0.1 Micron! More Than Accurate Machining Tools Are Here
Text|China Science Daily Reporter Wang Correspondent Yang Yuxin
Multi-sensor built-in measurement. Photos provided by the National Defense University
Breakthroughs in processing and application technologies of basic components of ultra-precision machine tools can provide strong technical support for the survival and development of the manufacturing industry. However, our country's ultra-precision machine tools and key basic components mainly rely on imports.
The external roundness treatment of domestic and foreign axes is basically achieved through ultra-precise outer cylindrical grinding stone. Taking the grinding shaft core with a diameter of 100 mm and a length of 300 mm as an example, my country's cylindrical grinders can roughly grind 1 to 2 microns, while the foreign level can reach 0.3 to 0.5 microns.
To solve the technical problems of machine tools and key components, Dai Yifan, a professor of technology at the National Defense University, has improved the roundness accuracy of shaft core machining and has been successfully developed. Exporting ultra-accurate air-static spindles. Recently, it has been used to export a super-accurate air-static spindle. , After testing by the China Institute of Index Science, the relevant parameters of the static pressure spindle have reached the international advanced level, which will effectively improve the ultra-precision processing accuracy of our country. Relevant research results have been published in "Materials" and "Micromechanical".
Grind super-precision parts, such as shovels
For the ultra-precision machines and key basic components in our country, the biggest technical problem is the lack of a "working host" that deals with core parts, that is, a machine that produces machines and machinery, also known as tool machines, including lathes, grinders, Planers, drilling machines, etc. are the basis for manufacturing tools and industrial self-improvement.
General mechanical processing is the process of "copying" the machine tool accuracy into parts, that is, without high-precision machine tools, it is impossible to process parts with high precision. Without high-precision parts, high-precision components and machine tools cannot be assembled. Without a working host that produces high-precision parts, it will limit the development of the entire ultra-precision machine tool industry.
Dai Yifan's team has long been engaged in the research and development of modern optical manufacturing technology. They found that the final manufacturing accuracy of optical parts far exceeds that of the processing equipment used, and the fundamental principle of optical manufacturing is to gradually eliminate the accuracy of the high points of error. The team attempted to use this “precision evolution” principle processing method for high-precision processing of mechanical parts. Finally, through innovation in machining principles, it proposes a deterministic shape shaping technology for the outer circularity of shaft parts, breaking through the limitations of high-precision "working mother machine".
How does the refining process of deterministic shapes work? “It’s like leveling a piece of land with a shovel, i.e., removing the right amount of soil in a place that looks uneven and repeating it until a very flat land is obtained.” Dai Yifan said the process relies on a complete set of digital devices, Including obtaining a high-precision circular instrument for cylindrical morphology, a grinding machine that implements digitized material removal, and a dedicated computer program that can obtain time-dwelling at specific spatial locations grinding tools.
Machinery replaces experienced workers
With the help of the new process, Dai Yifan’s team broke into time-controlled grinding processing based on the principle of precision evolution, forming a comprehensive process approach for the built-in processing and detection of cylindrical parts and successfully developed Super-precision air pressure spindle.
The test results of the China Institute of Index Science show that the radial bounce of the air-static pressure spindle is less than 15 nanometers CNC inquiry, and the end surface bounce is less than 15 nanometers. This jump is equivalent to one-six thousandth of the diameter of the hair. If it is the main axis of the earth, the amplitude caused by rotational motion will not exceed 1 meter.
The test results show that the radial static stiffness of the air static pressure spindle is greater than 200 N/m, and the axial static stiffness is greater than 200 n/m. In layman's terms, the spindle can remain motionless under a gravity load of 20 kg and deform no more than 1 micron, which is one percent of the hair diameter. Comparison of product manuals representing the highest level of companies in the field of ultra-precision in the United States, the above technical indicators can be with or even higher.
At present, the outer circularity of shaft parts can be processed and at a level of several microns at home and abroad. If you want to improve it, you can only rely on manual grinding and trimming. “Our new technology can get rid of the dependence on experienced workers and masters and can easily organize production according to modern industrial models, thereby facilitating the mass production and application of ultra-precision basic components,” Dai Yifan said. Ultra-precision. Breakthroughs in processing and application technologies of basic machine tools will provide strong technical support for the survival and development of manufacturing industry, improve the support facilities of the high-end machine tool industrial chain, thereby greatly improving the competitiveness of high-performance functional components and promoting high-end accuracy. and localization of ultra-precision machines.
Dai Yifan added that these breakthroughs will also effectively solve the problems of ultra-precision equipment and core processes for ultra-precision processing of critical components for inspection and guidance, further aiding in the mass production of ultra-precision processing of high-end core parts and enabling science. A rapid shift in research results.
Related paper information:
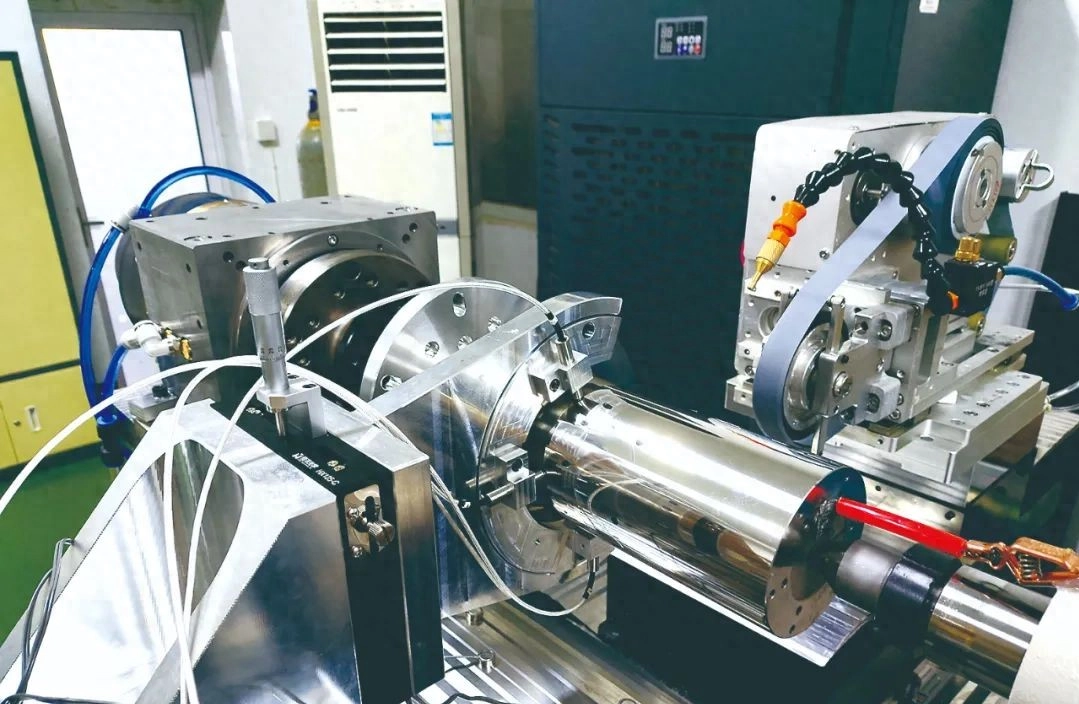