Improving Water Jet Machining Cut Quality with CNC Lead and Shaft Rod: A Technical Approach
Introduction to Water Jet Machining
What is Water Jet Machining?
Water jet machining is a manufacturing process that uses a high-pressure stream of water, often mixed with abrasive particles, to cut through various materials. It is a versatile technique applicable to a wide range of materials, including metals, plastics, ceramics, and composites. The process offers several advantages, such as minimal heat-affected zones, no mechanical stress on the workpiece, and the ability to cut complex shapes with high precision.
Applications of Water Jet Machining
Water jet machining finds applications in numerous industries. In the automotive industry, it is used for cutting and shaping parts with intricate designs. In the aerospace sector, it helps in manufacturing components with high precision requirements. The medical field also benefits from water jet machining for creating surgical instruments and implants. Additionally, it is widely used in the manufacturing of electronic components, where precision is of utmost importance.
Challenges in Water Jet Machining Cut Quality
Surface Roughness
One of the major challenges in water jet machining is achieving a smooth surface finish. The high-pressure water stream, especially when combined with abrasives, can cause surface irregularities. These irregularities can affect the functionality and aesthetics of the final product. For example, in the case of parts used in optical applications, a rough surface can lead to light scattering and reduced performance.
Dimensional Accuracy
Maintaining precise dimensional accuracy is another significant challenge. Variations in water pressure, nozzle wear, and material properties can result in deviations from the desired dimensions. This is particularly critical in industries such as aerospace and medical, where even small dimensional errors can have serious consequences.
Taper and Kerf Width
Taper, which is the difference in width between the top and bottom of the cut, and kerf width, the width of the material removed during cutting, are important parameters to control. Excessive taper or kerf width can lead to material waste and affect the fit and assembly of parts.
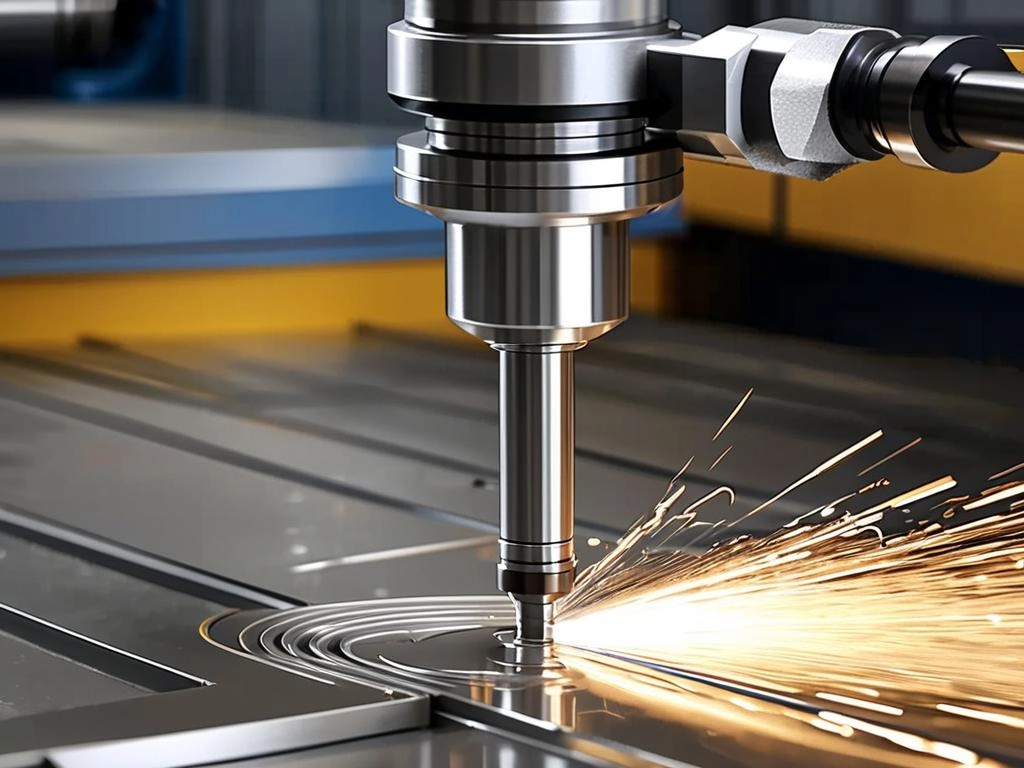
The Role of CNC Lead and Shaft Rod in Cut Quality Improvement
CNC Lead: Precision Motion Control
The CNC lead plays a crucial role in controlling the movement of the cutting head with high precision. It ensures accurate positioning and smooth motion, which is essential for achieving consistent cut quality. By precisely controlling the speed and direction of the cutting head, the CNC lead helps in reducing surface roughness and improving dimensional accuracy. For example, in a complex cutting pattern, the CNC lead can guide the cutting head along the desired path with minimal deviation, resulting in a high-quality cut.
