Office Of The State Council Safety Committee: Four Explosion Accidents Occurred In Aluminum Processing (deep Well Casting) Enterprises This Year, Resulting In 15 Deaths And 38 Injuries.
China News Service, September 27. According to the website of the Ministry of Emergency Management, the Office of the State Council Safety Committee released a report on production safety accidents in aluminum processing (deep well casting) enterprises this year.
The report stated that since this year, production safety accidents have occurred frequently in aluminum processing (deep well casting) enterprises (hereinafter referred to as enterprises). Four explosions have occurred, resulting in 15 deaths and 38 injuries. The situation of production safety is very serious. On August 31, molten aluminum exploded when exposed to water in the melting and casting workshop of Shanxi Southeast Precision Technology Co., Ltd. (hereinafter referred to as Southeast Precision) in Luliang City, Shanxi Province, causing 3 deaths and 10 injuries; on July 26, Zhongrui, Shangqiu City, Henan Province An explosion occurred in the deep casting workshop of Nonferrous Metal Materials Co., Ltd. (hereinafter referred to as Zhongrui Nonferrous Metals), killing 5 people and injuring 14 others. people. Injured; On July 9, an explosion occurred in the casting workshop of Fuzhou Fen'an Aluminum Co., Ltd. (hereinafter referred to as Fen'an Aluminum) in Fujian Province, killing two people and injuring one. On February 18, molten aluminum exploded when it encountered water in the smelting workshop of Nantong Asia-Pacific Light Alloy (Nantong) Technology Co., Ltd. (hereinafter referred to as Asia-Pacific Light Alloy), killing 5 people and injuring 13 others. These accidents have a great social impact, causing a large number of casualties and almost leading to major accidents. The lessons are profound and expose outstanding problems in enterprise safety management and government department safety supervision:
First, the concept of safe development is not firm and the emphasis is on production but not on safety. Some enterprises have weak awareness of production safety. When they discovered an abnormality in the equipment and failed to thoroughly investigate and repair it, they continued to work while sick and took risks, causing accidents. Before the "8·31" accident at Southeast Seiko, the cooling water pump relay was powered off and tripped many times. The company failed to thoroughly identify the cause of the trip, eliminate the fault, and continue to organize production. As a result, the cooling water was cut off and a large amount of uncooled and crystallized aluminum liquid flowed into the casting well. , explodes when exposed to water.
Second, the main person in charge of the company failed to perform his duties well, and there was a risk of major accidents. Since 2020, the Emergency Management Department has continued to carry out special rectification of the aluminum processing (deep well casting) industry, and has repeatedly emphasized that the main person in charge of the enterprise must personally organize learning and regularly investigate major accident risks. However, there are still some companies where the main leaders do not pay attention to, implement, or investigate. Governance is only a formality, but the potential for major accidents still exists. The Sino-Switzerland Nonferrous Metals "7.26" accident was caused by the company's failure to promptly investigate and discover the potential for major accidents in unqualified steel wire ropes. During the casting process, the steel wire rope broke, causing the spindle plate to become unstable and tilted. Liquid aluminum entered the casting well and exploded. The "8·31" accident of Southeast Precision exposed major accident risks such as the failure of cooling water temperature and pressure monitoring and alarms during the company's casting process, and the lack of interlocking of quick shut-off valves and return valves. Tilting control for tilting holding furnaces.
Third, there are prominent problems of corporate violations and employee violations, and on-site management is chaotic. Some violations may seem to be employees' problems, but in fact they are the result of company leaders not paying attention to safety, becoming paralyzed by chance, acquiescing to employees' illegal operations or even issuing orders in violation of regulations. In the Asia Pacific Light Alloy "2·18" accident, employees illegally used metal rods to insert between the formwork and the formwork to help separate them. When the partition is separated from the formwork instantaneously, the partition loses support and falls rapidly. A large amount of aluminum liquid in the formwork entered the deep well before it could cool down and crystallize. By the time of the accident, the illegal operations had continued for several months and hundreds of times; Fen'an Aluminum's "7·9" accident was due to the company's violation of operating procedures and the caster speeding up casting without authorization The speed will cause the liquid aluminum to explode when it encounters water if it is not cooled in time.
Fourth, the process layout is unreasonable and accident casualties increase. In order to facilitate production, many companies have set up sawing, heat treatment, inspection and other processes in their foundry workshops in addition to the casting process. As many as ten people were working on site at the same time. Because liquid aluminum explodes with great force when exposed to water, it often affects employees in other processes outside the core casting area. Accidents such as Asia Pacific Light Alloy, Zhongrui Nonferrous Metals, and Southeast Seiko all caused a large number of injuries to people outside the casting process.
