Rare Top-level Mechanical Technology: The Original Metal Production And Processing Process Is Like This
Today we will discuss metal processing technology.
1. The core of this technology lies in how to use various tools and mechanical equipment to transform metal into different shapes and structures. It is widely used in modern manufacturing, construction engineering and high-precision industrial fields. The scope of metal processing is very broad, covering areas such as welding, cutting, steel recycling and machine parts production.
2. Welding technology is a common method of joining metals. The key is to effectively form a long-lasting, strong joint. With the continuous development of industry, metal processing technology is constantly updated, and the process becomes more efficient and faster. Especially driven by automation and intelligence, production efficiency has been greatly improved. Now let’s take a look at some of the unique metal processing techniques in the world.
- First of all, friction welding is an important technology. Welding or joining plays a vital role in infrastructure construction. Friction welding produces high-quality joints and can handle many different shapes of metals. The technology is particularly suitable for applications with high strength requirements, such as the aerospace and automotive industries. Friction welding uses advanced technology to generate the required heat through rotating friction between metals. The basic principle is that the friction heat generated by controlling the contact pressure and rotation speed of the metal can quickly heat the contact surface of the metal to a molten state, thereby achieving an effective connection. . Friction welding is a simpler process and takes significantly less time than traditional welding. During this process, the operator prepares and secures the piece of metal to be welded to specialized equipment and places another piece of metal on a rotating device. Place two pieces of metal parallel to each other and the rotating device will spin at a specific speed. . The heat from friction quickly heats and melts both ends of the metal, eventually joining them together to form a strong connection. After welding is completed, the connected parts need to be processed with an automatic grinder to ensure their smoothness and precision. The advantages of friction welding are significant savings in material and welding time. It is more efficient than other welding methods, often resulting in higher weld quality and less material waste. This is particularly important in the current context of resource shortages.
- So let's look at the hot spinning machine. This type of equipment is specifically used for metal forming. It uses a combination of heat and rotation to quickly process metal products of various sizes. It is widely used in parts manufacturing in automobile, aviation and other industries. Before processing can begin, the metal needs to be heated to a set temperature. The process typically uses efficient heaters or burners to ensure the metal reaches the required forming temperature quickly. The hot metal is then spun through burners and shaped into a predetermined pattern, ensuring precision and consistency in the final product.
——Next let’s talk about the manufacturing process of liquefied gas bottles. This process mainly includes two steps: bottle making and welding, which is an important link to ensure the safe storage and transportation of liquefied gas.
- In the production process of liquefied gas cylinders, the processed steel is first formed into cylindrical steel plates and then processed into semi-finished gas cylinders through an automatic forming machine. The modern production line uses automated equipment to ensure production efficiency and quality consistency.
- This semi-finished product of the gas cylinder is divided into upper and lower parts. The lower part will be processed by automated equipment to provide the required support position for the liquefied gas cylinder. This design ensures that the gas cylinder can be placed upright safely and stably during use.
- Then drill some holes in the upper part of the cylinder to install the valve. The selection and installation of valves are crucial and are directly related to the safety performance of gas cylinders.
- During the welding process, a cap and valve will be installed on the upper end of the liquefied gas bottle and sealed to avoid leakage of liquefied gas.
- After welding is completed, a metal plate is installed on the outside of the cylinder as a supporting structure to ensure the stability of the cylinder during transportation and storage.
- Next, connect the upper and lower parts by welding to form a complete liquefied gas bottle. The gas cylinders produced will undergo strict quality inspection to ensure they meet national standards.
- Let's look at the manufacturing of wind turbine fuselages. The process involves assembling multiple steel plates to form large wind turbines. Wind turbines are important equipment in the field of renewable energy, and their manufacturing process must ensure the safety and durability of their structures.
- Shape the prepared steel plate into the required curve through a bending machine to adapt to the design requirements of the wind turbine.
- Formed steel plates are connected together by welding to form a huge cylindrical structure with excellent wind resistance.
- The structure is then transported to subsequent processing using a forklift, ensuring that no damage is caused to the structure during handling.
- In a subsequent step, the cylinders are welded together to form the complete wind turbine body. The fineness of the welding process directly affects the performance of the turbine, so advanced welding technology and equipment must be used.
- Once completed, the fuselage will be sent to a paint shop to prevent problems caused by corrosion.
- The spraying process is not only for aesthetics, but also to provide an extra layer of protection and extend the service life of the equipment.
- In the final steps, the painted airframe will be fitted with internal components including electric motors, generators, etc. These components are critical to the proper operation of the wind turbine.
