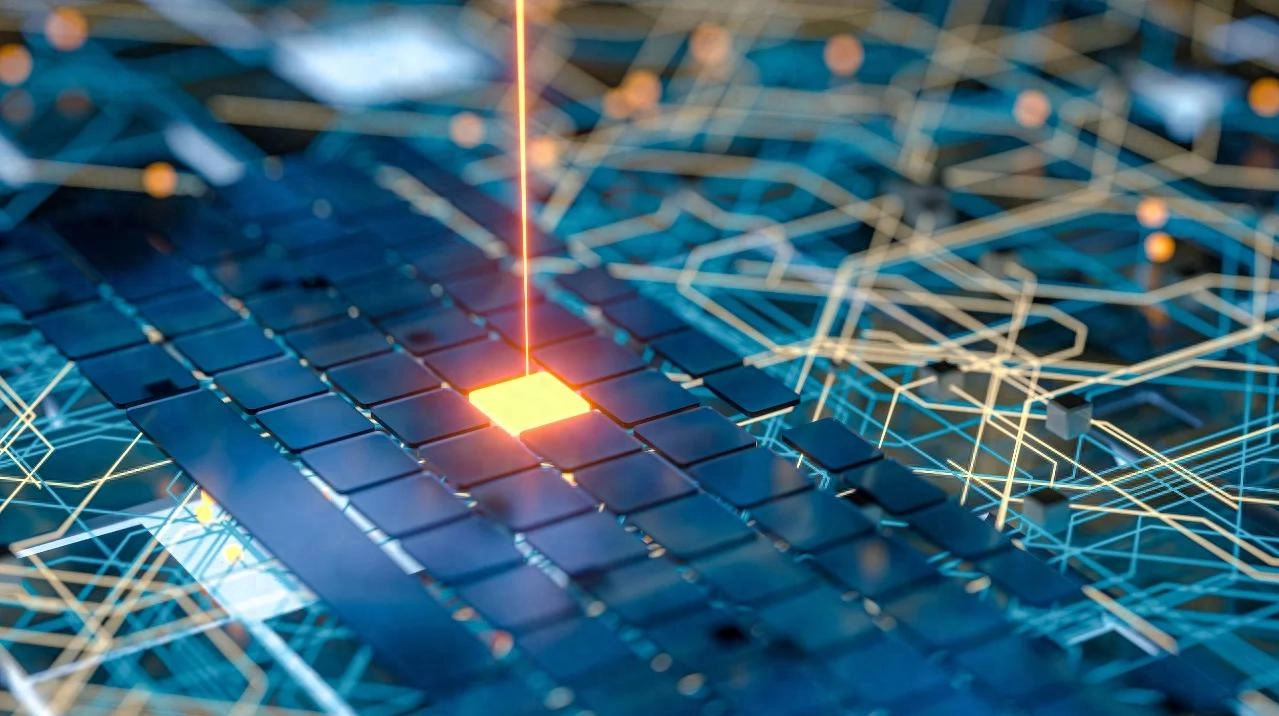