Fifth, supervision and law enforcement are not strict, and hidden dangers have not been rectified to form a closed loop. The above-mentioned companies have all gone through multiple rounds of supervision and law enforcement but still have accidents, which exposes problems such as law enforcement officials’ inaccurate grasp of the standards for identifying major accident hazards and the lax closed loop of law enforcement inspections. . At the same time, there are still problems such as insufficient application and promotion of safety production risk monitoring and early warning systems for enterprises in key industrial and trade industries by grassroots regulatory authorities, and ineffective results.
In order to learn lessons from accidents, prevent and resolve major safety risks, and resolutely curb the trend of frequent accidents, the following requirements are hereby put forward:
First, we must firmly establish the concept of safe development. Coordinate development and security and strictly enforce security access. Industrial development and investment promotion must attach great importance to the safety risks of aluminum processing (deep well casting) processes. When formulating industrial planning and layout, strict enterprise entry thresholds must be met, and the unified construction of industrial plants must meet the requirements for the installation and use of advanced equipment. Strictly review the safety facility design of metal smelting enterprises, requiring enterprises to entrust a design unit with corresponding qualifications to prepare safety facility designs for new (renovation and expansion) projects, and will resolutely refuse approval for safety facility designs that do not meet the requirements. It is strictly prohibited to use fixed casting furnaces and wire rope lifting casting machines in new (renovation and expansion) construction projects. Enterprises are urged to fully identify safety risks and formulate effective control measures before new processes, new equipment are put into use, and new products are mass-produced. It is necessary to produce in small batches first, and then expand scale production after the equipment and technology are mature and stable. If safety is ensured, there will be no production. If hidden dangers are not rectified, there will be no production. If key equipment is not confirmed, there will be no production.
Second, we must improve the intrinsic safety level of enterprises. Enterprises are urged to optimize their process layout, set up a separate casting workshop or take hard isolation measures such as explosion-proof walls in the casting area; strengthen source control to ensure the procurement of casting furnaces, casting machines and other production equipment with qualified quality and safety conditions. Fully evaluate and demonstrate the production capacity of the equipment, and do not blindly pursue large templates and large quantities. Encourage the use of advanced process technologies and equipment and facilities with high intrinsic safety levels, high degree of automation, and fewer on-site workers. Enterprises that use steel wire ropes to lift casting machines are required to ensure that the safety factor of the steel core wire rope is not less than 5.6, and the lifting system should be equipped with a braking device and have a mechanical self-locking function. Enterprises that use hydraulic cylinders to lift casting machines must ensure that the hard connection between the hydraulic top plate and the partition bracket is intact and effective during the casting process. Urge enterprises to strictly ensure the cooling needs of castings, scientifically set the cooling pool capacity, and ensure clean water quality; increase the inlet pressure of the crystallizer cooling water, monitor the inlet water flow alarm signal, and interlock with the lowering of the casting machine lifting platform to ensure that casting operations automatically stop when abnormalities occur Casting.
Third, we must strengthen the implementation of the responsibilities of the main persons in charge of the enterprise. The main person in charge of the enterprise must have corresponding safety production knowledge and management capabilities, and must pass the assessment of the emergency management department. Supervise the main persons in charge of the enterprise to implement the first responsibility for safety, establish and improve the safety production responsibility system for all employees, strengthen safety education and training for all employees, formulate standards for identifying major accident hazards and identify safety risks, grasp the key points of safety training for all employees, and focus on employees in casting positions Conduct special safety education and training to familiarize them with the safety risks of casting operations and master emergency skills such as handling cooling water abnormalities. Supervise the main persons in charge of the enterprise to study and study the identification standards for major accident hazards, and carry out inspections and rectifications based on standards and forms; grasp the actual situation of casting operations through on-site spot inspections, inspection and monitoring, etc., and promptly discover and correct employees' "three violations"; establish and improve potential accident hazards The internal reporting reward system and public reporting channels encourage employees to discover hidden dangers and strengthen self-protection.
Fourth, we must strengthen casting operation site management. Supervise enterprises to ensure that key equipment and facilities are qualified and effective, and various interlocking devices operate reliably; strengthen the monitoring and monitoring of key parameters such as cooling water flow and temperature, pulling speed, aluminum liquid temperature; rationally set up emergency water sources to ensure that emergency water pressure and flow are met and time requirements. Urge enterprises to determine the number of employees and division of responsibilities in casting positions based on actual production conditions and strictly implement them; strengthen law enforcement inspections on employee duty status during the smelting and casting process, standardize operating behaviors, and strictly prohibit leaving work without authorization, sleeping, and skipping work, and unrelated personnel are strictly prohibited during casting Enter the workshop.
