What Is The Process Flow Of Nickel-based Alloy Free Forging? Shanghai Alloy Manufacturers Tell You
Nickel-based alloy free forging> What is the process flow? In today's era of rapid technological development, many high-end fields are emerging. From the soaring aerospace engineering to the high-end equipment manufacturing that supports the heavy equipment of major countries, nickel-based alloys play a pivotal role. Why is it so important? This is due to its outstanding high temperature resistance, corrosion resistance and high strength properties, making it the best choice to meet the needs of complex working conditions. To process nickel-based alloys into various precision components, the free-forging process is crucial. So, what is the process flow of nickel-based alloy free forging? Let’s take a look with the editor next.
Raw material inspection:
This is the starting point of the nickel-based alloy free forging process and the cornerstone of ensuring the quality of the final product. First of all, after purchasing nickel-based alloy raw materials, CNC machining companies must use professional spectrum analyzers and other equipment to carefully measure the contents of nickel, chromium, molybdenum, titanium and other elements, and must ensure their chemical composition and alloy formula required for design. Close match. You know, even a small deviation in the element content may bring great trouble to the performance of the alloy. For example, if there is less nickel, corrosion resistance may be significantly reduced. At the same time, ultrasonic flaw detectors, radiographic flaw detection and other methods must be used to thoroughly check whether there are cracks, inclusions and other defects inside the raw materials. Only raw materials with accurate composition and pure texture are qualified to enter the next forging process.
Blank heating:
Forging temperature plays a decisive role in free forging of nickel-based alloys. Due to the high melting point and slow heat conduction of nickel-based alloys, the billet must be placed in a special heating furnace to slowly heat up. Generally, an electric furnace or a gas furnace is used to operate according to a predetermined heating curve to heat the blank evenly and prevent local overheating from causing thermal stress and cracks. Under normal circumstances, the initial forging temperature should be controlled between 1000°C and 1150°C. This range can keep the alloy in a good plastic state and facilitate deformation; the final forging temperature cannot be lower than 900°C. If it is lower, the plasticity of the alloy will drop sharply and forced forging will be inevitable. Cause cracking. During the heating period, the temperature in the furnace and the billet temperature must be monitored in real time, and the heating power and time must be accurately controlled to prepare the billet for subsequent forging in "excellent condition".
Forging work:
This is the core of the entire process and extremely tests the skills and experience of the forging workers. When starting work, you need to select appropriate forging equipment according to the product shape and size requirements. Common ones include air hammers, friction presses, hydraulic presses, etc. If you want to forge simple shaft parts, you can first use an air hammer to initially stretch it, and then hammer it repeatedly to make the blank elongate in the axial direction and reduce the cross-section; when it comes to complex shapes, CNC miling, such as those with inner cavities For aero-engine blade forgings, you can rely on the powerful pressure of the hydraulic press and the precision forging of special molds. During the forging process, workers must always pay attention to the deformation of the blank, flexibly adjust the strength and direction of each hammering or pressure, and follow the principle of "light-heavy-light". Light blows at the beginning will deform the blank evenly, and increase the force in the middle to shape the desired shape. shape and then lightly trimmed at the ends to ensure precise dimensions and high surface quality of the forging while avoiding forging defects.
Intermediate test:
After the stage forging task is completed, it is crucial to conduct an intermediate inspection immediately. Use measuring tools such as calipers and micrometers to carefully measure the dimensional accuracy of the forgings and compare with the design drawings. If any deviation is found, the subsequent forging process must be adjusted immediately to correct it. Use a metallographic microscope to analyze the metallographic structure of the forging to see if the grain size and shape do not meet the process standards. If the grains are coarse, it may mean that the forging temperature is too high or the deformation is insufficient, and subsequent operations must be optimized. In addition, the hardness tester can also be used to detect the hardness of different parts of the forging, based on which the internal stress distribution can be judged, providing a basis for subsequent heat treatment to ensure an overall and stable improvement in the quality of the forging. - Round shape.
