Reasonably Select Tool Cutting Parameters In Stainless Steel Cutting Processing
In stainless steel cutting processing, the rational selection of tool cutting parameters is crucial to ensure processing quality and efficiency. Here are detailed analysis of cutting parameters such as cutting speed, cutting depth, cutting width and feed speed, as well as recommendations for selecting tool material and geometric parameters:
1. Cutting speed
The cutting speed directly affects the cutting efficiency and cutting surface quality and must be set with caution. The cutting speed of stainless steel should be adjusted appropriately according to factors such as its hardness, material and processing method. Generally speaking, the cutting speed of stainless steel can be selected within the range of /min. In actual operation, the recommended cutting speed provided by the tool manufacturer should be adjusted appropriately according to actual processing conditions. It should be noted that when dealing with stainless steel, the cutting speed will be slightly increased, the cutting temperature will be higher, the tool wear will be intensified, and the durability will be greatly reduced, so the cutting speed should be appropriately reduced, usually 40% of ordinary carbon steel to 60% of the choice.
2. Cutting depth
Since the hardness of stainless steel is relatively high, the cutting depth is slightly smaller than that of ordinary steel. The cutting depth should not be too large, otherwise the cutting force will be increased, which will easily cause tool damage and workpiece deformation. Generally speaking, the cutting depth can be controlled at about 1/2 of the tool diameter or not more than 3 mm. Specific values should be fully considered based on factors such as the power of the machining center, the strength and stiffness of the tool, and the material of the workpiece.
3. Cutting width
The setting of the cutting width will directly affect the processing accuracy and processing efficiency. Similar to the cutting depth, the cutting width of stainless steel is usually smaller than that of ordinary steel. Excessive cutting width can lead to excessive cutting forces, which can easily lead to workpiece deformation and degradation of surface quality. Generally, the cutting width can be controlled between 1/2 and 1/3 of the tool diameter.
4. Eating speed
During the process of stainless steel, an appropriate feeding speed can keep the machining center stable and ensure processing efficiency. The selection of feed speed should be fully considered based on parameters such as cutting speed, cutting depth and cutting width. Under normal circumstances, the feeding speed of the stainless steel machining center can be adjusted within a certain range, such as 515 mm/min (or 0.050.35 mm/r). In actual operation, appropriate adjustments should be made based on factors such as the performance of the machining center, the durability of the tool, and the machining requirements of the workpiece. At the same time, it should be noted that the feeding volume must not be less than 0.1 mm/r and micro-rated quantities are avoided to avoid cutting in the working hardened zone.
5. Tool material selection
Cutting stainless steel requires harder tool materials such as cemented carbides (including tungsten-pectin alloys and tungsten-copper-grain titanium alloys) and high-speed steels. These tool materials have strong wear and tensile strength, which can effectively extend the service life of the tool and improve processing efficiency. Among them, carbides have become the first choice material for stainless steel processing milling cutters due to their high hardness, wear resistance, strength and toughness and good thermal conductivity.
6. Select tool geometry parameters
Selecting the geometry of the tool cut parts (such as front angle, back angle, edge inclination angle, etc.) also has an important influence on the processing effect.
1. Front angle: When ensuring that the knife has sufficient strength, a larger front angle should be selected. This not only reduces the plastic deformation of the cut metal, but also reduces the cutting force and cutting temperature while also reducing the depth of the hardened layer. For stainless steel, the roughness range of the front angle is 10°~30°. During roughing, smaller values are occupied and larger values are obtained during finishing.
2. Rear Angle: Increasing the rear angle reduces friction between the backhand surface and the machining surface, but reduces the strength and heat dissipation of the tip. Therefore, it is necessary to avoid making the rear corner choice too small or too large. When cutting stainless steel, most of the rear angle values of the cemented carbide tool are roughly processed at 40° to 60°, and are slightly greater than 60° during finishing.
3. Blade inclination: To increase the strength of the tool tip, the blade inclination angle is usually -20°-60° when cutting stainless steel. During intermittent cutting, λs is smaller, usually -50°-150°.
7. Use of cutting fluid
During stainless steel processing, cutting fluid should be used to reduce tool wear and maintain processing quality. Common cutting fluids include water-soluble cutting fluids and oil-based cutting fluids. Among them, the water-soluble cutting liquid not only has excellent cutting performance, but also reduces the risk of environmental pollution. However, it should be noted that when using coated carbide tools, water-soluble cutting fluids should be avoided to avoid cutting due to excessive thermal stress.