Shaft Rod: Stability and Rigidity
The shaft rod provides stability and rigidity to the cutting system. It helps in reducing vibrations during the cutting process, which can significantly affect the cut quality. A stable and rigid shaft rod ensures that the cutting head remains in the correct position and orientation, minimizing the chances of errors. This is especially important when cutting hard or brittle materials, where vibrations can cause cracking or chipping.
Synergy between CNC Lead and Shaft Rod
The combination of the CNC lead and shaft rod is key to improving water jet machining cut quality. The CNC lead provides the precise motion control, while the shaft rod ensures the stability needed for accurate cutting. Together, they enable the cutting system to achieve high levels of precision and consistency, resulting in better surface finish, dimensional accuracy, and control over taper and kerf width.
Strategies for Optimizing Cut Quality
Proper Calibration and Maintenance
Regular calibration of the CNC lead and shaft rod is essential to ensure their optimal performance. This includes checking for any misalignments, wear, or damage and making the necessary adjustments. Proper maintenance, such as lubrication and cleaning, can also extend the lifespan of these components and improve their reliability.
Optimal Cutting Parameters
Selecting the appropriate cutting parameters, such as water pressure, abrasive flow rate, and cutting speed, is crucial for achieving good cut quality. These parameters need to be adjusted based on the material being cut and the desired outcome. For example, higher water pressure may be required for cutting thicker or harder materials, but it may also increase the risk of surface roughness if not properly controlled.
Advanced Control Algorithms
Using advanced control algorithms can further enhance the performance of the CNC lead and shaft rod. These algorithms can compensate for any errors or variations in the cutting process, ensuring more accurate and consistent results. For instance, adaptive control algorithms can automatically adjust the cutting parameters based on real-time feedback from sensors, optimizing the cut quality.
Conclusion and Future Directions
Summary of Findings
In conclusion, improving water jet machining cut quality requires a comprehensive approach that involves the proper use of CNC lead and shaft rod, along with strategies for calibration, parameter optimization, and advanced control. By addressing the challenges related to surface roughness, dimensional accuracy, and taper and kerf width, manufacturers can achieve higher quality cuts and improve the overall performance of their products.
Future Research and Development
Looking ahead, further research and development are needed to continuously improve water jet machining technology. This could include the development of more advanced CNC lead and shaft rod systems with higher precision and stability, as well as the exploration of new cutting materials and techniques. Additionally, the integration of artificial intelligence and machine learning algorithms could enable more intelligent and automated control of the cutting process, leading to even better cut quality.
Industry Impact
The improvement in water jet machining cut quality has significant implications for various industries. It can lead to enhanced product quality, reduced manufacturing costs, and increased competitiveness. For example, in the automotive and aerospace industries, higher quality parts can improve the performance and safety of vehicles and aircraft. In the medical field, precise and smooth cuts are essential for the production of reliable surgical instruments and implants.