An In-depth Analysis of the Production Challenges Related to CNC ABS Parts and Three-way Catalytic Converters, with a Focus on the Issue of Poor Team Collaboration in the Production Workshop
Introduction to CNC ABS Parts
What are CNC ABS Parts?
CNC ABS parts refer to components that are manufactured using Computer Numerical Control (CNC) technology with Acrylonitrile Butadiene Styrene (ABS) as the raw material. ABS is a popular thermoplastic polymer known for its excellent mechanical properties, such as high impact resistance, good dimensional stability, and ease of processing. CNC technology, on the other hand, allows for precise and accurate machining of these parts, ensuring tight tolerances and high-quality finishes. CNC ABS parts find applications in a wide range of industries, including automotive, electronics, and consumer goods.
Advantages of CNC ABS Parts
One of the key advantages of CNC ABS parts is their high precision. The CNC machining process can achieve extremely accurate dimensions, which is crucial for parts that need to fit together precisely. For example, in the automotive industry, CNC ABS parts used in engine components must have exact dimensions to ensure proper functioning. Additionally, ABS has good chemical resistance, making CNC ABS parts suitable for use in harsh environments where they may come into contact with various chemicals. Another advantage is the ability to produce complex shapes and geometries. CNC machines can create intricate designs that would be difficult or impossible to achieve with traditional manufacturing methods.
Challenges in Producing CNC ABS Parts
Despite their many advantages, the production of CNC ABS parts also presents several challenges. One of the main challenges is the need for skilled operators. CNC machines require operators who have a deep understanding of programming and machining principles. Any errors in programming can lead to defective parts and wasted materials. Another challenge is the cost of equipment and maintenance. CNC machines are expensive to purchase and require regular maintenance to ensure their accuracy and reliability. Moreover, the production process can be time-consuming, especially for complex parts, which can impact production efficiency.
Overview of Three-way Catalytic Converters
Function of Three-way Catalytic Converters
Three-way catalytic converters play a vital role in reducing harmful emissions from internal combustion engines. They are designed to convert three types of pollutants - carbon monoxide (CO), hydrocarbons (HC), and nitrogen oxides (NOx) - into less harmful substances. The converter contains a catalyst, usually made of precious metals such as platinum, palladium, and rhodium, which promotes chemical reactions that convert the pollutants into carbon dioxide (CO2), water (H2O), and nitrogen (N2). This helps to improve air quality and reduce the environmental impact of vehicle emissions.
Importance in the Automotive Industry
In the automotive industry, three-way catalytic converters are essential components for meeting increasingly strict emissions regulations. Governments around the world have implemented strict standards to limit the amount of pollutants that vehicles can emit. Three-way catalytic converters enable automakers to comply with these regulations and produce more environmentally friendly vehicles. They are also important for improving the overall performance and efficiency of engines. By reducing emissions, catalytic converters can help engines run more smoothly and efficiently, leading to better fuel economy.
Production Considerations for Three-way Catalytic Converters
The production of three-way catalytic converters requires careful attention to several factors. The choice of catalyst materials is crucial, as it affects the converter's efficiency and durability. The manufacturing process must also ensure that the catalyst is evenly distributed and properly bonded to the substrate to maximize its effectiveness. Additionally, the design of the converter must take into account factors such as exhaust gas flow, temperature, and pressure to ensure optimal performance. Any flaws in the production process can lead to reduced converter efficiency and increased emissions.
The Problem of Poor Team Collaboration in the Production Workshop
Causes of Poor Team Collaboration
Poor team collaboration in the production workshop can be attributed to several factors. One common cause is a lack of clear communication channels. If team members are not able to communicate effectively with each other, misunderstandings can occur, leading to errors and inefficiencies. Another factor is a lack of shared goals and vision. When team members do not have a common understanding of the production objectives, they may work towards different goals, resulting in a lack of coordination. Additionally, personal conflicts and differences in work styles can also contribute to poor collaboration.