Fifth, ensure that monitoring is effective and available. Timely deploy the construction and application of safety production risk monitoring and early warning systems for enterprises in key industrial and trade industries, and promote enterprises to have data access conditions as soon as possible and go online as required. Supervise enterprises to test safety interlocking devices before each casting operation to ensure that flow meters, liquid level gauges, quick shut-off valves, emergency discharge valves, etc. are intact and effective; monitoring alarm and safety interlocking data should be kept for no less than 1 month. It is strictly prohibited to turn off or covertly shield monitoring alarms and safety interlocks by setting unreasonable alarm parameter values, delaying action times, etc.
Sixth, we must strengthen on-site handling and emergency drills. Enterprises are urged to formulate realistic emergency plans and on-site disposal plans, improve employees' on-site emergency response, danger avoidance and escape capabilities, conduct evacuation drills every six months, and conduct drill assessments and rectifications. Supervise enterprises to focus on handling abnormal situations on site. If abnormal working conditions such as aluminum leakage, cooling water cutoff, wire rope burnt by molten aluminum, spindle plate and formwork cannot be separated naturally, etc., production must be stopped decisively and personnel evacuated. What cannot be handled must be handled promptly. .
All localities are requested to promptly notify all relevant types of enterprises in their jurisdictions of the above requirements, strengthen safety supervision and law enforcement, and urge enterprises to implement self-inspections. Conduct a thorough survey of the aluminum industry concentrated areas and enterprises within the administrative region, and master basic information such as scale, equipment level, product type, number of personnel, etc., so as to have a clear understanding of the situation. In accordance with the three-year action requirements, we must continue to promote the dynamic cleanup of major accident hazards and solve the root causes of safety production. Carry out key law enforcement inspections on the performance of the main persons in charge of the company, typical accident exposure issues, large templates, many counts, and long casting rods; carry out key law enforcement inspections through on-site law enforcement inspections, casting operation video review, and risk management. , through online inspections of the monitoring and early warning system, promote enterprises to standardize business behaviors, identify potential risks, and severely crack down on violations of laws and regulations. Typical accidents will be listed for supervision and upgraded investigation; areas where production safety accidents occur must strictly follow the "four no-misses" principle, complete accident investigations in a timely manner, notify warnings in a timely manner, and promote the entire industry to learn lessons from the accidents.
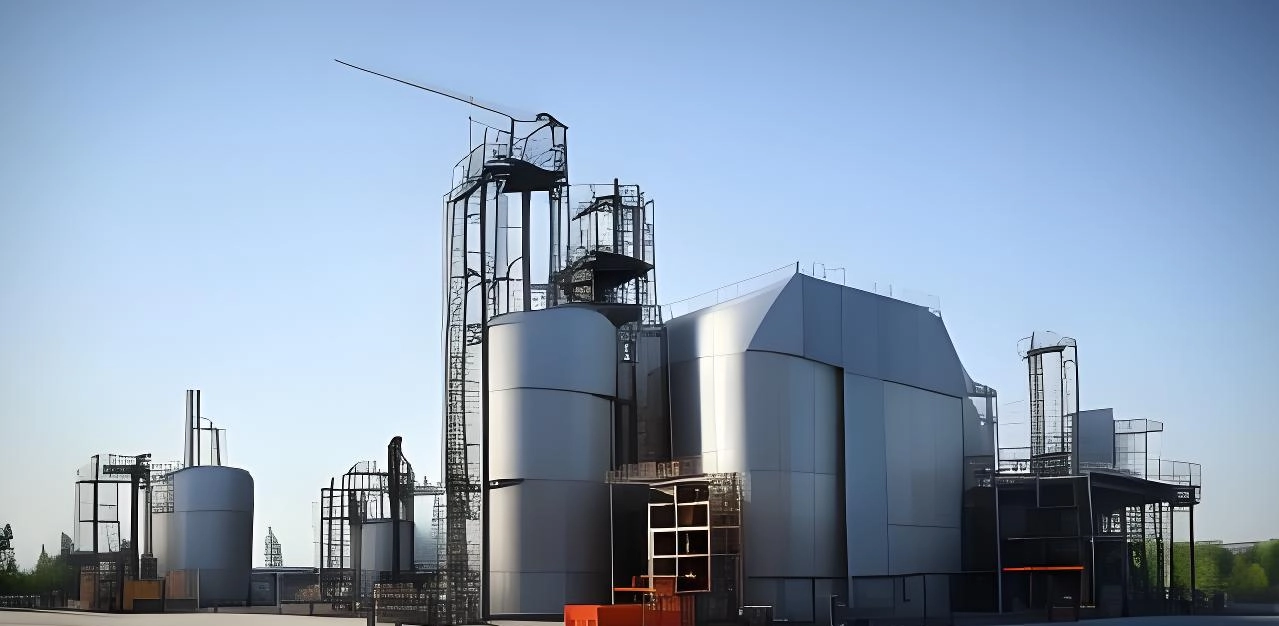