Heat treatment:
The purpose of the heat treatment process is to optimize the performance of nickel-based alloy forgings, eliminate residual stress in the forgings, and adjust the metallographic structure. Common heat treatment processes include annealing, solution treatment, aging treatment, etc. Annealing can reduce the hardness of forgings and improve their plasticity. Generally, it is kept at 800℃-950℃ for a period of time, and then slowly cooled; solution treatment is to heat the forging to a high temperature to fully dissolve the alloy elements, and then cool it quickly to obtain a supersaturated solid solution to strengthen the alloy. Strength and corrosion resistance; aging treatment is to keep the forgings after solid solution treatment at a lower temperature for a long time to promote the precipitation of alloy elements and further improve performance. Different nickel-based alloy products can flexibly combine these processes according to service requirements to create high-performance forgings that can adapt to various harsh working conditions.
Surface treatment:
Although the performance of the heat-treated forgings meets the standards, surface treatment is required in order to improve corrosion resistance, wear resistance and appearance quality. If forgings are used in the marine environment or chemical industry, electroless nickel plating or electrochromic plating processes are often used to deposit a dense metal protective layer on the surface to isolate corrosive media; in situations with severe mechanical wear, such as aircraft engine gears, Surface strengthening processes such as nitriding and carburizing are used to improve surface hardness and wear resistance. At the same time, forgings must be finely polished to remove surface oxide scale and burrs to make the surface smooth and clean, which not only meets assembly requirements but also extends service life. At this point, the process flow of nickel-based alloy free forging is completed.
Taimco Metal Products (Shanghai) Co., Ltd. was established in 2004 and specializes in the research and development, production, processing and sales of mid-to-high-end metal materials at home and abroad; its products cover aluminum alloys, stainless steel, alloy steel, special alloys, copper alloys and other metals Material. The company has established long-term material research and development and production cooperation with a number of materials research institutes and well-known material factories. It is good at the solution development and comprehensive application of aerospace and semiconductor aluminum alloys, high-end special materials, alloys and other metal materials; it has now grown into a high-end A well-known dealer in the metal materials industry.
To sum up, Nickel-based alloy free forging> Including raw material inspection, billet heating, forging operations, intermediate inspection, heat treatment, surface treatment and other fine processes, all links are closely connected and coordinated. Each process has technical points, and a slight oversight may affect product quality. Only by strictly controlling the process and operating precisely can we forge high-quality nickel-based alloy products that meet the needs of high-end manufacturing and help related industries flourish.
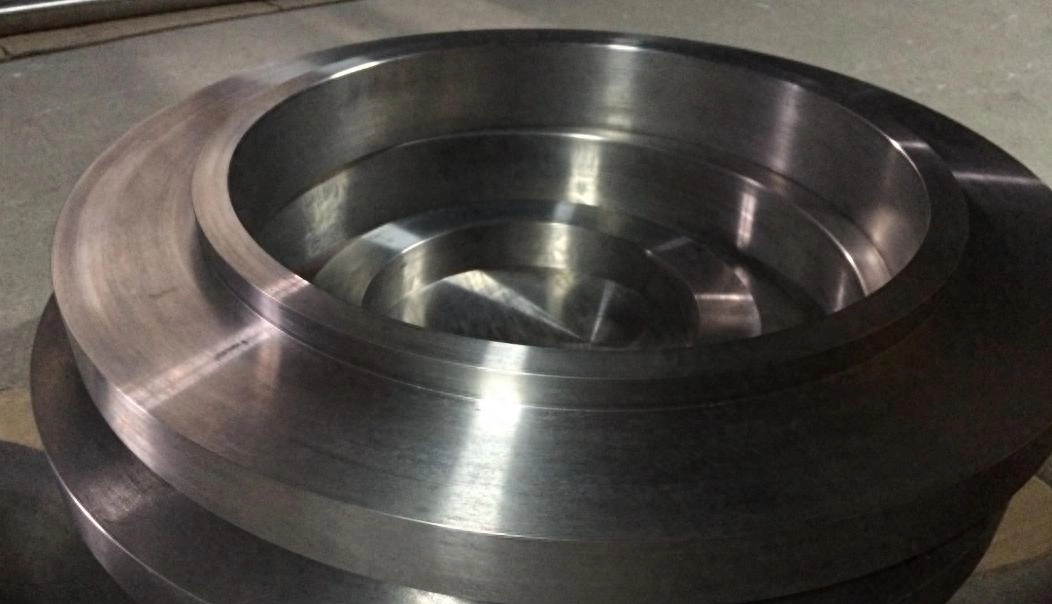