Impact on Production
The consequences of poor team collaboration in the production workshop can be significant. It can lead to delays in production schedules, as tasks may not be completed in a timely manner due to lack of coordination. This can result in missed deadlines and lost business opportunities. Poor collaboration can also lead to quality issues, as errors may go unnoticed or uncorrected due to a lack of communication. In the case of CNC ABS parts and three-way catalytic converters, quality is of utmost importance, and any defects can have serious implications for the performance and safety of the final products.
Solutions to Improve Team Collaboration
To address the issue of poor team collaboration, several measures can be taken. First, it is essential to establish clear communication channels. This can include regular team meetings, the use of communication tools such as instant messaging platforms, and the creation of a collaborative work environment where team members feel comfortable sharing their ideas and concerns. Second, a shared vision and goals should be defined and communicated to all team members. This will help to align their efforts and ensure that everyone is working towards the same objectives. Third, team-building activities can be organized to improve relationships and foster a sense of teamwork. Finally, conflicts should be addressed promptly and resolved in a constructive manner to prevent them from affecting collaboration.
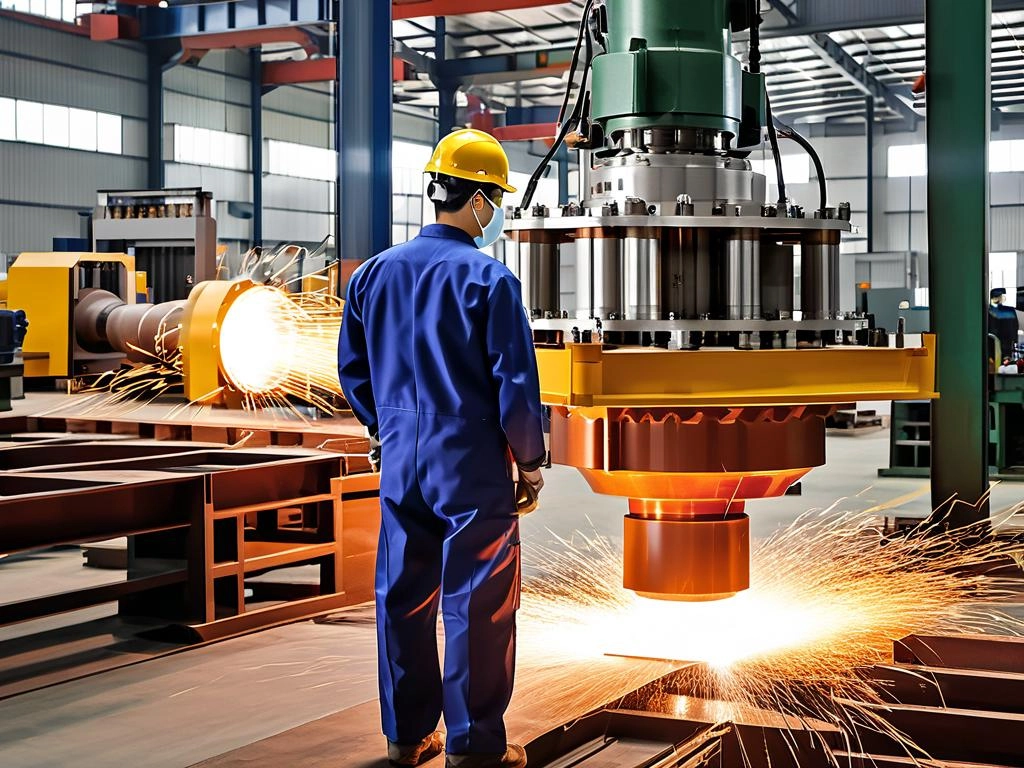
Conclusion
In conclusion, the production of CNC ABS parts and three-way catalytic converters is a complex process that requires a high level of skill and precision. However, poor team collaboration in the production workshop can undermine the quality and efficiency of production. By understanding the causes and impacts of poor collaboration and implementing appropriate solutions, manufacturers can improve teamwork, enhance production processes, and produce high-quality products that meet the demands of the market and regulatory requirements. It is crucial for companies to recognize the importance of team collaboration and invest in strategies to foster a collaborative work environment for the long-term success of their production operations.