In short, the rational selection of cutting parameters in stainless steel cutting processing is a complex and meticulous process, and a variety of factors need to be considered comprehensively. By scientifically selecting cutting parameters as well as appropriate tool material and geometric parameters CNC company, the efficiency and quality of stainless steel processing can be significantly improved.
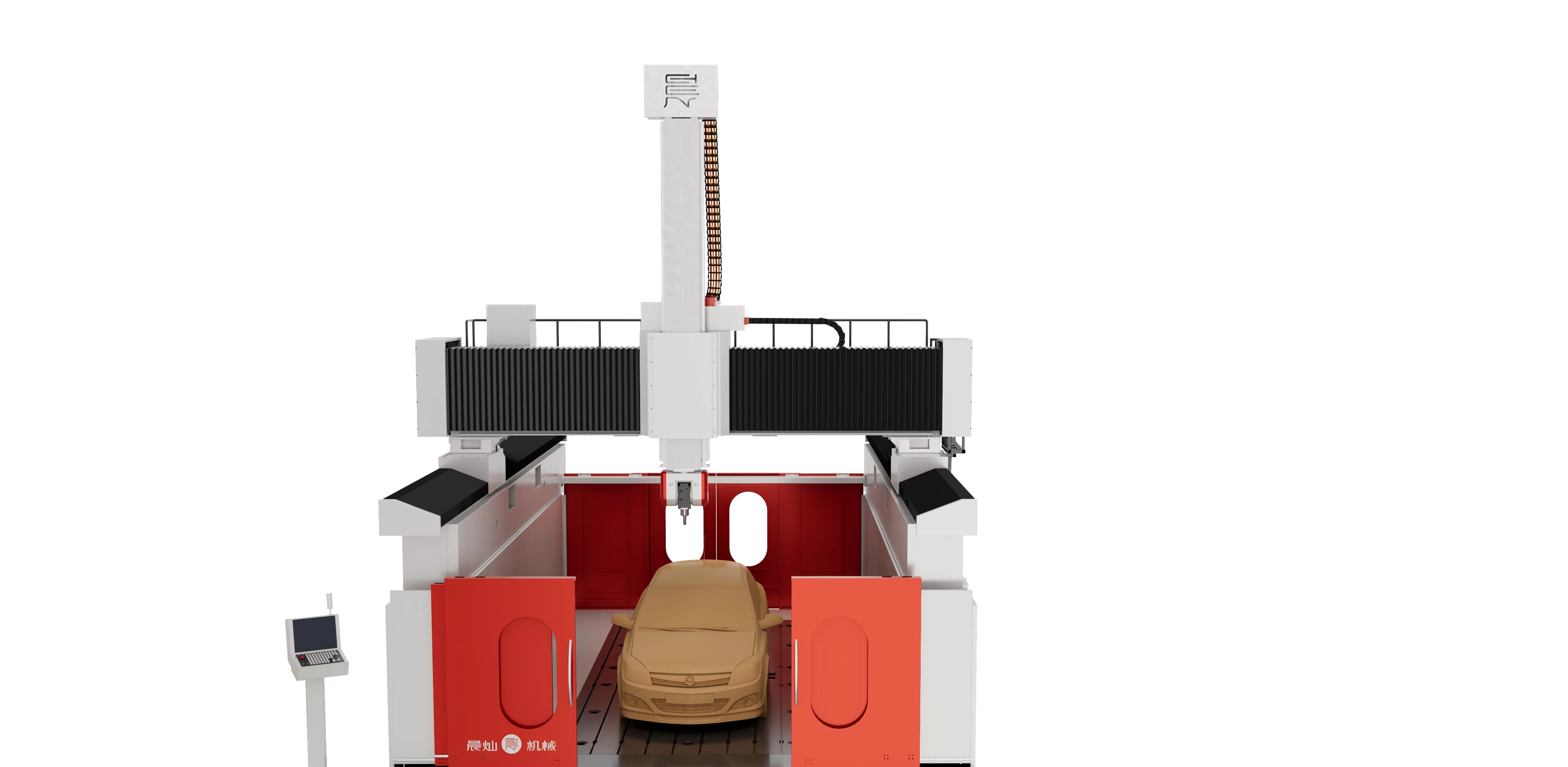