- Finally, let's talk about recycling machines. Recycling is a method of converting waste materials into new products. Recycling equipment plays a vital role in this, helping to reduce environmental pollution and promote the sustainable use of resources. In the field of recycling, there is a German company called Wema, which focuses on the research and development of recycling technology. WM has advanced experience in recycling technology and has demonstrated a high level of expertise in handling complex materials. WM produces many types of recycling equipment, each with its own specific functions. They can process steel, paper and plastic efficiently and are widely used in recycling plants around the world, greatly contributing to global environmental protection. The recycling process is relatively simple. First, the recycled materials need to be sorted manually. This step ensures the efficiency and accuracy of subsequent automated processing. After sorting is complete, the material is placed into recycling equipment and shredded through a tool called a "shredder." Not only can crushers process large amounts of material quickly, but they can also control the size of the particles for subsequent processing. The materials processed by the crusher will be heated, pressed, and cut to form new materials to provide high-quality raw materials for subsequent production. The materials processed by recycling equipment can be converted into new raw materials, which can be used in future industrial production and promote the process of sustainable development.
Finally, don’t forget to like, retweet and follow the video. See you in the next video.
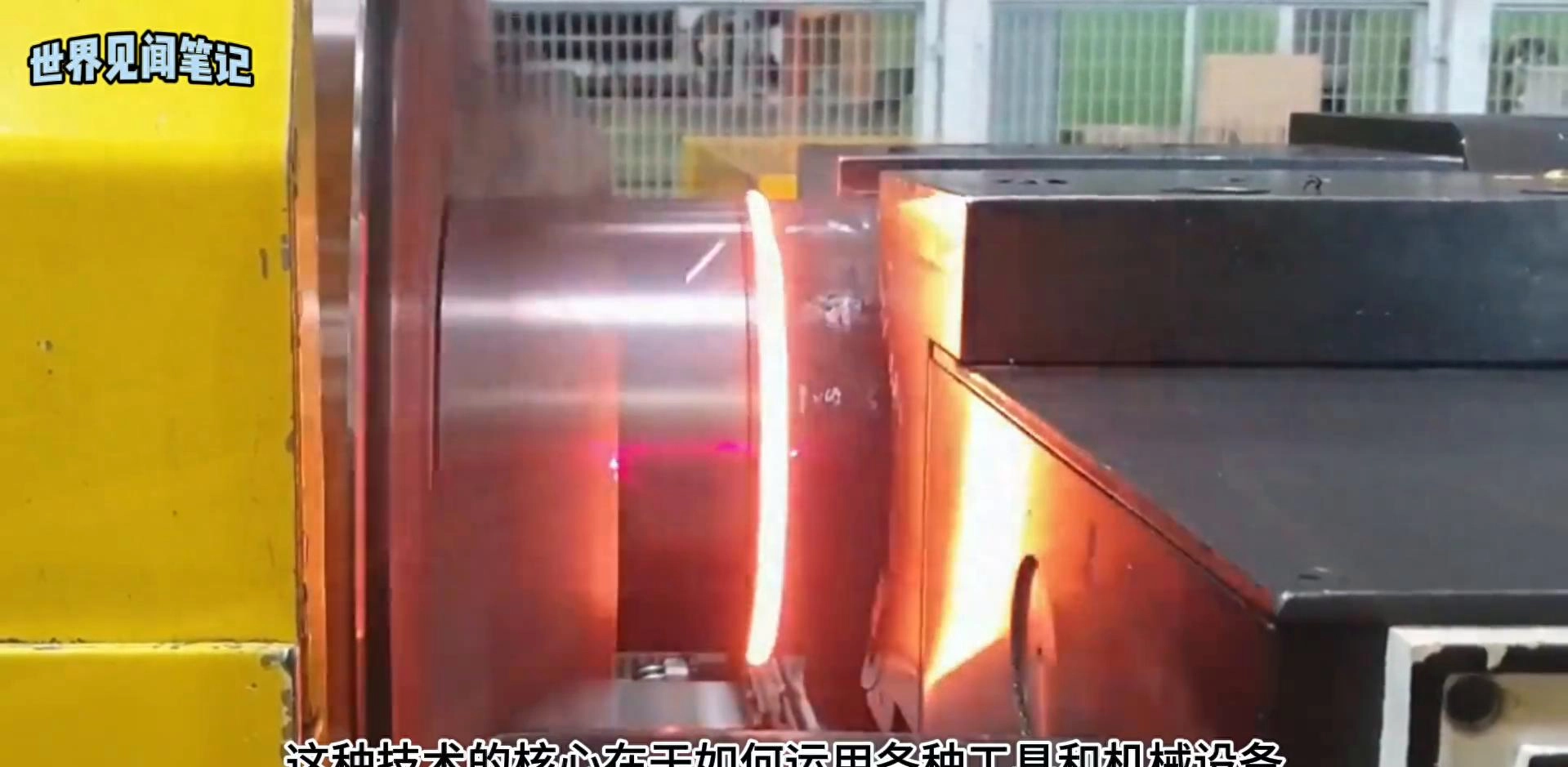