Unveiling the Intricacies of CNC Stainless Steel Machining, Semiconductor Part Machining, and the Challenges Posed by the Inaccuracy of Measuring Tools
CNC Stainless Steel Machining: Precision and Versatility
The Basics of CNC Stainless Steel Machining
CNC stainless steel machining is a highly precise manufacturing process that utilizes computer numerical control (CNC) technology to shape and fabricate stainless steel components with utmost accuracy. Stainless steel, known for its excellent corrosion resistance, strength, and aesthetic appeal, is a popular choice in various industries such as automotive, aerospace, and medical. In CNC machining, a computer program controls the movement of cutting tools, enabling the creation of complex geometries and tight tolerances.
Advantages of CNC Stainless Steel Machining
One of the key advantages of CNC stainless steel machining is its ability to produce consistent and high-quality parts. The precision offered by CNC machines ensures that each component is manufactured to exact specifications, reducing the need for manual adjustments and minimizing errors. Additionally, CNC machining allows for efficient production, as multiple operations can be performed in a single setup, saving time and increasing productivity. Moreover, the versatility of CNC machines enables the machining of a wide range of stainless steel grades, catering to different application requirements.
Applications of CNC Stainless Steel Machining
CNC stainless steel machining finds extensive applications in numerous industries. In the automotive sector, it is used to manufacture engine components, exhaust systems, and decorative parts. The aerospace industry relies on CNC machining for producing aircraft parts that require high strength and corrosion resistance. In the medical field, stainless steel components machined with CNC technology are used in surgical instruments, implants, and medical devices. The precision and reliability of CNC stainless steel machining make it an indispensable process in these and many other industries.
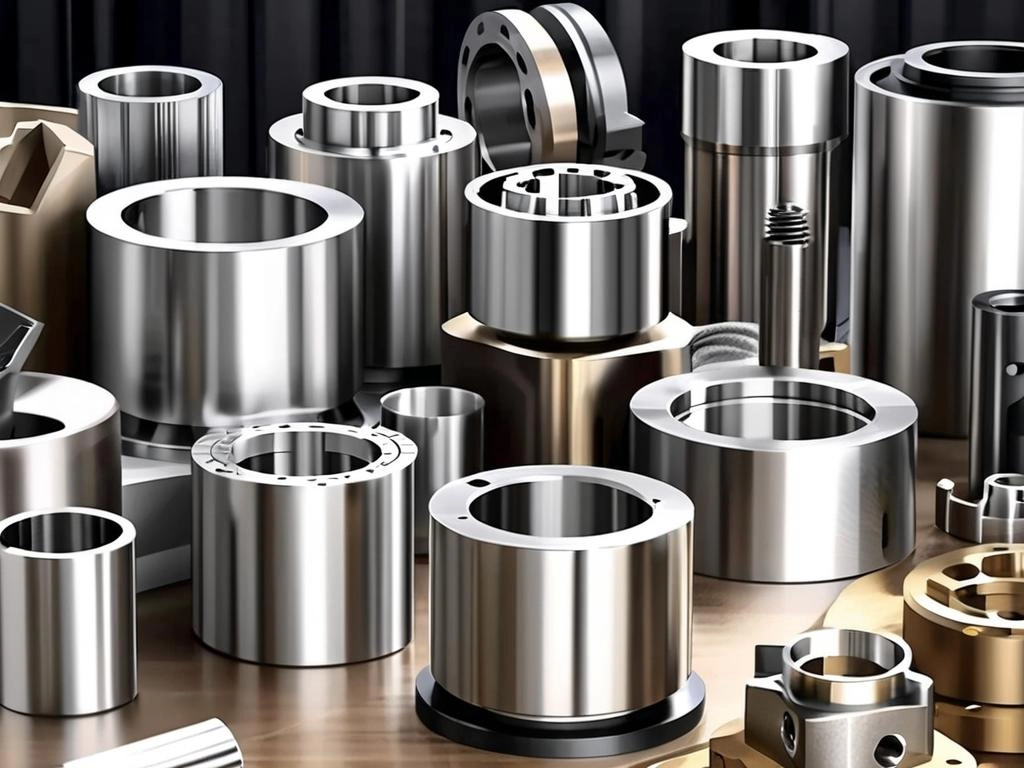
Semiconductor Part Machining: Enabling Technological Advancements
The Significance of Semiconductor Part Machining
Semiconductor part machining plays a crucial role in the development and production of advanced electronic devices. Semiconductors are the building blocks of modern technology, powering everything from smartphones and computers to medical equipment and renewable energy systems. The machining of semiconductor parts involves precise fabrication of microstructures and circuits on semiconductor wafers, which requires extremely high levels of accuracy and cleanliness.
Challenges in Semiconductor Part Machining
One of the major challenges in semiconductor part machining is achieving sub-micron precision. The ever-increasing demand for smaller and more powerful electronic devices has led to the need for extremely fine features and tight tolerances. Additionally, maintaining a clean and dust-free environment is essential to prevent contamination of the semiconductor wafers, as even the tiniest particles can affect the performance of the final device. Another challenge is the selection of appropriate machining techniques and materials to ensure compatibility with the delicate nature of semiconductors.
Future Trends in Semiconductor Part Machining
As technology continues to advance, semiconductor part machining is expected to evolve as well. The development of new machining techniques, such as nano-machining and laser processing, will enable even higher levels of precision and efficiency. Moreover, the integration of artificial intelligence and machine learning algorithms into the machining process will help optimize tool paths, improve quality control, and reduce production costs. The future of semiconductor part machining holds great potential for further enhancing the performance and capabilities of electronic devices.
The Problem of Measuring Tools Inaccuracy: Causes and Solutions
Causes of Measuring Tools Inaccuracy
The inaccuracy of measuring tools, often referred to as "量具失准" in Chinese, can be caused by various factors. Wear and tear over time is a common cause, as the repeated use of measuring tools can lead to the degradation of their components and affect their accuracy. Environmental conditions, such as temperature, humidity, and vibration, can also have an impact on the performance of measuring tools. Incorrect calibration or improper handling by operators can further contribute to inaccuracies.
Effects of Measuring Tools Inaccuracy
The inaccuracy of measuring tools can have serious consequences in both CNC stainless steel machining and semiconductor part machining. In CNC machining, inaccurate measurements can lead to incorrect dimensions of the machined parts, resulting in poor fit and functionality. In semiconductor part machining, even a slight deviation in measurement can affect the performance and reliability of the final electronic device. Therefore, it is crucial to address the issue of measuring tools inaccuracy to ensure the quality and consistency of the manufacturing process.
Solutions to Measuring Tools Inaccuracy
To mitigate the problem of measuring tools inaccuracy, regular calibration and maintenance are essential. Measuring tools should be calibrated at regular intervals using traceable standards to ensure their accuracy. Additionally, operators should be trained to handle and use the measuring tools correctly, following proper procedures and guidelines. Environmental control measures, such as maintaining a stable temperature and humidity in the machining environment, can also help reduce the impact of environmental factors on the accuracy of measuring tools.
In conclusion, CNC stainless steel machining and semiconductor part machining are two critical manufacturing processes that require high precision and accuracy. The issue of measuring tools inaccuracy poses a significant challenge to the quality and reliability of these processes. By understanding the causes and effects of measuring tools inaccuracy and implementing appropriate solutions, manufacturers can ensure the production of high-quality components and contribute to the advancement of various industries. As technology continues to evolve, continuous improvement and innovation in machining techniques and quality control will be key to meeting the ever-increasing demands of modern manufacturing.